Preparation method of microporous-mesoporous composite zeolite
A composite molecular sieve and molecular sieve technology, which is applied in the direction of molecular sieve catalysts, chemical instruments and methods, physical/chemical process catalysts, etc., and can solve problems such as application range limitations
- Summary
- Abstract
- Description
- Claims
- Application Information
AI Technical Summary
Problems solved by technology
Method used
Image
Examples
Embodiment 1
[0029] Put 1038g of water glass (Hongxing Soda Soda Factory, modulus: 3.1-3.4) into a 3000ml two-necked flask. Weigh 266g of sodium hydroxide (Beijing Chemical Plant, analytically pure), dissolve it into 400ml of deionized water, then add the sodium hydroxide solution into the water glass and stir for 30 minutes. Get 198g of aluminum sulfate (Beijing Chemical Reagent Company, analytically pure) and dissolve it in 400ml of deionized water, add the aluminum sulfate solution dropwise to the mixture of water glass and sodium hydroxide, carry out aging at 98°C, and obtain a compound containing Y after 8 hours Type molecular sieve precursor; 200g P123 (Aldrich, analytical grade) was dissolved in 7500ml deionized water, stirred at 25°C, and the pH of the P123 solution was adjusted to 1.5 with sulfuric acid. After the aging of the precursor is completed, weigh 1500g of fresh Y molecular sieve precursor emulsion and add it to the P123 solution. At the same time, use sulfuric acid to ad...
Embodiment 2
[0035] Put 1038g of water glass (Hongxing Soda Soda Factory, modulus: 3.1-3.4) into a 3000ml two-necked flask. Weigh 266g of sodium hydroxide (Beijing Chemical Plant, analytically pure), dissolve it into 400ml of deionized water, then add the sodium hydroxide solution into the water glass and stir for 30 minutes. Get 198g of aluminum sulfate (Beijing Chemical Reagent Company, analytically pure) and dissolve it in 400ml of deionized water, add the aluminum sulfate solution dropwise to the mixture of water glass and sodium hydroxide, carry out aging at 80°C, and obtain a compound containing Y after 9 hours Type molecular sieve precursor; 200g P123 (Aldrich, analytical grade) was dissolved in 7500ml deionized water, stirred at 25°C, and the pH of the P123 solution was adjusted to 1.5 with sulfuric acid. After the aging of the precursor is completed, weigh 1500g of fresh Y molecular sieve precursor emulsion and add it to the P123 solution. At the same time, use sulfuric acid to ad...
Embodiment 3
[0037] Put 1038g of water glass (Hongxing Soda Soda Factory, modulus: 3.1-3.4) into a 3000ml two-necked flask. Weigh 266g of sodium hydroxide (Beijing Chemical Plant, analytically pure), dissolve it into 400ml of deionized water, then add the sodium hydroxide solution into the water glass and stir for 30 minutes. Get 198g of aluminum sulfate (Beijing Chemical Reagent Company, analytically pure) and dissolve it in 400ml of deionized water, add the aluminum sulfate solution dropwise to the mixture of water glass and sodium hydroxide, carry out aging at 80°C, and obtain a compound containing Y after 9 hours Type molecular sieve precursor; 200g P123 (Aldrich, analytical grade) was dissolved in 7500ml deionized water, stirred at 25°C, and the pH of the P123 solution was adjusted to 1.5 with sulfuric acid. After the aging of the precursor is completed, weigh 1500g of fresh Y molecular sieve precursor emulsion and add it to the P123 solution. At the same time, use sulfuric acid to ad...
PUM
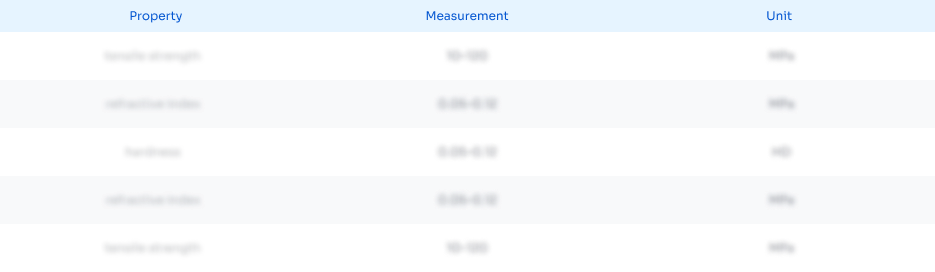
Abstract
Description
Claims
Application Information

- Generate Ideas
- Intellectual Property
- Life Sciences
- Materials
- Tech Scout
- Unparalleled Data Quality
- Higher Quality Content
- 60% Fewer Hallucinations
Browse by: Latest US Patents, China's latest patents, Technical Efficacy Thesaurus, Application Domain, Technology Topic, Popular Technical Reports.
© 2025 PatSnap. All rights reserved.Legal|Privacy policy|Modern Slavery Act Transparency Statement|Sitemap|About US| Contact US: help@patsnap.com