Method for pretreating indium-containing zinc oxide acid supernatant
A zinc oxide and pretreatment technology, applied in the direction of improving process efficiency, can solve the problems of inability to carry out extraction and high impurity content, and achieve the effects of simplifying indium recovery process, improving indium recovery rate, and reducing consumption
- Summary
- Abstract
- Description
- Claims
- Application Information
AI Technical Summary
Problems solved by technology
Method used
Image
Examples
Embodiment 1
[0044] The composition of the indium-containing zinc oxide supernatant of the present invention is: In 3+ 0.92g / L, Bi 3+ 0.12g / L, Sn 2+ 0.11g / L, SiO 2 0.36g / L, Fe 2+ 20.83g / L, Fe 3+ 23.71g / L, Cu 2+ 0.73g / L, Zn 2+ 87.36g / L, As 3+ 1.59g / L, Cl - 0.89g / L,H 2 SO 4 71.53g / L.
[0045] Step 1: Reduction: Add the zinc sulfide concentrate after ball milling to the constantly stirring indium-containing zinc oxide supernatant, and the addition amount of the zinc sulfide concentrate is Fe 3+ All reduced to Fe 2+ The theoretical dosage is 1.0 times, the reduction temperature is 95°C, and the time is 2 hours. After filtration, the reduction solution and reduction slag are obtained, and the reduction slag returns to the zinc system to recover zinc. The main components of the reducing solution are: In 3+ 0.91g / L, Fe 2+ 40.15g / L, Fe 3+ 4.78g / L, Zn 2+ 98.35g / L, Bi 3+ 0.13g / L, Sn 2+ 0.11g / L, SiO 2 0.34g / L, Cu 2+ 0.78g / L, As 3+ 1.51g / L, Cl - 0.93g / L,H 2 SO ...
Embodiment 2
[0051] The composition of the supernatant containing indium zinc oxide acid of the present embodiment is: In 3+ 0.92g / L, Bi 3+ 0.12g / L, Sn 2+ 0.11g / L, SiO 2 0.36g / L, Fe 2+ 20.83g / L, Fe 3+ 23.71g / L, Cu 2+ 0.73g / L, Zn 2+ 87.36g / L, As 3+ 1.59g / L, Cl - 0.89g / L,H 2 SO 4 71.53g / L.
[0052] Step 1: Reduction: Add the zinc sulfide concentrate after ball milling to the constantly stirring indium-containing zinc oxide supernatant, and the addition amount of the zinc sulfide concentrate is Fe 3+ All reduced to Fe 2+ The theoretical dosage is 1.2 times, the reduction temperature is 85°C, and the time is 3.5 hours. After filtration, the reduction solution and reduction residue are obtained, and the reduction residue zinc return system recovers zinc. The main components of the reducing solution are: In 3+ 0.91g / L, Fe 2+ 41.08g / L, Fe 3+ 3.92g / L, Zn 2+ 99.15g / L, Bi 3+ 0.13g / L, Sn 2+ 0.12g / L, SiO 2 0.38g / L, Cu 2+ 0.81g / L, As 3+ 1.65g / L, Cl - 0.97g / L,H ...
Embodiment 3
[0058] The composition of the supernatant containing indium zinc oxide acid of the present embodiment is: In 3+ 0.92g / L, Bi 3+ 0.12g / L, Sn 2+ 0.11g / L, SiO 2 0.36g / L, Fe 2+ 20.83g / L, Fe 3+ 23.71g / L, Cu 2+ 0.73g / L, Zn 2+ 87.36g / L, As 3+ 1.59g / L, Cl - 0.89g / L,H 2 SO 4 71.53g / L.
[0059] Step 1: Reduction: Add the zinc sulfide concentrate after ball milling to the constantly stirring indium-containing zinc oxide supernatant, and the addition amount of the zinc sulfide concentrate is Fe 3+ All reduced to Fe 2+ The theoretical dosage is 1.3 times, the reduction temperature is 75°C, and the time is 5 hours. After filtration, the reduction solution and reduction slag are obtained, and the reduction slag returns to the zinc system to recover zinc. The main components of the reducing solution are: In 3+ 0.90g / L,Fe 2+ 41.54g / L, Fe 3+ 3.16g / L, Zn 2+ 99.83g / L, Bi 3+ 0.14g / L, Sn 2+ 0.13g / L, SiO 2 0.41g / L, Cu 2+ 0.91g / L, As 3+ 1.64g / L, Cl - 0.98g / L,H ...
PUM
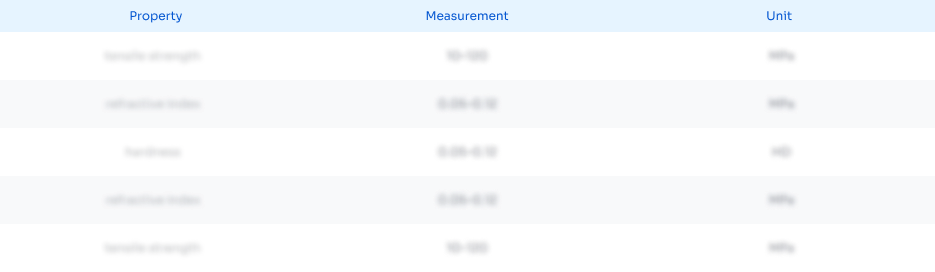
Abstract
Description
Claims
Application Information

- Generate Ideas
- Intellectual Property
- Life Sciences
- Materials
- Tech Scout
- Unparalleled Data Quality
- Higher Quality Content
- 60% Fewer Hallucinations
Browse by: Latest US Patents, China's latest patents, Technical Efficacy Thesaurus, Application Domain, Technology Topic, Popular Technical Reports.
© 2025 PatSnap. All rights reserved.Legal|Privacy policy|Modern Slavery Act Transparency Statement|Sitemap|About US| Contact US: help@patsnap.com