Method for directly smelting high-titanium molten iron by using converter
A converter and molten iron technology, which is applied in the manufacture of converters and the improvement of process efficiency, can solve the problems of no direct smelting of high-titanium molten iron, and achieve the effects of improving resource recycling, improving stability, and improving effects
- Summary
- Abstract
- Description
- Claims
- Application Information
AI Technical Summary
Problems solved by technology
Method used
Examples
Embodiment
[0013] The 100-ton top-bottom double-blown converter directly smelting high-titanium molten iron using the method of the present invention has the following characteristics:
[0014] ① Add magnetic separation slag and sludge balls in the early stage of blowing to promote faster slagging of vanadium-titanium molten iron; the amount of magnetic separation slag and sludge balls must reach about 70kg / t steel to ensure that the slag after melting The content of FeO in the medium meets the requirements of slag removal.
[0015] ② The method of blowing with low lance position and high flow rate is adopted, the parameters of low lance position are determined according to the capacity of the converter, and the oxygen flow rate is controlled at 350 m 3 / min, weaken the temperature echelon and concentration gradient of the converter molten pool, so that the pig iron, magnetic separation slag, and sludge balls in the early stage can be melted rapidly; the slag alkalinity in the blowing pr...
PUM
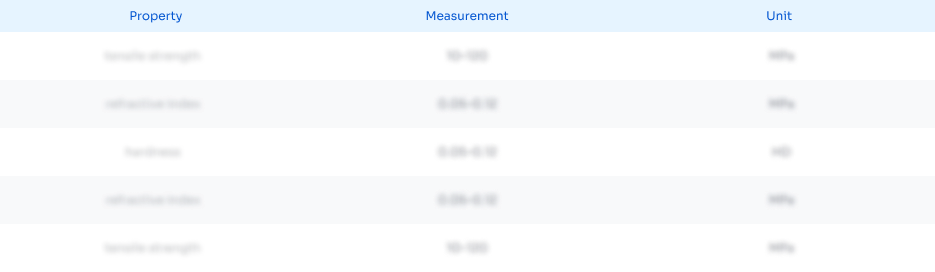
Abstract
Description
Claims
Application Information

- R&D Engineer
- R&D Manager
- IP Professional
- Industry Leading Data Capabilities
- Powerful AI technology
- Patent DNA Extraction
Browse by: Latest US Patents, China's latest patents, Technical Efficacy Thesaurus, Application Domain, Technology Topic, Popular Technical Reports.
© 2024 PatSnap. All rights reserved.Legal|Privacy policy|Modern Slavery Act Transparency Statement|Sitemap|About US| Contact US: help@patsnap.com