Epoxy resin composition, and prepreg and copper foil-clad laminated sheet prepared by using epoxy resin composition
A technology of epoxy resin and prepreg, which is applied in the direction of synthetic resin layered products, layered products, metal layered products, etc., and can solve the problems of low glass transition temperature, low dielectric loss tangent, reduced water absorption, and low water absorption. , to achieve excellent dielectric properties, low water absorption, good heat and humidity resistance
- Summary
- Abstract
- Description
- Claims
- Application Information
AI Technical Summary
Problems solved by technology
Method used
Image
Examples
Embodiment 1
[0088] Take a container, add 100 parts by weight of naphthol type novolac epoxy resin NC-7300L (Nippon Kayaku Corporation, EEW is 214g / eq), and then add 105 parts by weight of active ester curing agent HPC-8000-65T (Japan DIC , solid content 65%) and stir evenly, then add 30 parts by weight of flame retardant aluminum phosphate (Clariant company, phosphorus content is 23%), then add 0.075 parts by weight of curing accelerator DMAP, and solvent toluene, continue to stir evenly Serve as glue. Use glass fiber cloth (type 2116, thickness 0.08mm) to impregnate the above glue solution, and control it to an appropriate thickness, then dry to remove the solvent to prepare a prepreg. Use several prepared prepregs to stack each other, press a piece of copper foil on each side of it, and cure it in a hot press to obtain a copper-clad laminate. The curing temperature is 150-250 ° C, and the curing pressure is 25-60Kg / cm 2 , The curing time is 90min.
Embodiment 2
[0090] Take a container, add 100 parts by weight of naphthol type novolac epoxy resin NC-7000L (Nippon Kayaku Corporation, EEW is 232g / eq), and then add 95 parts by weight of active ester curing agent HPC-8000-65T (Japan DIC , solid content 65%) and stir evenly, then add 30 parts by weight of flame retardant aluminum phosphate (Clariant company, phosphorus content is 23%), then add 0.075 parts by weight of curing accelerator DMAP, and solvent toluene, continue to stir evenly Serve as glue. Use glass fiber cloth (type 2116, thickness 0.08mm) to impregnate the above glue solution, and control it to an appropriate thickness, then dry to remove the solvent to prepare a prepreg. Use several prepared prepregs to stack each other, press a piece of copper foil on each side of it, and cure it in a hot press to obtain a copper-clad laminate. The curing temperature is 150-250 ° C, and the curing pressure is 25-60Kg / cm 2 , The curing time is 90min.
Embodiment 3
[0092]Take a container, add 100 parts by weight of naphthol type novolak epoxy resin HP-5000 (Japan DIC company, EEW is 250g / eq), and then add 90 parts by weight of active ester curing agent HPC-8000-65T (Japan DIC company, solid content 65%) and stir evenly, then add 35 parts by weight of flame retardant phosphate aluminum salt (Clariant company, phosphorus content is 23%), then add 0.075 parts by weight of curing accelerator DMAP, and solvent toluene, continue to stir evenly into glue. Use glass fiber cloth (type 2116, thickness 0.08mm) to impregnate the above glue solution, and control it to an appropriate thickness, then dry to remove the solvent to prepare a prepreg. Use several prepared prepregs to stack each other, press a piece of copper foil on each side of it, and cure it in a hot press to obtain a copper-clad laminate. The curing temperature is 150-250 ° C, and the curing pressure is 25-60Kg / cm 2 , The curing time is 90min.
PUM
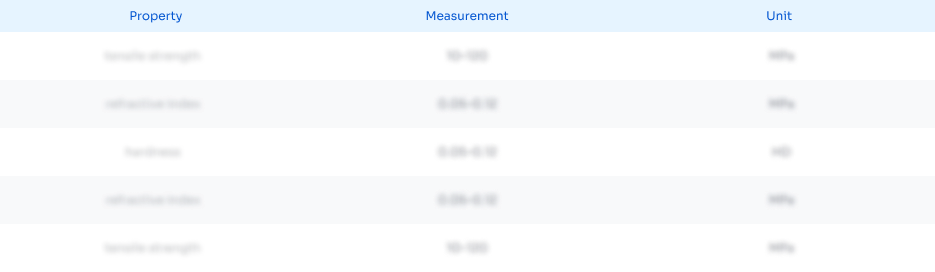
Abstract
Description
Claims
Application Information

- R&D Engineer
- R&D Manager
- IP Professional
- Industry Leading Data Capabilities
- Powerful AI technology
- Patent DNA Extraction
Browse by: Latest US Patents, China's latest patents, Technical Efficacy Thesaurus, Application Domain, Technology Topic, Popular Technical Reports.
© 2024 PatSnap. All rights reserved.Legal|Privacy policy|Modern Slavery Act Transparency Statement|Sitemap|About US| Contact US: help@patsnap.com