Flange for wind power drum and manufacturing technique thereof
A manufacturing process and technology of using flanges, applied in the direction of flange connection, pipe/pipe joint/pipe fitting, passing element, etc., can solve the problem of low tensile strength and high yield strength, not meeting the requirements of wind tower use, flange The problem of low corrosion resistance is to achieve the effect of improved toughness and low temperature impact performance, obvious reduction of defects and consistent performance
- Summary
- Abstract
- Description
- Claims
- Application Information
AI Technical Summary
Problems solved by technology
Method used
Image
Examples
Embodiment 1
[0024] The flange for the wind power tower of the present embodiment, the mass percent of its chemical composition is: C: 0.15%, Si: 0.65%, Mn: 0.65%, Ni: 6%, Cr: 4%, Nb: 0.85%, Cu: 0.35%, N: 0.05%, Mo: 0.06%, Al: 0.7%, S: 0.02%, Ti: 0.09%, V: 0.01%, B: 0.002%, lanthanide rare earth: 1%, the balance is Fe; The mass percentages of lanthanide rare earth components are: lanthanum: 25%, cerium: 19%, samarium: 5%, neodymium: 13%, gadolinium: 11%, praseodymium: 10%, dysprosium: 9%, and other lanthanide elements: 8%.
[0025] The manufacturing process of the flange for wind power tower in this embodiment is carried out according to the following procedures: billet blanking-forging-forging size and surface inspection-heat treatment-mechanical rough machining-ultrasonic inspection-mechanical performance test-mechanical finishing to the required shape and size-clean coating; among them, billet blanking, forging, forging size and surface inspection, mechanical rough machining, ultrasoni...
Embodiment 2
[0032] The wind power tower flange of the present embodiment, the mass percent of its chemical composition is: C: 0.22%, Si: 0.60%, Mn: 0.75%, Ni: 5%, Cr: 5%, Nb: 0.65%, Cu: 0.25%, N: 0.07%, Mo: 0.05%, Al: 0.9%, S: 0.02%, Ti: 0.08%, V: 0.03%, B: 0.002%, lanthanide rare earth: 2%, the balance is Fe; The mass percentages of lanthanide rare earth components are: lanthanum: 35%, cerium: 16%, samarium: 10%, neodymium: 10%, gadolinium: 5%, praseodymium: 15%, dysprosium: 7%, and other lanthanide elements: 2%.
[0033] The manufacturing process of the flange for wind power tower in this embodiment is carried out according to the following procedures: billet blanking-forging-forging size and surface inspection-heat treatment-mechanical rough machining-ultrasonic inspection-mechanical performance test-mechanical finishing to the required shape and size-clean coating; among them, billet blanking, forging, forging size and surface inspection, mechanical rough machining, ultrasonic inspec...
Embodiment 3
[0040]The wind power tower flange of the present embodiment, the mass percent of its chemical composition is: C: 0.19%, Si: 0.55%, Mn: 0.70%, Ni: 8%, Cr: 6%, Nb: 0.75%, Cu: 0.45%, N: 0.06%, Mo: 0.07%, Al: 0.8%, S: 0.03%, Ti: 0.09%, V: 0.04%, B: 0.003%, lanthanide rare earth: 2%, the balance is Fe; The mass percentages of lanthanide rare earth components are: lanthanum: 26%, cerium: 18%, samarium: 9%, neodymium: 12%, gadolinium: 12%, praseodymium: 13%, dysprosium: 8%, and other lanthanide elements: 2%.
[0041] The manufacturing process of the flange for wind power tower in this embodiment is carried out according to the following procedures: billet blanking-forging-forging size and surface inspection-heat treatment-mechanical rough machining-ultrasonic inspection-mechanical performance test-mechanical finishing to the required shape and size-clean coating; among them, billet blanking, forging, forging size and surface inspection, mechanical rough machining, ultrasonic inspect...
PUM
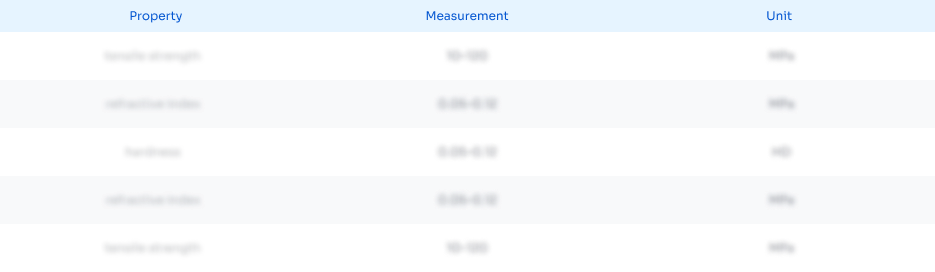
Abstract
Description
Claims
Application Information

- R&D
- Intellectual Property
- Life Sciences
- Materials
- Tech Scout
- Unparalleled Data Quality
- Higher Quality Content
- 60% Fewer Hallucinations
Browse by: Latest US Patents, China's latest patents, Technical Efficacy Thesaurus, Application Domain, Technology Topic, Popular Technical Reports.
© 2025 PatSnap. All rights reserved.Legal|Privacy policy|Modern Slavery Act Transparency Statement|Sitemap|About US| Contact US: help@patsnap.com