Method for producing roll collars by recycling tungsten carbide from waste hard alloy roll collars
A technology of cemented carbide and tungsten carbide, which is applied in the field of recycling coarse-grained tungsten carbide to produce roll rings, can solve problems such as product quality, unstable performance, high production costs and energy consumption, and zinc environmental hazards, so as to improve efficiency, The effect of reducing production cost and improving wear resistance
- Summary
- Abstract
- Description
- Claims
- Application Information
AI Technical Summary
Problems solved by technology
Method used
Examples
Embodiment 1
[0015] Example 1, a method of recycling tungsten carbide from discarded cemented carbide roll rings to produce roll rings is to use coarse-grained tungsten carbide recovered from discarded cemented carbide roll rings as raw material, and mix other raw materials according to the formula of the roll ring , put into rolling ball mill, add alcohol weight and be 13.8-15.7% of raw material weight, alcohol is the industrial alcohol with ethanol weight content greater than 95.5%, present embodiment raw material total amount is 300kg, in 300L rolling ball mill, add alcohol 41.4kg, Grinding for 22-24 hours, after conventional screening, drying, glue mixing, pressing, and degumming steps, pressurize 6MPa in a vacuum pressurized sintering furnace at a temperature of 1410°C-1460°C, and hold the pressure for not less than 70min. The furnace temperature is not higher than 100°C, and the roller ring is composed of 82%-90% WC, 7%-10% Co, 2.1%-7.1% Ni, 0.4% Cr, and 0.5% mixed powder, of which T...
Embodiment 2
[0016] Example 2, a method of recycling tungsten carbide from discarded cemented carbide roller rings to produce roller rings is to use coarse-grained tungsten carbide recovered from discarded cemented carbide roller rings as raw material, and mix other raw materials according to the formula of the roller ring 300kg, add 47.1kg of alcohol in a 300L rolling ball mill, grind for 22-24 hours, after sieving, drying, mixing, pressing, and degumming, pressurize in a vacuum pressurized sintering furnace at a temperature of 1410°C-1460°C 6MPa, the holding time is not less than 70min, and the furnace temperature is not higher than 100°C. The coarse-grained tungsten carbide raw material recovered from the discarded cemented carbide roll ring used in this example is obtained by the following method: the discarded carbide The high-quality alloy roller rings are classified according to different models and placed in an intermediate frequency carbonization furnace. 2 protection, flow 3mm 3...
PUM
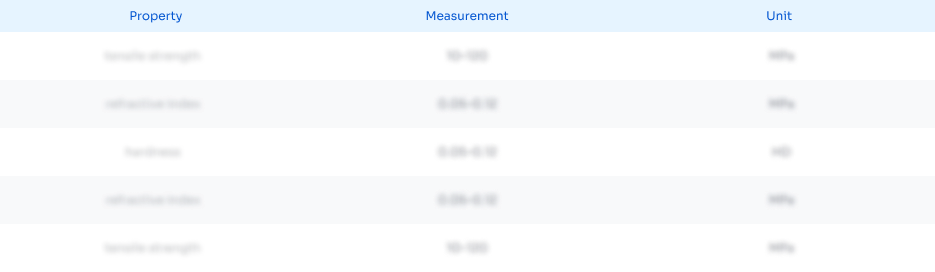
Abstract
Description
Claims
Application Information

- R&D Engineer
- R&D Manager
- IP Professional
- Industry Leading Data Capabilities
- Powerful AI technology
- Patent DNA Extraction
Browse by: Latest US Patents, China's latest patents, Technical Efficacy Thesaurus, Application Domain, Technology Topic, Popular Technical Reports.
© 2024 PatSnap. All rights reserved.Legal|Privacy policy|Modern Slavery Act Transparency Statement|Sitemap|About US| Contact US: help@patsnap.com