Polrvinyl chloride alloy material and preparation method
A technology of polyvinyl chloride and alloy materials, applied in the field of metal materials, can solve problems such as self-crosslinking of compatibilizers, and achieve the effects of good comprehensive mechanical properties, low cost, and simple methods
- Summary
- Abstract
- Description
- Claims
- Application Information
AI Technical Summary
Problems solved by technology
Method used
Examples
Embodiment 1
[0018] A polyvinyl chloride alloy material is made of the following components by weight:
[0019] Polyvinyl chloride: 30 parts; ABS resin: 10 parts; manganese dioxide: 0.2 parts; anhydrous calcium chloride: 0.2 parts; dioctyl terephthalate: 1 part; magnesium stearate: 10 parts; stearin Potassium acid: 10 parts.
[0020] The preparation method of polyvinyl chloride alloy material comprises the following steps:
[0021] (1) Mix the materials uniformly in proportion, and then grind the uniformly mixed materials into fine powder;
[0022] (2) Melting the ground material at a temperature of 150° C. to 200° C., granulating, and drying to obtain a polyvinyl chloride alloy material.
[0023] The polyvinyl chloride alloy material provided by the invention has good comprehensive mechanical properties, greatly improved tensile strength, elongation at break and impact strength, and has important industrial application prospects. The invention adopts reaction mixing in-situ compatibili...
Embodiment 2
[0025] A polyvinyl chloride alloy material is made of the following components by weight:
[0026] Polyvinyl chloride: 80 parts; ABS resin: 50 parts; manganese dioxide: 0.8 parts; anhydrous calcium chloride: 0.8 parts; dioctyl terephthalate: 5 parts; magnesium stearate: 20 parts; stearin Potassium acid: 20 parts.
[0027] The preparation method of polyvinyl chloride alloy material comprises the following steps:
[0028] (1) Mix the materials uniformly in proportion, and then grind the uniformly mixed materials into fine powder;
[0029] (2) Melting the ground material at a temperature of 150° C. to 200° C., granulating, and drying to obtain a polyvinyl chloride alloy material.
[0030] The polyvinyl chloride alloy material provided by the invention has good comprehensive mechanical properties, greatly improved tensile strength, elongation at break and impact strength, and has important industrial application prospects. The invention adopts reaction mixing in-situ compatibil...
Embodiment 3
[0032] A polyvinyl chloride alloy material is made of the following components by weight:
[0033] Polyvinyl chloride: 60 parts; ABS resin: 30 parts; manganese dioxide: 0.5 parts; anhydrous calcium chloride: 0.5 parts; dioctyl terephthalate: 3 parts; magnesium stearate: 15 parts; stearin Potassium acid: 15 parts.
[0034] The preparation method of polyvinyl chloride alloy material comprises the following steps:
[0035] (1) Mix the materials uniformly in proportion, and then grind the uniformly mixed materials into fine powder;
[0036] (2) Melting the ground material at a temperature of 150° C. to 200° C., granulating, and drying to obtain a polyvinyl chloride alloy material.
[0037] The polyvinyl chloride alloy material provided by the invention has good comprehensive mechanical properties, greatly improved tensile strength, elongation at break and impact strength, and has important industrial application prospects. The invention adopts reaction mixing in-situ compatibil...
PUM
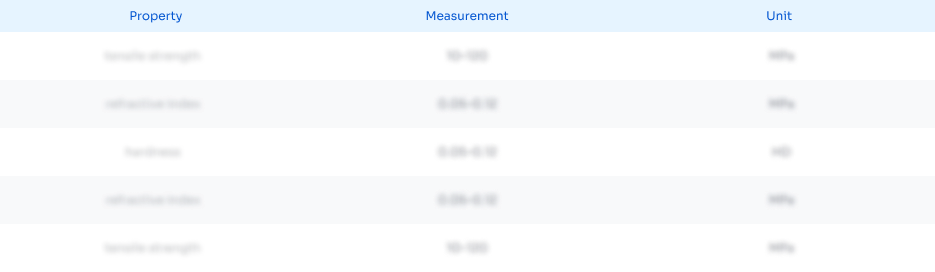
Abstract
Description
Claims
Application Information

- R&D
- Intellectual Property
- Life Sciences
- Materials
- Tech Scout
- Unparalleled Data Quality
- Higher Quality Content
- 60% Fewer Hallucinations
Browse by: Latest US Patents, China's latest patents, Technical Efficacy Thesaurus, Application Domain, Technology Topic, Popular Technical Reports.
© 2025 PatSnap. All rights reserved.Legal|Privacy policy|Modern Slavery Act Transparency Statement|Sitemap|About US| Contact US: help@patsnap.com