High-strength and high-conductivity rare-earth copper alloy and preparation method thereof
A rare-earth copper and high-conductivity technology, applied in the field of alloy materials, can solve the problems of only 65-70% conductivity, low strength, 6% and 75% elongation and conductivity, and achieve good comprehensive performance. Effect
- Summary
- Abstract
- Description
- Claims
- Application Information
AI Technical Summary
Problems solved by technology
Method used
Examples
Embodiment 1
[0033] The copper alloy of this example is composed of the following components in weight percentage: 0.3% chromium, 0.2% zirconium, 0.15% silver, 0.03% phosphorus, 0.02% cerium, and the balance is copper and unavoidable impurity elements. The specific preparation method is:
[0034] (1) Melting electrolytic copper, chromium, zirconium, silver, phosphorus, and rare earth elements at 1200 ° C, pouring into the mold after melting to form an ingot;
[0035] (2) Heating the cast ingot in step (1) to 850°C, keeping it warm for 1 hour, and then forging to form a bar with a deformation of 70% to obtain a bar;
[0036] (3) Put the billet in step (2) into a heat treatment furnace, keep it warm at 850°C for 1 hour, and then perform water quenching;
[0037] (4) cold-rolling and deforming the quenched alloy in step (3), the deformation amount is 60%;
[0038] (5) Heat the alloy after cold rolling and deformation in step (4) for the first time at an aging temperature of 400°C for 4 hour...
Embodiment 2
[0041] The copper alloy of this example is composed of the following components in weight percentage: 0.5% chromium, 0.3% zirconium, 0.2% silver, 0.03% phosphorus, 0.04% iridium, and the balance is copper and unavoidable impurity elements. The specific preparation method is:
[0042] (1) Melting electrolytic copper, chromium, zirconium, silver, phosphorus, and rare earth elements at 1250 ° C, pouring into the mold after melting to form an ingot;
[0043] (2) Heating the cast ingot in step (1) to 870°C, keeping it warm for 2 hours, and then forging to form a bar with a forging deformation of 70% to obtain a bar;
[0044] (3) Put the billet in step (2) into a heat treatment furnace, keep it at 900°C for 1 hour, and then perform water quenching;
[0045] (4) cold-rolling and deforming the quenched alloy in step (3), the deformation amount is 80%;
[0046] (5) Heat the alloy after cold rolling and deformation in step (4) for the first time at an aging temperature of 480°C for 2 ...
Embodiment 3
[0049] The copper alloy of this example is composed of the following components in weight percentage: 0.5% chromium, 0.3% zirconium, 0.2% silver, 0.03% phosphorus, 0.06% neodymium, and the balance is copper and unavoidable impurity elements. The specific preparation method is:
[0050](1) Melting electrolytic copper, chromium, zirconium, silver, phosphorus, and rare earth elements at 1250 ° C, pouring into the mold after melting to form an ingot;
[0051] (2) Heating the cast ingot in step (1) to 880°C, keeping it warm for 2 hours, and then forging to form a bar with a forging deformation of 75% to obtain a bar;
[0052] (3) Put the billet in step (2) into a heat treatment furnace, keep it at 910°C for 1.5 hours, and then perform water quenching;
[0053] (4) cold-rolling and deforming the quenched alloy in step (3), the deformation amount is 80%;
[0054] (5) Heat the cold-rolled and deformed alloy in step (4) for the first time at an aging temperature of 480°C for 4 hours,...
PUM
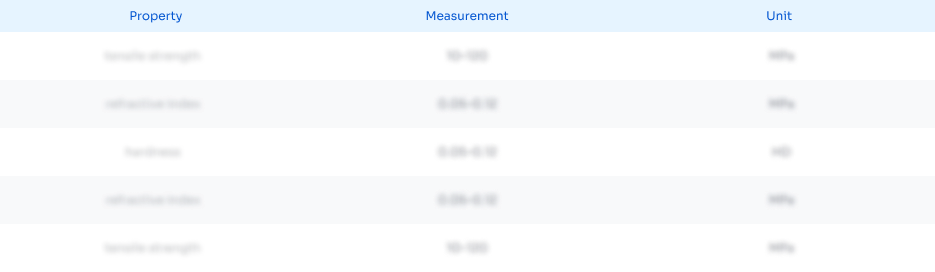
Abstract
Description
Claims
Application Information

- R&D
- Intellectual Property
- Life Sciences
- Materials
- Tech Scout
- Unparalleled Data Quality
- Higher Quality Content
- 60% Fewer Hallucinations
Browse by: Latest US Patents, China's latest patents, Technical Efficacy Thesaurus, Application Domain, Technology Topic, Popular Technical Reports.
© 2025 PatSnap. All rights reserved.Legal|Privacy policy|Modern Slavery Act Transparency Statement|Sitemap|About US| Contact US: help@patsnap.com