Coating material for modified bitumen waterproof roll material surface and preparation method
A technology of waterproofing membrane and modified asphalt, applied in the direction of antifouling/underwater paint, coating, paint containing biocide, etc., can solve inappropriate, increase the labor intensity of construction workers, building load and material cost, Increase labor intensity and comprehensive costs
- Summary
- Abstract
- Description
- Claims
- Application Information
AI Technical Summary
Problems solved by technology
Method used
Image
Examples
Embodiment 1
[0129] 1. Raw material composition of film forming agent
[0130] The proportioning ratio of the first component is:
[0131] 20.0 parts by weight of deionized water;
[0132] The proportioning ratio of the second component is:
[0133] 3.0 parts by weight of deionized water, 0.2 parts by weight of potassium persulfate, 0.1 parts by weight of sodium lauryl sulfate and 0.1 parts by weight of alkylphenol polyoxyethylene ether;
[0134] The proportioning ratio of the third component is:
[0135] 18.0 parts by weight of deionized water, 0.1 parts by weight of potassium persulfate, 0.4 parts by weight of sodium lauryl sulfate, 0.5 parts by weight of alkylphenol polyoxyethylene ether and 0.4 parts by weight of anhydrous sodium sulfate;
[0136] The proportioning ratio of the fourth component is:
[0137] 40.0 parts by weight of butyl acrylate, 1.0 parts by weight of methacrylic acid, 12.0 parts by weight of styrene and 3.0 parts by weight of octamethylcyclotetrasiloxane;
[013...
Embodiment 2
[0155] 1. Raw material composition of film forming agent
[0156] The proportioning ratio of the first component is:
[0157] 18.0 parts by weight of deionized water;
[0158] The proportioning ratio of the second component is:
[0159] 5.0 parts by weight of deionized water, 0.2 parts by weight of sodium persulfate, 0.1 parts by weight of sodium dodecylbenzenesulfonate and 0.1 parts by weight of nonylphenol polyoxyethylene ether;
[0160] The proportioning ratio of the third component is:
[0161] 18.0 parts by weight of deionized water, 0.1 parts by weight of sodium persulfate, 0.4 parts by weight of sodium dodecylbenzenesulfonate, 0.5 parts by weight of nonylphenol polyoxyethylene ether and 0.4 parts by weight of anhydrous sodium carbonate;
[0162] The proportioning ratio of the fourth component is:
[0163] 30.0 parts by weight of butyl acrylate, 1.0 parts by weight of acrylic acid, 11.0 parts by weight of styrene and 5.0 parts by weight of dimethylcyclosiloxane;
[...
Embodiment 3
[0182] 1. Raw material composition of film forming agent
[0183] The proportioning ratio of the first component is:
[0184] 20.0 parts by weight of deionized water;
[0185] The proportioning ratio of the second component is:
[0186] 4.0 parts by weight of deionized water, 0.2 parts by weight of potassium persulfate, 0.1 parts by weight of sodium lauryl sulfate and 0.1 parts by weight of alkylphenol polyoxyethylene ether;
[0187] The proportioning ratio of the third component is:
[0188] 17.0 parts by weight of deionized water, 0.1 parts by weight of potassium persulfate, 0.4 parts by weight of sodium lauryl sulfate, 0.5 parts by weight of alkylphenol polyoxyethylene ether, 0.2 parts by weight of polyvinyl alcohol and 0.2 parts by weight of acrylamide;
[0189] The proportioning ratio of the fourth component is:
[0190] 35.0 parts by weight of butyl acrylate, 7.0 parts by weight of methyl methacrylate, 1.0 parts by weight of methacrylic acid, 10.0 parts by weight of ...
PUM
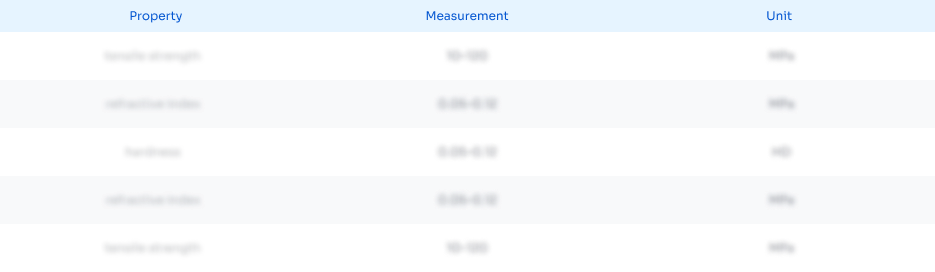
Abstract
Description
Claims
Application Information

- R&D Engineer
- R&D Manager
- IP Professional
- Industry Leading Data Capabilities
- Powerful AI technology
- Patent DNA Extraction
Browse by: Latest US Patents, China's latest patents, Technical Efficacy Thesaurus, Application Domain, Technology Topic, Popular Technical Reports.
© 2024 PatSnap. All rights reserved.Legal|Privacy policy|Modern Slavery Act Transparency Statement|Sitemap|About US| Contact US: help@patsnap.com