Production technology of aluminum alloy sectional bar for automobile bumper
A technology of aluminum alloy profiles and automobile bumpers, which is applied in the field of metal machining, can solve the problems of high price, complex forming process, low toughness and impact strength, etc., and achieve the effect of eliminating external conditions, chemical composition and uniform temperature
- Summary
- Abstract
- Description
- Claims
- Application Information
AI Technical Summary
Problems solved by technology
Method used
Image
Examples
Embodiment Construction
[0030] The present invention is used for the aluminum alloy profile production process of automobile bumper, comprises the following steps;
[0031] (1) Ingredients: Aluminum ingot of 99.85 grade is selected as the base of the alloy. Mg and Zn elements are added in the form of pure metals. Considering that Cu, Cr, Ti, and Zr elements have high melting points and low content in the alloy, they are added in the form of master alloys.
[0032] (2) Smelting: smelting in a 25-ton regenerative gas furnace. Considering that the alloy contains a relatively high Zn content and the melting point of Zr is high, it is easy to produce specific gravity segregation and feather crystals of Zn and Zr, so the following measures are taken: In order to prevent To produce feather crystals, the smelting temperature should not be too high, which is 755°C;
[0033](3) In order to prevent the specific gravity segregation of Zn and Zr, add the Zn ingots into the furnace in three batches with a feeding...
PUM
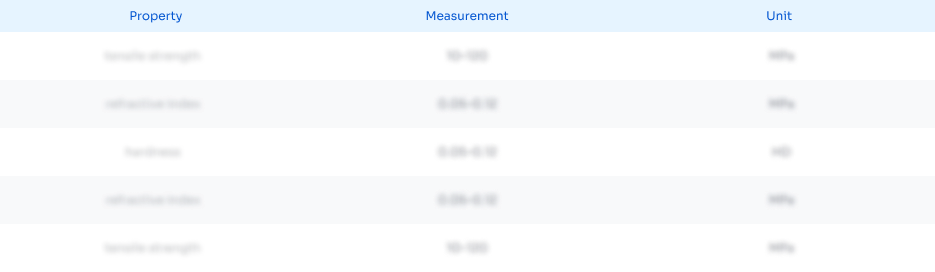
Abstract
Description
Claims
Application Information

- R&D
- Intellectual Property
- Life Sciences
- Materials
- Tech Scout
- Unparalleled Data Quality
- Higher Quality Content
- 60% Fewer Hallucinations
Browse by: Latest US Patents, China's latest patents, Technical Efficacy Thesaurus, Application Domain, Technology Topic, Popular Technical Reports.
© 2025 PatSnap. All rights reserved.Legal|Privacy policy|Modern Slavery Act Transparency Statement|Sitemap|About US| Contact US: help@patsnap.com