Hf (Ta) C ultra-high-temperature composite coating and preparation method thereof
An ultra-high temperature coating technology, applied in the field of HfC ultra-high temperature multi-phase coating and its preparation, can solve the problems that are difficult to meet the ablation environment of solid rocket engine throat lining, and achieve excellent ablation resistance and thermal shock resistance Superior performance and anti-ablation performance, combined with good effect
- Summary
- Abstract
- Description
- Claims
- Application Information
AI Technical Summary
Problems solved by technology
Method used
Image
Examples
Embodiment 1
[0037] First, the C / C composite material was polished and polished with SiC sandpaper, cleaned with ultrasonic alcohol for 30 minutes, and dried in vacuum at 120°C for 2 hours before use; the hafnium tetrachloride and tantalum pentachloride powders were placed in a vacuum glove box, and placed under argon protection. The two powders are mechanically mixed at a molar ratio of 4 / 1; the obtained multi-component precursor mixed powder is placed in a mechanical powder feeding device, and the surface-treated carbon / carbon composite material substrate is placed in a low-pressure chemical vapor deposition furnace.
[0038] Turn on the vacuum system to keep the vapor deposition furnace at low pressure (lower than 100Pa); turn on the argon protection, turn on the heating system, and heat up to 1300°C at a heating rate of 5°C / min; after the temperature rises to 1300°C, put in hydrogen . After the temperature in the furnace is stabilized, methane is introduced, and the CH 4 / H 2 =1 / 8、CH...
Embodiment 2
[0042] Firstly, the graphite was polished and polished with SiC sandpaper, cleaned with ultrasonic alcohol for 30 min, and vacuum-dried at 120°C for 2 h for later use; the powders of hafnium tetrachloride and tantalum pentachloride were placed in a vacuum glove box, and the two powders were separated under the protection of argon. The molar ratio is 1 / 1 mechanical mixing; the obtained multi-component precursor mixed powder is placed in a mechanical powder feeding device, and the surface-treated carbon / carbon composite material substrate is placed in a low-pressure chemical vapor deposition furnace.
[0043] Turn on the vacuum system to keep the vapor deposition furnace at low pressure (lower than 100Pa); turn on the argon gas protection, turn on the heating system, and heat up to 1650°C at a heating rate of 8°C / min; after the temperature rises to 1650°C, put in hydrogen . After the temperature in the furnace is stabilized, methane is introduced, and the CH 4 / H 2 =1 / 20,CH 4...
Embodiment 3
[0047] Firstly, the ZrC ceramics were polished and polished with SiC sandpaper, cleaned with ultrasonic alcohol for 30 minutes, and then vacuum-dried at 120°C for 2 hours for later use. Physical mixing at a molar ratio of 10 / 1; the obtained multi-component precursor mixed powder is placed in a mechanical powder feeding device, and the surface-treated carbon / carbon composite material substrate is placed in a low-pressure chemical vapor deposition furnace.
[0048] Turn on the vacuum system to keep the vapor deposition furnace at low pressure (lower than 100Pa); turn on the argon gas protection, turn on the heating system, and heat up to 1400°C at a heating rate of 10°C / min; after the temperature rises to 1400°C, put in hydrogen . After the temperature in the furnace is stabilized, methane is introduced, and the CH 4 / H 2 =1 / 1,CH 4 / (HfCl 4 +TaCl 5 ) = 5 / 1, and at the same time turn on the mechanical powder feeding device, control the internal pressure of the reaction furna...
PUM
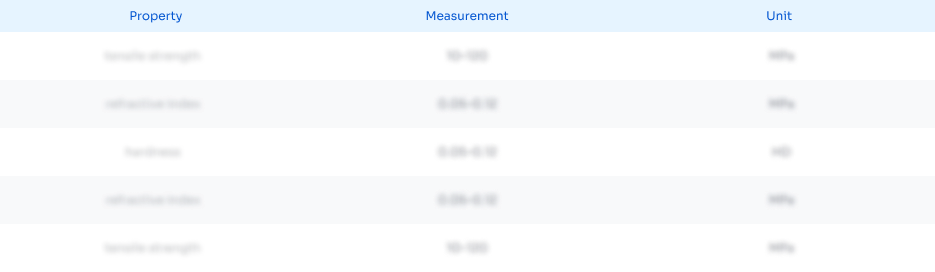
Abstract
Description
Claims
Application Information

- R&D
- Intellectual Property
- Life Sciences
- Materials
- Tech Scout
- Unparalleled Data Quality
- Higher Quality Content
- 60% Fewer Hallucinations
Browse by: Latest US Patents, China's latest patents, Technical Efficacy Thesaurus, Application Domain, Technology Topic, Popular Technical Reports.
© 2025 PatSnap. All rights reserved.Legal|Privacy policy|Modern Slavery Act Transparency Statement|Sitemap|About US| Contact US: help@patsnap.com