Dipped anti-oxidation fluid capable of improving high temperature anti-oxidation performance of graphite products and application method thereof
A technology for high-temperature anti-oxidation and graphite products, applied in chemical instruments and methods, compositions for inhibiting chemical changes, graphite, etc., can solve the problems of low impregnation efficiency, low oxidation resistance temperature, etc., and achieve the effect of convenient operation and simple process
- Summary
- Abstract
- Description
- Claims
- Application Information
AI Technical Summary
Problems solved by technology
Method used
Image
Examples
Embodiment 1
[0018] One weight component of the anti-oxidation dipping solution is selected: 50% of sodium hexametaphosphate and 50% of potassium aluminum sulfate. First dissolve the components and water at a ratio of 1:0.1 by weight, mix and stir the dissolved solution and heat it to about 100°C. 10h. The two components of the impregnation solution are: 30% sodium silicate, 70% sodium tetraborate, add water with a weight ratio of 1:3:3, stir and heat to about 100°C, and when the impregnation solution becomes clear, Put the graphite block into the impregnating solution and impregnate at normal pressure for 10h. Take out the impregnated graphite sample block and let it dry naturally or by heating. The treated graphite block is placed in a muffle furnace and heated to 1200°C at a heating rate of 10°C / min for 1 hour, and the oxidation weight loss is about 15%.
Embodiment 2
[0020] One weight component of the anti-oxidation dipping solution is selected: 50% of sodium hexametaphosphate and 50% of potassium aluminum sulfate. First dissolve the components and water at a ratio of 1:0.1 by weight, mix and stir the dissolved solution and heat it to about 100°C. 10h. The two components of the impregnation solution are: 40% sodium silicate, 60% sodium tetraborate, add water with a weight ratio of 1:3.3, stir and heat to about 100°C, and after the impregnation solution becomes clear, the graphite Put the block into the impregnating solution, and impregnate at normal pressure for 10h. Take out the impregnated graphite sample block and let it dry naturally or by heating. The treated graphite block was heated in a muffle furnace at a heating rate of 10°C / min to a constant temperature of 1200°C for 1 hour, and the oxidation weight loss was about 10%.
Embodiment 3
[0022] One weight component of the anti-oxidation dipping solution is selected: 50% of sodium hexametaphosphate and 50% of potassium aluminum sulfate. First dissolve the components and water at a ratio of 1:0.1 by weight, mix and stir the dissolved solution and heat it to about 100°C. 10h. The two components of the impregnation solution are: sodium tetraborate 50%, sodium hexametaphosphate 50%, add water with a weight ratio of 1:3.3, stir and heat to about 100°C, and when the impregnation solution becomes clear, put Put the graphite block into the impregnating solution and impregnate at normal pressure for 10h. Take out the impregnated graphite sample block and let it dry naturally or by heating.
[0023] Comparative test three:
[0024] Cut the graphite sample block into 1×1×1cm squares such as figure 1 As shown, without any treatment, put it in a muffle furnace and heat it to 1200°C at a heating rate of 10°C / min, and the condition when the temperature is constant for 1 h...
PUM
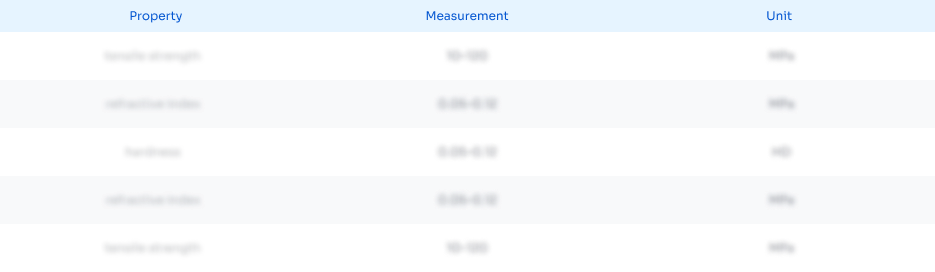
Abstract
Description
Claims
Application Information

- R&D Engineer
- R&D Manager
- IP Professional
- Industry Leading Data Capabilities
- Powerful AI technology
- Patent DNA Extraction
Browse by: Latest US Patents, China's latest patents, Technical Efficacy Thesaurus, Application Domain, Technology Topic, Popular Technical Reports.
© 2024 PatSnap. All rights reserved.Legal|Privacy policy|Modern Slavery Act Transparency Statement|Sitemap|About US| Contact US: help@patsnap.com