Flame-retardant glass fiber reinforced PA6 (polyamide 6)/PPO (P-Polyphenylene Oxide) alloy material and preparation method thereof
A technology of alloy materials and glass fiber, which is applied in the field of PA6/PPO alloy materials, can solve the problems of unsuitable electricity environment, low CTI value and GWIT value, etc., achieve high tracking index, improve processing fluidity, and reduce friction The effect of the coefficient
- Summary
- Abstract
- Description
- Claims
- Application Information
AI Technical Summary
Problems solved by technology
Method used
Image
Examples
Embodiment 3
[0029] A method for preparing environmentally friendly flame retardant glass fiber reinforced PA6 / PPO alloy material with high CTI value and high GWIT value, the method is as follows: Weigh raw materials according to weight ratio: PA6 23%, PPO 22%, compound flame retardant 20%, antimony trioxide 4.3%, glass fiber 20%, commercially available maleic anhydride grafted PPO 10%, antioxidant (1330) 0.1%, iron oxide 0.6%; put into high mixer and mix for 2 minutes, The material is discharged, and then extruded and granulated with a twin-screw extruder, the processing temperature is 240° C., and the screw rotation speed is 300 rpm.
[0030] The compound flame retardant is compounded by our company itself, and is composed of three components, and its mass percentage is BPS: 50%; magnesium hypophosphite: 25%; talcum powder: 25%.
Embodiment 4
[0032] A high CTI value, high GWIT value environmentally friendly flame retardant glass fiber reinforced PA6 / PPO alloy material preparation method, the method is as follows: Weigh raw materials according to weight ratio: PA6 46%, PPO 20%, compound flame retardant 6 %, antimony trioxide 3%, glass fiber 21%, commercially available maleic anhydride grafted PPO 2%, antioxidant (1330) 1%, iron oxide 1%; put into the high mixer and mix for 5 minutes, and the The material is then extruded and granulated with a twin-screw extruder, the processing temperature is 240° C., and the screw speed is 400 rpm.
[0033] The compound flame retardant is compounded by our company itself, and is composed of three components, and its mass percentage is BPS: 50%; magnesium hypophosphite: 25%; talcum powder: 25%.
[0034] The glass fiber is an alkali-free glass fiber, and the glass fiber is added into the silane coupling agent to make its surface treated with the silane coupling agent.
Embodiment 5
[0036] A high CTI value, high GWIT value environmentally friendly flame retardant glass fiber reinforced PA6 / PPO alloy material preparation method, the method is as follows: Weigh raw materials according to weight ratio: PA6 25%, PPO 41%, compound flame retardant 6 %, antimony trioxide 5%, glass fiber 20%, commercially available maleic anhydride grafted PPO 2%, antioxidant (1330) 0.5%, iron oxide 0.5%; The material is then extruded and granulated with a twin-screw extruder, the processing temperature is 240° C., and the screw speed is 350 rpm.
[0037] The compound flame retardant is compounded by our company itself, and is composed of three components, and its mass percentage is BPS: 50%; magnesium hypophosphite: 25%; talcum powder: 25%.
PUM
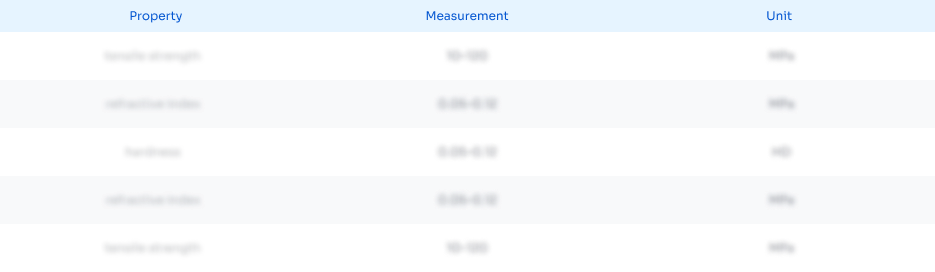
Abstract
Description
Claims
Application Information

- R&D
- Intellectual Property
- Life Sciences
- Materials
- Tech Scout
- Unparalleled Data Quality
- Higher Quality Content
- 60% Fewer Hallucinations
Browse by: Latest US Patents, China's latest patents, Technical Efficacy Thesaurus, Application Domain, Technology Topic, Popular Technical Reports.
© 2025 PatSnap. All rights reserved.Legal|Privacy policy|Modern Slavery Act Transparency Statement|Sitemap|About US| Contact US: help@patsnap.com