Method for argon-oxygen refining low-phosphorus ferrochrome
A ferrochrome alloy, argon-oxygen refining technology, applied in the field of argon-oxygen refined ferrochrome alloy dephosphorization and carbon reduction and chromium preservation, can solve the problems of carbon reduction efficiency reduction, chromium loss, difficulty in carbon reduction and chromium preservation, and achieve high-efficiency dephosphorization Effect
- Summary
- Abstract
- Description
- Claims
- Application Information
AI Technical Summary
Problems solved by technology
Method used
Image
Examples
Embodiment 1
[0024] The consistent conditions used in the experiments of multiple examples are: 1) The argon-oxygen refining furnace is a 5-ton top-bottom double-blown converter; 2) Each furnace of ferrochrome melt is 4 tons; 3) The dephosphorization agent uses commonly used CaO-BaO slag System, composition: 25% calcium oxide-50% barium oxide-15% calcium fluoride-10% iron oxide; 4) high carbon ferrochrome alloy (raw material) carbon content: 7.4~7.6%wt; 5) high carbon ferrochrome alloy ( Raw material) Phosphorus content: 0.05-0.06%wt; 6) Refining temperature is 1780-1820°C.
[0025] Obtained ferrochrome alloy melt dephosphorization experimental data by argon-oxygen refining a plurality of embodiments is as shown in table 1, can see, in the dephosphorization carbon content of the present invention 3.0~5.5%wt, dephosphorization time 10~30 minutes , The elevation distance of the top gun position is 10-50 cm, the top-blowing flow rate is 3.0-4.0 cubic meters per ton of melt per minute, the top...
Embodiment 2
[0028] 1) Initial high-temperature carbon reduction: the high-carbon ferrochrome alloy melt mixed into the argon-oxygen refining converter with top-bottom re-blowing is quickly raised to a high temperature of 1750°C for carbon reduction and refining until the carbon content drops to 5.0%wt , quickly reduce carbon to the carbon content required for dephosphorization at a higher temperature, and the loss of chromium is minimal;
[0029] 2) Melt cooling and slag replacement: reduce the carbon content to 5.0%wt of the ferrochromium alloy melt by re-blowing argon to cool it down, and remove 50% of the original slag during the cooling process, and then put 50 kg / ton of melt The barium oxide-calcium oxide slag-based dephosphorization agent until the temperature drops to 1400°C;
[0030] Rapidly lower the melt to a temperature suitable for dephosphorization, remove part of the high-silicon slag that is not conducive to dephosphorization, and use the high-temperature melt to quickly me...
Embodiment 3
[0035] 1) Initial high-temperature carbon reduction: the high-carbon ferrochrome alloy melt mixed into the argon-oxygen refining AOD furnace with top-bottom re-blowing is quickly raised to a high temperature of 1750°C for carbon reduction and refining until the carbon content drops to 5.0% wt, rapid decarburization to a carbon content suitable for dephosphorization at higher temperatures with minimal loss of chromium;
[0036] 2) Melt cooling and slag replacement: the ferrochromium alloy melt with carbon content reduced to 5.5%wt is cooled by blowing argon again, and at the same time, 50-100% of the original slag is removed during the cooling process, and then 90 kg / ton is added Dephosphorization agent of barium oxide-calcium oxide slag system in the melt until the temperature is lowered to 1550°C;
[0037] Rapidly lower the melt to a temperature suitable for dephosphorization, remove part of the high-silicon slag that is not conducive to dephosphorization, and use the high-te...
PUM
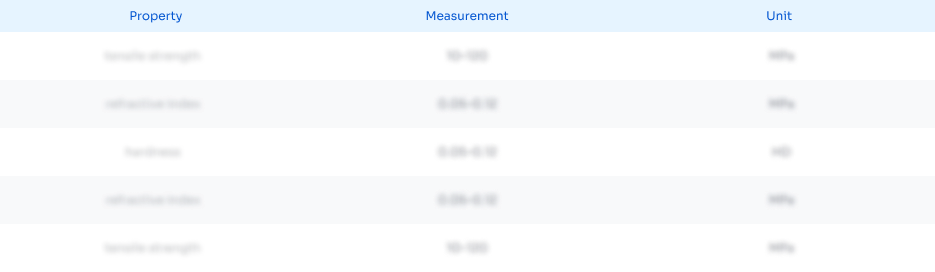
Abstract
Description
Claims
Application Information

- R&D
- Intellectual Property
- Life Sciences
- Materials
- Tech Scout
- Unparalleled Data Quality
- Higher Quality Content
- 60% Fewer Hallucinations
Browse by: Latest US Patents, China's latest patents, Technical Efficacy Thesaurus, Application Domain, Technology Topic, Popular Technical Reports.
© 2025 PatSnap. All rights reserved.Legal|Privacy policy|Modern Slavery Act Transparency Statement|Sitemap|About US| Contact US: help@patsnap.com