High-Ni-Cu alloy glass mold and method for manufacturing same
A technology for glass molds and manufacturing methods, which is applied in the field of high-nickel-content copper alloy glass molds and its manufacturing, and can solve the problems of weak corrosion resistance, easy oxidation and corrosion, difficulty in meeting high-speed production of high-speed bottle-making machines, reliable quality, etc.
- Summary
- Abstract
- Description
- Claims
- Application Information
AI Technical Summary
Problems solved by technology
Method used
Examples
Embodiment 1
[0012] The high-nickel copper alloy glass mold material contains mass ratio components: Al: 8.5%, Ni: 14.0%, Zn: 7.5%, Si: 0.8%, Fe: 0.8%, Mn: 0.08%, and the rest is Cu. First prepare a zinc-copper alloy with a mass ratio of zinc-copper of 45:55, calculate the mass of each component raw material based on 1000kg of glass mold material, melt each component raw material and 591kg of electrolytic copper in an intermediate frequency furnace to reach a temperature of 1200°C, and add zinc-copper The alloy is 167kg, heated and smelted at a temperature of 1280°C, and then heat-preserved pouring is carried out at a pouring temperature of 1260°C, and stress relief annealing is carried out after sand cleaning. During annealing, heat for 4 hours to 640°C and hold for 5.5 hours, then cool with the furnace for 8 hours to 300°C, then open the furnace door and cool to 90°C, and finally air cool to room temperature.
Embodiment 2
[0014] The high-nickel copper alloy glass mold material contains mass ratio components: Al: 9.2%, Ni: 14.5%, Zn: 8.1%, Si: 0.9%, Fe: 0.9%, Mn: 0.1%, and the rest is Cu. First prepare a zinc-copper alloy with a mass ratio of zinc-copper of 45:55, calculate the mass of each component raw material based on 1000kg of glass mold material, melt each component raw material and 564kg of electrolytic copper in an intermediate frequency furnace to reach a temperature of 1220°C, and add zinc-copper The alloy is 180kg, and the heating and smelting temperature reaches 1285°C, and then thermal insulation casting is adopted, and the pouring temperature is 1260°C, and stress relief annealing is carried out after sand cleaning. During annealing, heat for 4.5 hours to 645°C and hold for 5.7 hours, then cool with the furnace for 8.5 hours to 305°C, then open the furnace door and cool to 90°C, and finally air cool to room temperature.
Embodiment 3
[0016] The high-nickel copper alloy glass mold material contains mass ratio components: Al: 9.9%, Ni: 15.0%, Zn: 9.0%, Si: 1.0%, Fe: 1.0%, Mn: 0.12%, and the rest is Cu. First prepare a zinc-copper alloy with a mass ratio of zinc-copper of 45:55, calculate the mass of each component raw material based on 1000kg of glass mold material, melt each component raw material and electrolytic copper 530kg in an intermediate frequency furnace to reach a temperature of 1235°C, and add zinc-copper The alloy is 200kg, the heating and smelting temperature reaches 1290°C, and then thermal insulation casting is adopted, the pouring temperature is 1270°C, and stress relief annealing is carried out after sand cleaning. During annealing, heat for 5 hours to 645°C and hold for 6 hours, then cool with the furnace for 9 hours to 305°C, then open the furnace door and cool to 95°C, and finally air cool to room temperature.
PUM
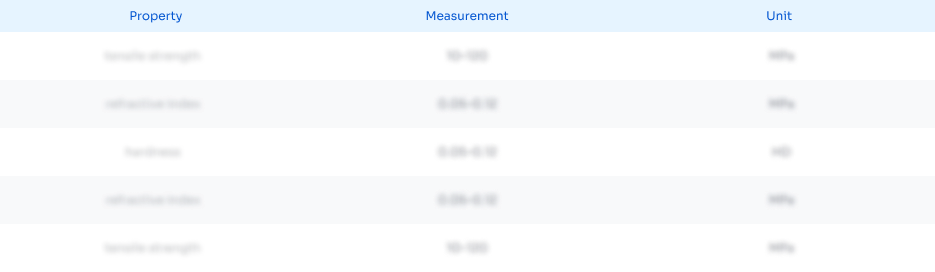
Abstract
Description
Claims
Application Information

- R&D
- Intellectual Property
- Life Sciences
- Materials
- Tech Scout
- Unparalleled Data Quality
- Higher Quality Content
- 60% Fewer Hallucinations
Browse by: Latest US Patents, China's latest patents, Technical Efficacy Thesaurus, Application Domain, Technology Topic, Popular Technical Reports.
© 2025 PatSnap. All rights reserved.Legal|Privacy policy|Modern Slavery Act Transparency Statement|Sitemap|About US| Contact US: help@patsnap.com