Method for replacing helium atoms on film layer
A chlorine atom, film layer technology, used in the manufacture of discharge tubes, electrical components, semiconductor/solid state devices, etc.
- Summary
- Abstract
- Description
- Claims
- Application Information
AI Technical Summary
Problems solved by technology
Method used
Image
Examples
Embodiment Construction
[0024] In order to further set forth the technical means and effects that the present invention takes to achieve the purpose of the predetermined invention, below in conjunction with the accompanying drawings and preferred embodiments, its specific implementation, structure, Features and their functions are described in detail below.
[0025] Please refer to figure 1 , which is a flow chart of the steps of the method for replacing chlorine atoms on the film layer in an embodiment of the present invention, the method includes the following steps S11-S14:
[0026] In step S11, a carrier with a film layer is placed into the cavity, and the surface of the film layer has several chlorine atoms. In this embodiment, step S11 is continued after the carrier with the film layer is etched by plasma as mentioned in the background art. Wherein, the film layer may be a metal layer, a semiconductor layer or an insulating layer.
[0027] In step S12, a first gas and a second gas are inject...
PUM
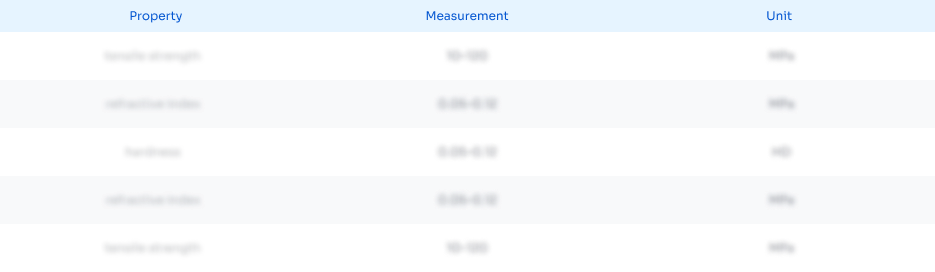
Abstract
Description
Claims
Application Information

- R&D
- Intellectual Property
- Life Sciences
- Materials
- Tech Scout
- Unparalleled Data Quality
- Higher Quality Content
- 60% Fewer Hallucinations
Browse by: Latest US Patents, China's latest patents, Technical Efficacy Thesaurus, Application Domain, Technology Topic, Popular Technical Reports.
© 2025 PatSnap. All rights reserved.Legal|Privacy policy|Modern Slavery Act Transparency Statement|Sitemap|About US| Contact US: help@patsnap.com