Blast furnace slag granulation and waste heat recovery device
A waste heat recovery device and blast furnace slag technology, which is applied in the field of ironmaking, can solve the problems of waste of high-quality waste heat resources, unrecoverable heat, and pollution of the surrounding environment, and achieve the effects of saving consumption, fully and effectively recycling, and reducing pollution
- Summary
- Abstract
- Description
- Claims
- Application Information
AI Technical Summary
Problems solved by technology
Method used
Image
Examples
Embodiment Construction
[0009] The present invention will be further described in detail below in conjunction with the accompanying drawings.
[0010] As shown in the figure, the present invention is mainly composed of a slag chute (1), a liquid slag bucket (2), a quick cooling cavity (3), a star-shaped slag discharge wheel (9), and an air-cooled cavity (10). The slag chute (1) is located at the top of the device, and its inlet is slightly higher and connected to the slag ditch of the blast furnace tapping site, and the outlet is slightly lower than the liquid slag hopper (2); the lower part of the liquid slag hopper (2) is connected to the quick cooling cavity (3) ), the slag chute (1) and the liquid slag bucket (2) are made of refractory materials; the lower part of the quick cooling chamber (3) is equipped with a star-shaped slag wheel (9) and connected to the air-cooled chamber (10) at the bottom ). It is characterized in that the quick cooling chamber (3) is composed of an upper part of the granul...
PUM
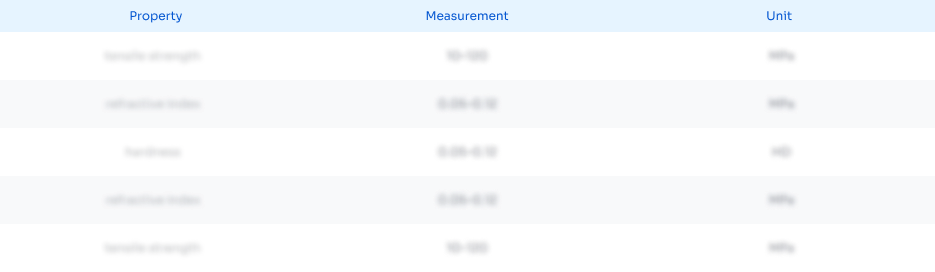
Abstract
Description
Claims
Application Information

- R&D Engineer
- R&D Manager
- IP Professional
- Industry Leading Data Capabilities
- Powerful AI technology
- Patent DNA Extraction
Browse by: Latest US Patents, China's latest patents, Technical Efficacy Thesaurus, Application Domain, Technology Topic, Popular Technical Reports.
© 2024 PatSnap. All rights reserved.Legal|Privacy policy|Modern Slavery Act Transparency Statement|Sitemap|About US| Contact US: help@patsnap.com