Optical fiber filling paste for polypropylene tube optical cable and preparation method thereof
A technology of optical fiber filling paste and polypropylene, which is applied in the direction of fiber mechanical structure, etc., can solve the problems of poor compatibility and small production quantity, and achieve the effects of good high-temperature dripping, ensuring performance transmission, and strong water resistance
- Summary
- Abstract
- Description
- Claims
- Application Information
AI Technical Summary
Problems solved by technology
Method used
Examples
Embodiment 1
[0037] Add 90 grams of tackifier to 483 grams of PAO 9 synthetic oil, stir well and evenly, add 55 grams of viscosity index improver, heat and stir for 1 to 3 hours, when the temperature rises to 150°C, keep warm and stir, until the viscosity After the index improver is completely melted in the synthetic oil, add 260 grams of high-viscosity synthetic oil and 85 grams of organic thickener respectively, and continue heating and stirring. After the softening agent is completely melted in the mixed oil, add 7 grams of antioxidant and stir for 0.5-1 hour, then cool down to 30 ° C ~ 60 ° C, add 20 grams of thickener, fully return and stir for 1 ~ 3 hours , after homogeneous grinding and vacuum degassing, the final product is a colorless transparent colloid.
[0038] Among the above raw materials, the synthetic oil is a commercially available product, the tackifier is selected from polyisobutylene products with a molecular weight between 2000 and 3000, the viscosity index improver is...
Embodiment 2
[0041] Add 91.5 grams of tackifier to 480 grams of PAO 9 synthetic oil, stir well and evenly, add 50 grams of viscosity index improver, heat and stir for 1 to 3 hours, when the temperature rises to 150°C, keep warm and stir until the viscosity After the index improver is completely melted in the synthetic oil, add 260 grams of high-viscosity synthetic oil and 90 grams of organic thickener respectively, and continue heating and stirring. After the softening agent is completely melted in the mixed oil, add 6.5 grams of antioxidant and stir for 0.5-1 hour, then cool down to 30°C-60°C, add 22 grams of thickener, fully return and stir for 1-3 hours , after homogeneous grinding and vacuum degassing, the final product is a colorless transparent colloid.
[0042] Among the above raw materials, synthetic oil is a commercially available product, the tackifier is selected from polybutene products with a molecular weight between 2000 and 3000, the viscosity index improver is selected from...
Embodiment 3
[0045] Add 90 grams of tackifier to 500 grams of PAO 12 synthetic oil, stir well and evenly, add 55 grams of viscosity index improver, heat and stir for 1 to 3 hours, when the temperature rises to 150°C, keep warm and stir until the viscosity After the index improver is completely melted in the synthetic oil, add 243 grams of high-viscosity synthetic oil and 85 grams of organic thickener respectively, and continue heating and stirring. After the softening agent is completely melted in the mixed oil, add 7 grams of antioxidant and stir for 0.5-1 hour, then cool down to 30 ° C ~ 60 ° C, add 20 grams of thickener, fully return and stir for 1 ~ 3 hours , after homogeneous grinding and vacuum degassing, the final product is a colorless transparent colloid.
[0046] Among the above raw materials, the synthetic oil is a commercially available product, the tackifier is selected from polyisobutylene products with a molecular weight between 2000 and 3000, the viscosity index improver is...
PUM
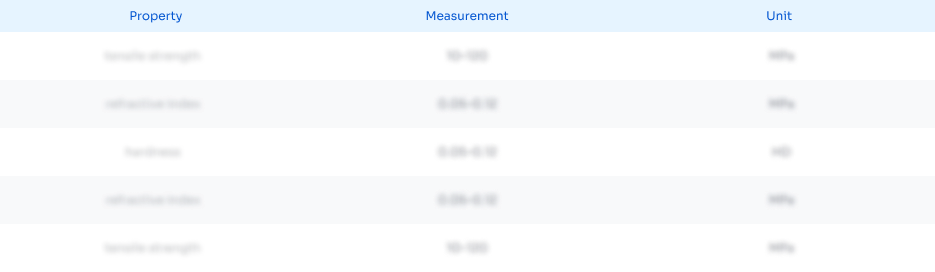
Abstract
Description
Claims
Application Information

- R&D
- Intellectual Property
- Life Sciences
- Materials
- Tech Scout
- Unparalleled Data Quality
- Higher Quality Content
- 60% Fewer Hallucinations
Browse by: Latest US Patents, China's latest patents, Technical Efficacy Thesaurus, Application Domain, Technology Topic, Popular Technical Reports.
© 2025 PatSnap. All rights reserved.Legal|Privacy policy|Modern Slavery Act Transparency Statement|Sitemap|About US| Contact US: help@patsnap.com