A kind of copper-zinc solder and preparation method thereof
A solder, copper-zinc technology, applied in the field of copper-zinc solder and its preparation, can solve the problems of copper tube rupture, stress concentration, leakage of refrigerant liquid, etc., and achieve the effects of cost reduction, easy operation and simple process
- Summary
- Abstract
- Description
- Claims
- Application Information
AI Technical Summary
Problems solved by technology
Method used
Examples
Embodiment 1
[0023] A copper-zinc solder in this embodiment is prepared from the following raw materials in weight percentage: Cu 58%; Sn 2%; Si 0.1%; Zn 39.9%.
[0024] The production process of the copper-zinc brazing filler metal comprises the following steps: First, firstly add a zinc ingot containing 9.15% by weight of zinc to the bottom of the crucible, and then add 0.1% by weight of copper and Silicon weight percentage is 0.1% copper-silicon alloy, then add copper-containing copper-silicon weight percentage on the copper-silicon alloy and be 57.9% electrolytic copper, then add the remaining zinc ingot that contains zinc weight percentage to be 30.75% on the electrolytic copper; Then the above raw materials After adding the crucible, heat the crucible for the first time; when the crucible is heated to 1100 ° C, all the raw materials in the crucible are melted and then stop heating; then add tin ingots with a tin weight percentage of 2% in the crucible, and heat the crucible for the se...
Embodiment 2
[0027] A copper-zinc solder in this embodiment is prepared from the following raw materials in weight percentage: Cu 60.72%; Sn 1.46%; Si 0.173%; Zn 37.647%.
[0028] The production process of the copper-zinc brazing filler metal comprises the following steps: First, firstly add a zinc ingot containing 8.5% by weight of zinc to the bottom of the crucible, and then add 0.173% by weight of copper and Silicon weight percentage is 0.173% copper-silicon alloy, then add electrolytic copper containing 60.547% copper weight percentage on the copper-silicon alloy, then add the remaining zinc ingots that contain zinc weight percentage to be 29.147% on the electrolytic copper; then the above raw materials After adding the crucible, heat the crucible for the first time; when the crucible is heated to 1100 °C, all the raw materials in the crucible are melted and then stop heating; After heating to 1100 degrees, all raw materials in the crucible are melted and then stop heating; finally sti...
Embodiment 3
[0031] A copper-zinc solder in this embodiment is prepared from the following raw materials in weight percentage: Cu 58.4%; Sn 2%; Si 0.5%; Zn 39.1%.
[0032] The production process of the copper-zinc brazing filler metal comprises the following steps: First, firstly add a zinc ingot containing 9.1% by weight of zinc to the bottom of the crucible, and then add 0.5% by weight of copper and Silicon weight percent is 0.5% copper-silicon alloy, and then on the copper-silicon alloy, adding electrolytic copper containing 57.9% copper by weight, then adding the remaining zinc ingot containing 30% zinc by weight on the electrolytic copper; then the above raw materials After adding the crucible, heat the crucible for the first time; when the crucible is heated to 1100 ° C, all the raw materials in the crucible are melted and then stop heating; then add tin ingots with a tin weight percentage of 2% in the crucible, and heat the crucible for the second time. After heating to 1100 degrees...
PUM
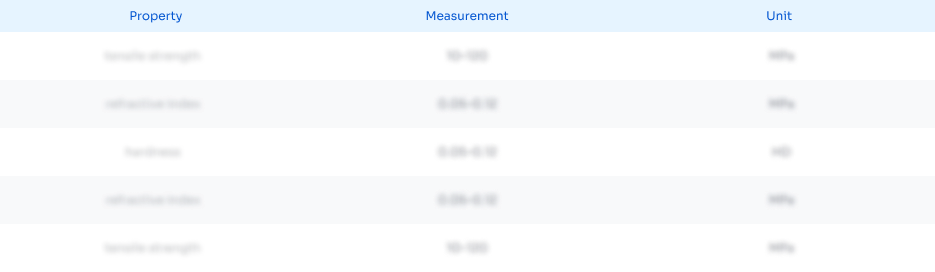
Abstract
Description
Claims
Application Information

- R&D
- Intellectual Property
- Life Sciences
- Materials
- Tech Scout
- Unparalleled Data Quality
- Higher Quality Content
- 60% Fewer Hallucinations
Browse by: Latest US Patents, China's latest patents, Technical Efficacy Thesaurus, Application Domain, Technology Topic, Popular Technical Reports.
© 2025 PatSnap. All rights reserved.Legal|Privacy policy|Modern Slavery Act Transparency Statement|Sitemap|About US| Contact US: help@patsnap.com