Preparation method of light-resistant waterborne polyurethane
A technology of water-based polyurethane and light resistance, applied in the field of preparation of water-based polyurethane, can solve the problems of lack of rigid benzene ring, low hardness of water-based polyurethane coating film, poor water resistance and solvent resistance, etc. low cost effect
- Summary
- Abstract
- Description
- Claims
- Application Information
AI Technical Summary
Problems solved by technology
Method used
Examples
example 1
[0018] (1), in the 500ml four-neck flask that stirring blade, thermometer, condenser tube are housed, polytetrahydrofuran ether glycol 10.0g is mixed with isophorone diisocyanate 35.5g, dibutyltin dilaurate catalyst 0.07g Under the condition of existence, stirred and reacted at 70°C for 2 hours to obtain 45.3g of polyurethane prepolymer;
[0019] (2), add hydrophilic chain extender dimethylol propionic acid 2.02g in the polyurethane prepolymer, the stirring reaction time is 30min, add tetrakis hydroxymethyl phosphorus sulfate 0.09g and carry out cross-linking, the stirring reaction time is 30min, Add 4.5g of butanone solvent, stir and react at 70°C for 1.0h, add 3.05g of triethylamine for neutralization, stir for 40min, add 150g of water for emulsification, and obtain 202.5g of hydrophilic polyurethane with a solid content of 24.9%. Transfer to the 500ml beaker for subsequent use;
[0020] (3), emulsifying agent 10g is dissolved in 50g water, adds nano iron oxide 2g, 2,4-dihy...
example 2
[0023] (1), in the 500ml four-neck flask that stirrer blade, thermometer, condensation pipe are housed, polytetrahydrofuran ether glycol 10.0g is mixed with hexamethylene diisocyanate 67.2g, dibutyltin dilaurate catalyst 0.31g Under the condition of existence, stir and react at 90°C for 4h to obtain 77.5g polyurethane prepolymer;
[0024] (2), add hydrophilic chain extender dimethylol butyric acid 10.71g in polyurethane prepolymer, stirring reaction time is 60min, add trimethylolpropane 0.62g to carry out cross-linking, stirring reaction time is 30min, add Butanone solvent 23.3g, stirred and reacted at 90°C for 3.5h, added 5.22g of triethylamine for neutralization, stirred for 60min, added 150g of water for emulsification, and obtained 267.4g of hydrophilic polyurethane with a solid content of 33.2%. into the 500ml beaker for subsequent use;
[0025] (3), sodium dodecylbenzene sulfonate 10g is dissolved in 50g water, adds nano silicon dioxide 5g, o-hydroxybenzoic acid phenyl ...
example 3
[0028] (1), in the 500ml four-necked flask that stirring blade, thermometer, condenser tube are housed, polytetrahydrofuran ether glycol 10.0g is mixed with isophorone diisocyanate 62.2g, dibutyltin dilaurate catalyst 0.20g Under the condition of existence, stir and react at 80°C for 3 h to obtain 72.3 g of polyurethane prepolymer;
[0029] (2), add hydrophilic chain extender dimethylol propionic acid 6.2g in polyurethane prepolymer, stirring reaction time is 45min, continue to add tetrakis hydroxymethyl phosphorus sulfate 0.36g, stirring reaction time is 30min, add butyl Ketone 14.5g, stirred and reacted at 80°C for 2 hours, added 4.9g of triethylamine for neutralization, stirred and reacted for 50min, added 160g of water for emulsification, formed 257.9g of water-based polyurethane with a solid content of 32.3%, transferred to a 500ml beaker in standby;
[0030] (3), sodium hexametaphosphate 10g is dissolved in 50g water, adds nano-zinc oxide 3.5g, phenyl o-hydroxybenzoate ...
PUM
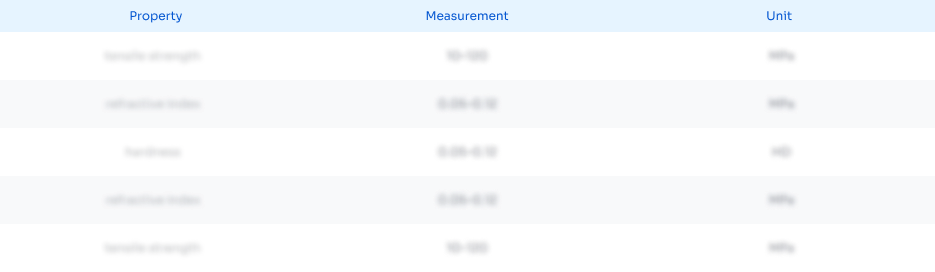
Abstract
Description
Claims
Application Information

- R&D
- Intellectual Property
- Life Sciences
- Materials
- Tech Scout
- Unparalleled Data Quality
- Higher Quality Content
- 60% Fewer Hallucinations
Browse by: Latest US Patents, China's latest patents, Technical Efficacy Thesaurus, Application Domain, Technology Topic, Popular Technical Reports.
© 2025 PatSnap. All rights reserved.Legal|Privacy policy|Modern Slavery Act Transparency Statement|Sitemap|About US| Contact US: help@patsnap.com