Method for preparing polymer-bonded magnetic refrigerating composite material
A composite material and magnetic refrigeration technology, which is applied in the direction of heat exchange materials, chemical instruments and methods, can solve the problems of reduced magnetic properties and weak bonding force of magnetocaloric alloys, and achieve strong bonding force, low cost, and simple process Effect
- Summary
- Abstract
- Description
- Claims
- Application Information
AI Technical Summary
Problems solved by technology
Method used
Image
Examples
Embodiment 1
[0015] In this embodiment, LaFe is prepared by coating metal particles with high thermal conductivity epoxy resin. 11 co 0.8 Si 1.2 alloy composites.
[0016] The composition is LaFe smelted by arc method 11 co 0.8 Si 1.2 Cast ingots, cut into small pieces, keep warm at 1050 degrees Celsius for 7 days in an argon atmosphere of 0.8 mbar, and then quench into water at room temperature. The small pieces after annealing are mechanically ground into fine particles with uniform size distribution, and the particle size is controlled between 10-100 microns. Mix the particles and high thermal conductivity epoxy resin in a polyethylene plastic container at a volume ratio of 10:1, stir evenly with a copper needle, and inject it into a copper mold. The mold was placed in a vacuum dish for degassing for 5 minutes, and then the mold was placed in a magnetic field composed of permanent magnets with a magnetic field strength of 1 Tesla. After standing for 1 week, the mold was opened to...
Embodiment 2
[0019] In this example, the method of coating metal particles with high thermal conductivity epoxy resin is used to prepare Mn 1.1 Fe 0.9 P 0.75 Ge 0.25 alloy composites.
[0020] Use Mn, Fe, P, Ge high-purity metal powder (purity greater than 99.9%) by Mn 1.1 Fe 0.9 P 0.75 Ge 0.25 The components were ball-milled for 10 hours by mechanical alloying, kept at 1000 degrees Celsius for 2 days in an argon atmosphere of 0.8 mbar, and then cooled to room temperature in the furnace. Grinding the annealed alloy into particles, the particle size is controlled between 10-100 microns. Mix the particles and high thermal conductivity epoxy resin in a polyethylene plastic container at a volume ratio of 10:1, stir evenly with a copper needle, and inject it into a copper mold. The mold was placed in a vacuum dish for degassing for 5 minutes, and then the mold was placed in a magnetic field composed of permanent magnets with a magnetic field strength of 1 Tesla. After standing for 1 we...
Embodiment 3
[0023] In this example, Ni was prepared by coating metal particles with high thermal conductivity epoxy resin. 49 mn 27 Ga 24 alloy composites.
[0024] The composition is Ni by arc melting 49 mn 27 Ga 24 Cast ingots, cut into small pieces, keep warm at 1100 degrees Celsius for 7 days in an argon atmosphere of 0.8 mbar, and then quench them into water at room temperature. The annealed small pieces are mechanically ground into particles, and the particle size is controlled at 10-100 microns. Mix the particles and high thermal conductivity epoxy resin in a polyethylene plastic container at a volume ratio of 10:1, stir evenly with a copper needle, and inject it into a copper mold. The mold was placed in a vacuum dish for degassing for 5 minutes, and then the mold was placed in a magnetic field composed of permanent magnets with a magnetic field strength of 1 Tesla. After standing for 1 week, the mold was opened to take out the cured composite material.
[0025] Heusler-ty...
PUM
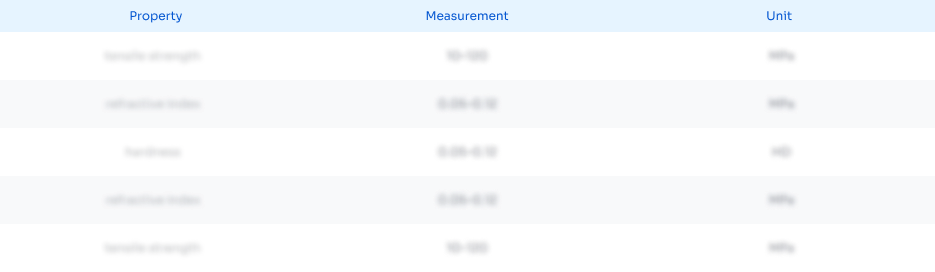
Abstract
Description
Claims
Application Information

- R&D
- Intellectual Property
- Life Sciences
- Materials
- Tech Scout
- Unparalleled Data Quality
- Higher Quality Content
- 60% Fewer Hallucinations
Browse by: Latest US Patents, China's latest patents, Technical Efficacy Thesaurus, Application Domain, Technology Topic, Popular Technical Reports.
© 2025 PatSnap. All rights reserved.Legal|Privacy policy|Modern Slavery Act Transparency Statement|Sitemap|About US| Contact US: help@patsnap.com