Hydrometallurgical process and method for recovering metals
A metal and valuable metal technology, applied in rare earth metal fluorides, chemical instruments and methods, rare earth metal compounds, etc., to achieve the effect of reducing demand, reducing reactant costs and transportation requirements, and reducing operating costs
- Summary
- Abstract
- Description
- Claims
- Application Information
AI Technical Summary
Problems solved by technology
Method used
Image
Examples
Embodiment A
[0141] Example A is the determination of a multi-stage precipitation and ion exchange process for the removal of divalent and trivalent cations prior to salt splitting treatment. Figure 4 and Figure 5 The reduction of divalent alkaline earth metal (especially magnesium, calcium, strontium and barium) and trivalent (lanthanum, cerium, praseodymium, neodymium, samarium and iron) cations after each precipitation and ion exchange stage are shown, respectively.
[0142] M1 is the first precipitation stage ( image 3 ), wherein a salt solution having a pH of about pH 7 (e.g., the by-product salt solution 224, the metal value-depleted salt solution 216, or a combination thereof (combined solution 228) as described above) contacts a Sodium carbonate solution at a pH of about pH 9.5 to form a metal carbonate slurry. Sodium carbonate was dissolved in water with stirring to form the sodium carbonate solution. The metal carbonate slurry has metal carbonate precipitates dispersed in b...
Embodiment B
[0148] Embodiment B is trivalent cation in chelating ion exchange resin ( image 3 Determination of load capacity on IX1) in. The chelating ion exchange resin evaluated was an iminodiacetate based resin sold under the trademark Amberlite IRC-748i by Rohm & Haas. The trivalent cation is lanthanum. By adding about 400 mg of lanthanum oxide (La 2 o 3 ) was dissolved in hydrochloric acid (about 3.7 ml of 2N HCl) to obtain a pH of about pH 4, about 50 g / L NaCl and 83 mg / L lanthanum (as LaCl 3) of the lanthanum feed solution. After dissolving the lanthanum oxide, about 200 grams of NaCl was added, the pH was adjusted to about pH 4 with 1 N NaOH and deionized water was added to give a final volume of about 4 liters. The column was packed with Amberlite IRC-748i. The lanthanum feed solution was passed through the packed column at a rate of about 2.05 mL / min at about 21 degrees Celsius (see Figure 6 ). The maximum trivalent cation capacity of the iminodiacetoxy resin was deter...
Embodiment C
[0150] Example C is the determination of the removal capacity of trivalent cations supported on IX1 resin in Example B. The resin tested was an iminodiacetoxy functional resin sold by Rohm & Haas under the trademark Amberlite IRC-748i. The trivalent cation is lanthanum. About 108 mg of lanthanum was supported on a resin column containing about 4 grams of Amberlite 748i. The lanthanum-supported column was regenerated with a hydrochloric acid solution having a normality of about 2.6N at a flow rate of about 2.7 mL / min. Fractions were collected approximately every 5 minutes. The first 5 fractions contained detectable amounts of lanthanum (see Figure 7 ). The first 5 fractions contained a total of 104 mg lanthanum, which was within experimental error of 108 mg lanthanum loaded on the column. The second fraction had the highest lanthanum concentration of about 7.5 g / L. Fractions beyond the fifth fraction did not contain any detectable amount of lanthanum. From this example,...
PUM
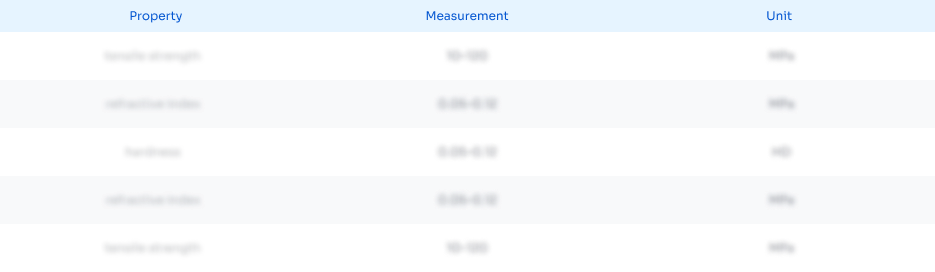
Abstract
Description
Claims
Application Information

- R&D Engineer
- R&D Manager
- IP Professional
- Industry Leading Data Capabilities
- Powerful AI technology
- Patent DNA Extraction
Browse by: Latest US Patents, China's latest patents, Technical Efficacy Thesaurus, Application Domain, Technology Topic, Popular Technical Reports.
© 2024 PatSnap. All rights reserved.Legal|Privacy policy|Modern Slavery Act Transparency Statement|Sitemap|About US| Contact US: help@patsnap.com