Compound molding tool system for hot stretch bending and creep deformation of section bar and application method of compound molding tool system
A composite forming and heating system technology, applied in the field of metal thermal processing, can solve problems such as many processes, poor forming precision, and difficulty in achieving precise forming, and achieve the effects of reducing manufacturing costs, improving forming precision and quality, and reducing springback
- Summary
- Abstract
- Description
- Claims
- Application Information
AI Technical Summary
Problems solved by technology
Method used
Image
Examples
Embodiment Construction
[0043] 1) A thermal stretch bending and creep composite forming tooling system for profiles according to the present invention includes a stretch arm type profile stretch bending machine 7, a heating box 1, a self-resistance heating system, an electrical control cabinet 8 and clamps 2, such as figure 1 shown. The position connection relationship between them is: the heating box 1 is located on the working table in the middle of the stretch arm type profile bending machine 7, and the electrical control cabinet 8 is located in front of the stretch arm type profile stretch bending machine 7 and connected with the stretch arm type profile stretch bending machine 7 connections, the self-resistance heating system is located on the periphery of the system, and the clamp 2 is installed on the stretching arm of the stretching arm type profile stretch bending machine 7.
[0044] The stretch arm type profile stretch bending machine 7 is a common profile stretch bending forming equipment,...
PUM
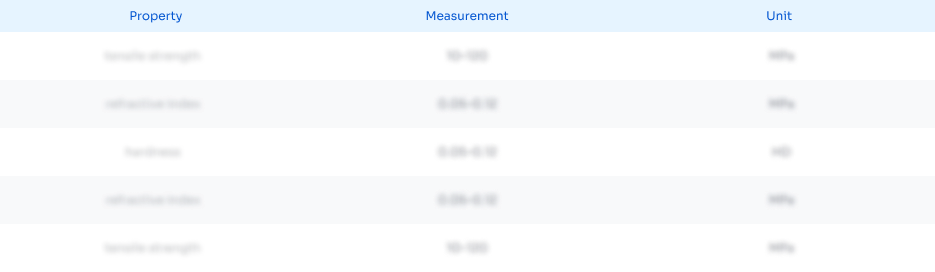
Abstract
Description
Claims
Application Information

- R&D Engineer
- R&D Manager
- IP Professional
- Industry Leading Data Capabilities
- Powerful AI technology
- Patent DNA Extraction
Browse by: Latest US Patents, China's latest patents, Technical Efficacy Thesaurus, Application Domain, Technology Topic, Popular Technical Reports.
© 2024 PatSnap. All rights reserved.Legal|Privacy policy|Modern Slavery Act Transparency Statement|Sitemap|About US| Contact US: help@patsnap.com