Strengthening-toughening glass ceramic and preparation method thereof
A glass-ceramic and toughening technology, applied in the field of strengthening and toughening glass-ceramic and its preparation, can solve the problems of poor toughening effect, difficulty in densification, and performance degradation.
- Summary
- Abstract
- Description
- Claims
- Application Information
AI Technical Summary
Problems solved by technology
Method used
Image
Examples
Embodiment 1
[0022] Prepare toughened glass ceramics according to the following steps: (1) Weigh according to the mass ratio: 60% SiO 2 , 29.4% Li 2 CO 3 , 3.69% of K 2 CO 3 , 2.75% AL 2 o 3 , 1.53% CeO 2 and 3.0% P 2 o 5 A total of 500g is used as an ingredient for subsequent use.
[0023] (2) SiO 2 , Li 2 CO 3 、K 2 CO 3 ,,AL 2 o 3 , CeO 2 ,P 2 o 5 Pour it into a ball mill jar, add 300ml of absolute ethanol, wet ball mill for 8 hours, mix evenly, put it in an oven, and dry it at 80°C for 24 hours to obtain a mixed powder.
[0024] (3) Preheat the quartz crucible in a resistance furnace, pour the mixed powder into the preheated quartz crucible, heat up to 1450°C at a rate of 10 / min, and melt at 1450°C in a program-controlled resistance furnace for 2 hours; Quickly pour into deionized water and quench to obtain glass particles. The obtained glass particles were placed in an agate ball mill jar, added with 300 ml of absolute ethanol and ball milled for 12 hours, and dried...
Embodiment 2
[0027] Prepare toughened glass ceramics according to the following steps: prepare glass powder according to the method in Example 1, mix the glass powder and zirconia powder evenly to form a mixture, wherein the mass percentage of zirconia in the mixture is 2%, The glass powder is the balance; the mixture is put into a prefabricated mold box, and subjected to cold isostatic pressing (250MPa) to form a green body. Carry out crystallization heat treatment on the above green body, start from room temperature to 700°C, the heating rate is 10°C / min, after 5 hours at 700°C, heat up to 900°C, after 5 hours of heat preservation, cool with the furnace, and the toughness is completed Preparation of glass ceramics.
Embodiment 3
[0029] Prepare toughened glass ceramics according to the following steps: prepare glass powder according to the method in Example 1, mix the glass powder and zirconia powder evenly to form a mixture, and the mass percentage of zirconia in the mixture is 3%, The glass powder is the balance; the mixture is put into a prefabricated mold box, and subjected to cold isostatic pressing (250MPa) to form a green body. Carry out crystallization heat treatment on the above green body, start from room temperature to 700°C, the heating rate is 10°C / min, after 5 hours at 700°C, heat up to 900°C, after 5 hours of heat preservation, cool with the furnace, and the toughness is completed Preparation of glass ceramics.
PUM
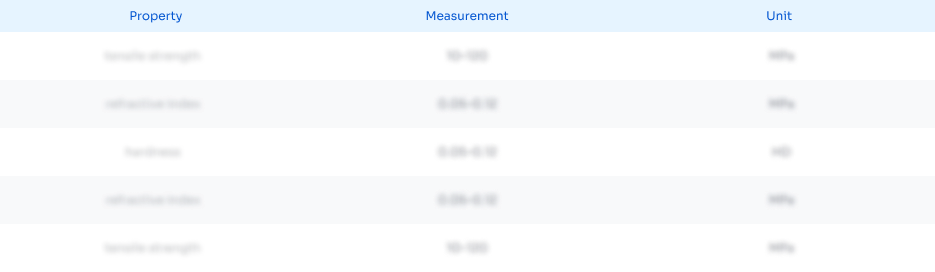
Abstract
Description
Claims
Application Information

- R&D
- Intellectual Property
- Life Sciences
- Materials
- Tech Scout
- Unparalleled Data Quality
- Higher Quality Content
- 60% Fewer Hallucinations
Browse by: Latest US Patents, China's latest patents, Technical Efficacy Thesaurus, Application Domain, Technology Topic, Popular Technical Reports.
© 2025 PatSnap. All rights reserved.Legal|Privacy policy|Modern Slavery Act Transparency Statement|Sitemap|About US| Contact US: help@patsnap.com