Epoxy resin modified styrene-acrylic emulsion and preparation method thereof
A technology of epoxy resin and styrene-acrylic emulsion, applied in coating, paper coating, textile and papermaking, etc., can solve the problems of poor surface strength of paper and poor water resistance of emulsion, so as to improve strength, good adhesion, and improve surface Effects of strength and gloss
- Summary
- Abstract
- Description
- Claims
- Application Information
AI Technical Summary
Problems solved by technology
Method used
Image
Examples
Embodiment 1
[0027] 20g of n-butyl acrylate, 74g of styrene, 6g of acrylic acid, 8g of epoxy resin (E-42) were fully mixed and dissolved at room temperature, and 2g of 2-hydroxyethyl methacrylate and 0.25g of dodecane were added Sodium phenyl sulfonate, 0.1g polyoxyethylene (20) sorbitan monooleate (Tween 80), 60g deionized water in a mixed aqueous solution, and then on the JB90-D type strong electric stirring machine, to Stir at a rotating speed of 1000rpm for 30 minutes to obtain a monomer pre-emulsion;
[0028] In a four-necked bottle filled with 0.2g sodium bicarbonate, 0.25g sodium dodecylbenzenesulfonate, 0.1g polyoxyethylene (20) sorbitan monooleate (Tween 80), and 176g deionized water Add 15g of the above-mentioned pre-emulsion to the mixture, raise the temperature to 60°C, add an aqueous solution of 0.1g potassium persulfate dissolved in 10g deionized water, react until the emulsion turns blue, and drop the remaining pre-emulsion and 0.3g potassium persulfate dissolved in 10g Aqu...
Embodiment 2
[0030] 40g of ethyl acrylate, 50g of methyl styrene, 10g of methacrylic acid, and 4g of epoxy resin (E-20) were fully mixed and dissolved at room temperature, and then 1g of 2-hydroxyethyl acrylate and 0.1g of dialkyl were added - Sodium 2-sulfosuccinate, 0.4g sorbitan monolaurate (Span 20), 1.5g polyoxyethylene monooleate, 60g deionized water, and then in JB90-D type Stir at a speed of 1500 rpm for 30 minutes on a powerful electric mixer to obtain a monomer pre-emulsion.
[0031] Add 15g of the above pre-emulsion to a four-necked bottle containing 2g disodium hydrogen phosphate, 1.5g sodium dodecylnaphthalenesulfonate, 1g sorbitan monolaurate (Span 20), and 26.7g deionized water , raise the temperature to 95°C, add 1g of sodium persulfate dissolved in 10g of deionized water, react until the emulsion turns blue, then add the remaining pre-emulsion and 3g of sodium persulfate in 10g of deionized water dropwise, drop for 1h After finishing, keep warm at 80°C for 1 hour, after c...
Embodiment 3
[0033] Add 1.5g of 10g of methyl methacrylate, 34g of 2-ethylhexyl acrylate, 48g of methyl styrene, 8g of methacrylic acid and 10g of epoxy resin (E-20) to the mixture that was fully mixed and dissolved at room temperature 2-hydroxypropyl methacrylate and 0.1g sodium succinate sulfonate, 0.2g polyoxypropylene stearate, 0.5g sodium lauryl sulfate, 0.2g sorbitan monooleate ( Span 80) and 60g of deionized water, and then stirred at a speed of 2000rpm for 20 minutes on a JB90-D powerful electric stirring machine to obtain a monomer pre-emulsion.
[0034] Add 15g of the above-mentioned pre-emulsion in a four-necked bottle equipped with 0.5g sodium bicarbonate, 0.2g potassium oleate, 0.8g diethylene glycol fatty acid ester, 0.3g sodium lauryl sulfate, and 94.9g deionized water, Raise the temperature to 75°C, add 0.8g of potassium persulfate dissolved in 10g of deionized water, react until the emulsion turns blue, and add the remaining pre-emulsion and 1.5g of potassium persulfate in...
PUM
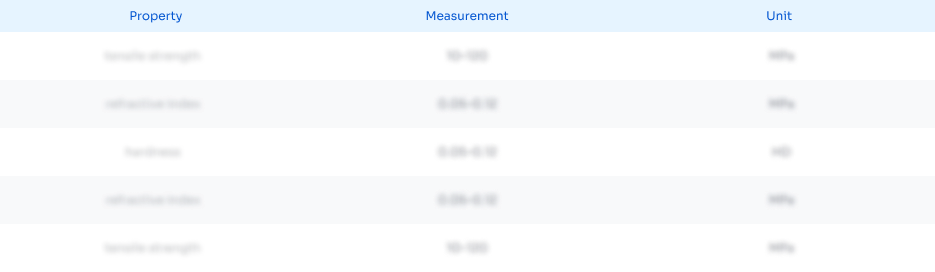
Abstract
Description
Claims
Application Information

- R&D
- Intellectual Property
- Life Sciences
- Materials
- Tech Scout
- Unparalleled Data Quality
- Higher Quality Content
- 60% Fewer Hallucinations
Browse by: Latest US Patents, China's latest patents, Technical Efficacy Thesaurus, Application Domain, Technology Topic, Popular Technical Reports.
© 2025 PatSnap. All rights reserved.Legal|Privacy policy|Modern Slavery Act Transparency Statement|Sitemap|About US| Contact US: help@patsnap.com