Friction material composition for ceramic brake pad
A friction material and brake pad technology, applied in the field of friction material composition, can solve the problems of easy rust, unstable performance and high heat transfer of materials for brake pads
- Summary
- Abstract
- Description
- Claims
- Application Information
AI Technical Summary
Problems solved by technology
Method used
Image
Examples
Embodiment 1
[0016] Example 1: 14% of mullite ceramic fiber, 10% of sprayed aluminum silicate fiber, 10% of aramid pulp, 9% of red copper fiber, 9% of potassium titanate whisker, and 3% of nano-iron oxide according to mass percentage , aluminum hydroxide 0.8%, barite 7%, potassium feldspar 8%, chromite 3%, magnesium hydroxide 1%, zinc oxide 0.2%, graphite particles 7%, expanded graphite 6%, nitrile rubber 2 %, cashew nut shell oil modified phenolic resin 10% is put into a high-speed disperser, stirred into powder, taken out and put into a forming mold for pressing and forming, and then compounded with a steel back, put into a flat vulcanizing machine at a high temperature of 270°C, and the pressure is Under the condition of 18MPa, keep it for 15 minutes, then take out the brake pad and remove the burr to become the finished product.
Embodiment 2
[0017] Example 2: 18% of mullite ceramic fiber, 13% of sprayed aluminum silicate fiber, 10% of aramid pulp, 8% of red copper fiber, 8% of potassium titanate whisker, and 3% of nano-iron oxide according to mass percentage , aluminum hydroxide 0.8%, barite 7%, potassium feldspar 8%, chromite 3%, magnesium hydroxide 1%, zinc oxide 0.2%, graphite particles 7%, expanded graphite 6%, nitrile rubber 1 %, cashew nut shell oil modified phenolic resin 6% is put into a high-speed disperser, stirred into powder, taken out and put into a forming mold for pressing and forming, and then compounded with a steel back, put into a flat vulcanizer at a high temperature of 270°C, and the pressure is Under the condition of 18MPa, keep it for 15 minutes, then take out the brake pad and remove the burr to become the finished product.
Embodiment 3
[0018] Example 3: 16% of mullite ceramic fiber, 11.5% of sprayed aluminum silicate fiber, 11% of aramid pulp, 8.5% of red copper fiber, 8% of potassium titanate whisker, and 3% of nano-iron oxide according to mass percentage , aluminum hydroxide 0.8%, barite 9%, potassium feldspar 8%, chromite 3%, magnesium hydroxide 1%, zinc oxide 0.2%, graphite particles 7%, expanded graphite 6%, nitrile rubber 1 %, cashew nut shell oil modified phenolic resin 6% is put into a high-speed disperser, stirred into powder, taken out and put into a forming mold for pressing and forming, and then compounded with a steel back, put into a flat vulcanizer at a high temperature of 270°C, and the pressure is Under the condition of 18MPa, keep it for 15 minutes, then take out the brake pad and remove the burr to become the finished product.
PUM
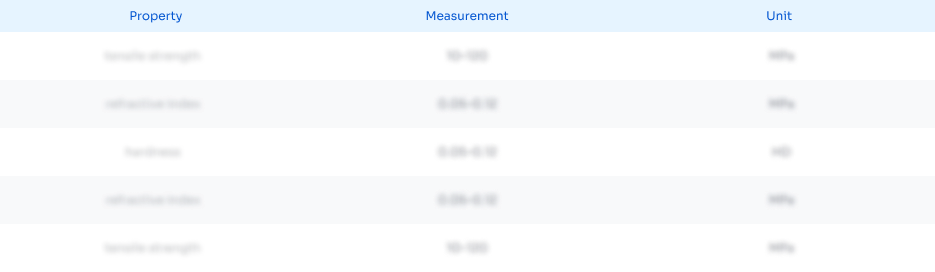
Abstract
Description
Claims
Application Information

- R&D
- Intellectual Property
- Life Sciences
- Materials
- Tech Scout
- Unparalleled Data Quality
- Higher Quality Content
- 60% Fewer Hallucinations
Browse by: Latest US Patents, China's latest patents, Technical Efficacy Thesaurus, Application Domain, Technology Topic, Popular Technical Reports.
© 2025 PatSnap. All rights reserved.Legal|Privacy policy|Modern Slavery Act Transparency Statement|Sitemap|About US| Contact US: help@patsnap.com