Antibacterial film coating member and its preparation method
An antibacterial coating, nickel chromium nitrogen technology, applied in the field of antibacterial coating parts and its preparation, can solve the problems of reducing the antibacterial durability of metal antibacterial coatings, loss of antibacterial metal ions, and low surface hardness
- Summary
- Abstract
- Description
- Claims
- Application Information
AI Technical Summary
Problems solved by technology
Method used
Image
Examples
preparation example Construction
[0024] The preparation method of the antibacterial coating part 10 of a preferred embodiment of the present invention, it comprises the steps:
[0025] A substrate 11 is provided, and the material of the substrate 11 is preferably stainless steel, but not limited to stainless steel.
[0026] The substrate 11 is subjected to surface pretreatment. The surface pretreatment may include conventional steps of polishing the substrate 11 , ultrasonic cleaning with absolute ethanol, and drying.
[0027] Argon plasma cleaning is performed on the surface of the substrate 11 after the above treatment to further remove impurities remaining on the surface of the substrate 11 and improve the bonding force between the surface of the substrate 11 and the subsequent coating. combined reference figure 2 , provide a vacuum coating machine 20, the vacuum coating machine 20 includes a coating chamber 21 and a vacuum pump 30 connected to the coating chamber 21, the vacuum pump 30 is used to evacu...
Embodiment 1
[0035] The vacuum coating machine 20 used in this embodiment is a magnetron sputtering coating machine.
[0036] The material of the substrate 11 used in this embodiment is stainless steel.
[0037] Plasma cleaning: the flow rate of argon gas is 500 sccm, the bias voltage of the substrate 11 is -200V, and the plasma cleaning time is 5 minutes;
[0038] Sputtering primer layer 13: the mass percentage of nickel in the nickel-chromium alloy target 23 is 35%, the power of the nickel-chromium alloy target 23 is 7kw, the flow rate of argon gas is 420sccm, the bias voltage of the substrate 11 is -100V, and the coating temperature is The temperature is 80°C, and the coating time is 6 minutes; the thickness of the primer layer 13 is 185nm;
[0039] Sputtering nickel-chromium-nitrogen layer 15: the power of nickel-chromium alloy target 23 is 8kw, the flow rate of argon gas is 400 sccm, the flow rate of nitrogen gas is 60 sccm, the bias voltage of substrate 11 is -80V, the coating tempe...
Embodiment 2
[0043] The vacuum coating machine 20 and the substrate 11 used in this embodiment are the same as those in Embodiment 1.
[0044] Plasma cleaning: the flow rate of argon gas is 500 sccm, the bias voltage of the substrate 11 is -200V, and the plasma cleaning time is 5 minutes;
[0045] Sputtering primer layer 13: the mass percentage of nickel in the nickel-chromium alloy target 23 is 40%, the power of the nickel-chromium alloy target 23 is 7kw, the flow rate of argon gas is 420sccm, the bias voltage of the substrate 11 is -100V, and the coating temperature is The temperature is 80°C, and the coating time is 5 minutes; the thickness of the primer layer 13 is 185nm;
[0046] Sputtering nickel-chromium-nitrogen layer 15: the power of nickel-chromium alloy target 23 is 7kw, the flow rate of argon gas is 400sccm, the flow rate of nitrogen gas is 100sccm, the bias voltage of substrate 11 is -80V, the coating temperature is 80°C, and the coating time is 5min; The thickness of the nic...
PUM
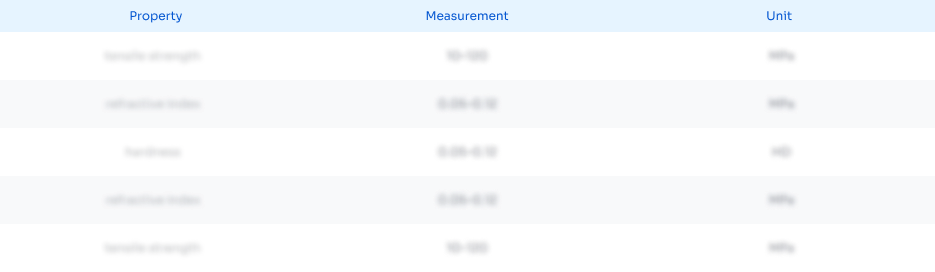
Abstract
Description
Claims
Application Information

- R&D
- Intellectual Property
- Life Sciences
- Materials
- Tech Scout
- Unparalleled Data Quality
- Higher Quality Content
- 60% Fewer Hallucinations
Browse by: Latest US Patents, China's latest patents, Technical Efficacy Thesaurus, Application Domain, Technology Topic, Popular Technical Reports.
© 2025 PatSnap. All rights reserved.Legal|Privacy policy|Modern Slavery Act Transparency Statement|Sitemap|About US| Contact US: help@patsnap.com