Method for preparing color fluorescent nanometer resin particle dispersion liquid
A fluorescent nanometer and resin particle technology, applied in chemical instruments and methods, luminescent materials, etc., can solve the problems of low tinting strength, demulsification gel, poor product purity, etc., to achieve good temperature resistance, small and uniform particle size, bright color effect
- Summary
- Abstract
- Description
- Claims
- Application Information
AI Technical Summary
Problems solved by technology
Method used
Examples
Embodiment 1
[0033] Preparation of polymerization medium initiation system: a 500 ml four-neck flask equipped with a stirrer, thermometer, nitrogen tube and reflux condenser was placed in a super constant temperature water bath, 63 grams of water was added to the four-necked flask, and then 0.43 grams of supernatant was added. Potassium sulfate, stir and dissolve evenly, then heat up to 73°C, turn on nitrogen protection, and maintain a constant temperature;
[0034] Preparation of monomer emulsion system: add 63 grams of water, 0.8 grams of polyvinyl alcohol, 2.3 grams of sodium dodecylbenzenesulfonate, 1.9 grams of fatty alcohol polyoxyethylene ether ammonium sulfate in another container with agitator, 2.1 Add 54.2 grams of styrene, 27.5 grams of acrylonitrile, 4.5 grams of hydroxypropyl methacrylate, and 0.14 grams of potassium persulfate, and continue to stir to form a uniform monomer emulsion system.
[0035] Polymerization reaction: The emulsion in the monomer emulsion system is dripp...
Embodiment 2
[0037] Preparation of polymerization medium initiation system: put a 500 ml four-necked flask equipped with a stirrer, thermometer, nitrogen tube and reflux condenser in a super constant temperature water bath, add 40 grams of water to the four-necked flask, start stirring, and then add 0.43 g of ammonium persulfate, stir and dissolve evenly, then heat up to 68°C, turn on nitrogen protection, and maintain a constant temperature;
[0038] Preparation of monomer emulsion system: add 86 grams of water, 0.6 gram of polyoxyethylene alcohol, 2.3 gram of sodium tridecylbenzenesulfonate, 1.9 gram of sodium fatty alcohol polyoxyethylene ether sulfate in another container with agitator, 1.5 grams of RHODAMINE B, 0.6 grams of RHODAMINE 6G, stirring to dissolve into a uniform solution; then add 54.2 grams of methyl styrene, 27.5 grams of 3-pentanecyanide, 4.5 grams of ethyl acrylate, 0.14 grams of ammonium persulfate, continue to stir to form a uniform monomer Emulsion system.
[0039] P...
Embodiment 3
[0041] Preparation of polymerization medium initiation system: put a 500 ml four-necked flask equipped with a stirrer, thermometer, nitrogen tube and reflux condenser in a super constant temperature water bath, add 50 grams of water to the four-necked flask, start stirring, and then add 0.50 g of potassium persulfate was stirred and dissolved evenly, then heated to 70°C, nitrogen protection was turned on, and the temperature was maintained at a constant temperature.
[0042] Preparation of monomer emulsion system: add 86 grams of water, 0.5 grams of hydroxyethyl cellulose, 2.3 grams of alkylphenol polyoxyethylene sodium sulfate, 1.9 grams of fatty alcohol polyoxyethylene ether ammonium sulfate into another container with agitator , 0.8 grams of RHODAMINE B, 1.6 grams of RHODAMINE 6G, stir and dissolve into a uniform solution; then add 54.2 grams of ethyl styrene, 27.5 grams of methacrylonitrile, 1.5 grams of glycidyl methacrylate, 0.14 grams of potassium persulfate, and continu...
PUM
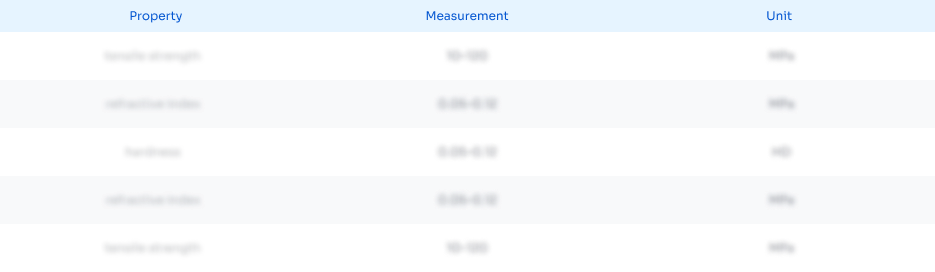
Abstract
Description
Claims
Application Information

- R&D
- Intellectual Property
- Life Sciences
- Materials
- Tech Scout
- Unparalleled Data Quality
- Higher Quality Content
- 60% Fewer Hallucinations
Browse by: Latest US Patents, China's latest patents, Technical Efficacy Thesaurus, Application Domain, Technology Topic, Popular Technical Reports.
© 2025 PatSnap. All rights reserved.Legal|Privacy policy|Modern Slavery Act Transparency Statement|Sitemap|About US| Contact US: help@patsnap.com