Hot loading method for medium-thick slabs
A thick slab, hot charging technology, applied in heat treatment furnaces, heat treatment equipment, furnace types, etc., can solve the problems of slab fracture, thermal stress difference, uneven heating in the heating furnace, etc., to reduce the probability of scrap and thermal conductivity. Good, no-investment results
- Summary
- Abstract
- Description
- Claims
- Application Information
AI Technical Summary
Problems solved by technology
Method used
Image
Examples
Embodiment 1
[0032] The 250mm×2200mm×7200mm high-quality carbon structural steel medium-thick plate high-temperature billet produced by continuous casting in a steel plant is transported to the rolling mill through the conveying roller table, and the billet is hoisted to the slow cooling site of the wide-plate factory for stacking. The surface temperature of the slab is 750-850°C. The normal-temperature slabs are medium-thick slabs of the same steel type and size. The normal-temperature slabs and the high-temperature slabs are stacked alternately by sandwiching a cold slab between two hot slabs. There are 4 stacks in total. 7 high-temperature slabs and 3 normal-temperature slabs are stacked in each pile. When the slabs are stacked for 12 hours, the side temperature of the high-temperature slab after slow cooling is 580-630°C, and that of the normal-temperature slab after preheating is 450~500°C; After the billets are stacked for 14 hours, they are loaded into the heating furnace. First, t...
Embodiment 2
[0034] The 250mm×2200mm×7200mm high-quality carbon structural steel medium-thick plate high-temperature billet produced by continuous casting in a steel plant is transported to the wide-plate rolling mill through the conveying roller table, and the cast billet is hoisted to the slow-cooling site of the wide-plate factory for stacking and stacking The surface temperature of the slab is 800-850℃, and the slab at room temperature is 250mm×2200mm×3400mm low-alloy structural steel medium-thick slab. pile up. There are 2 piles in total, each with 7 pieces of high-temperature billets and 6 pieces of normal-temperature billets. When the billets are stacked for 12 hours, the side temperature of the high-temperature billets is 530-610°C after slow cooling, and the billets at room temperature are preheated. The temperature of the rear side is 430-530°C; after the slabs are stacked for 14 hours, they are loaded into the heating furnace. Slowly cooled slabs; the slab conveying roller tabl...
PUM
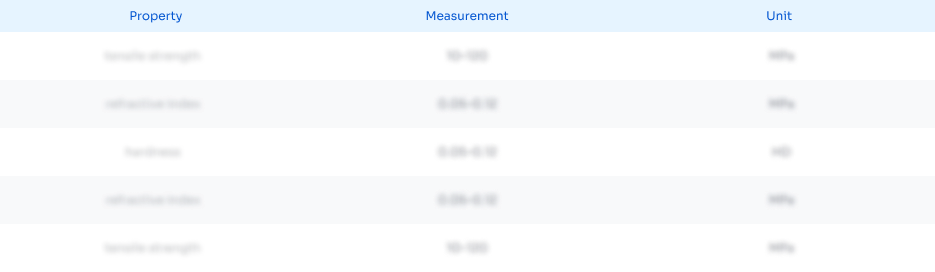
Abstract
Description
Claims
Application Information

- Generate Ideas
- Intellectual Property
- Life Sciences
- Materials
- Tech Scout
- Unparalleled Data Quality
- Higher Quality Content
- 60% Fewer Hallucinations
Browse by: Latest US Patents, China's latest patents, Technical Efficacy Thesaurus, Application Domain, Technology Topic, Popular Technical Reports.
© 2025 PatSnap. All rights reserved.Legal|Privacy policy|Modern Slavery Act Transparency Statement|Sitemap|About US| Contact US: help@patsnap.com