Organic heat carrier waste-heat furnace and waste-heat furnace system
A waste heat furnace and carrier technology, applied in furnaces, waste heat treatment, furnace components, etc., can solve the problems of increasing equipment manufacturing costs and use and maintenance costs, affecting the effect of waste heat recovery from flue gas, and reducing the life of heat exchange devices, and achieving a simple structure. , high effectiveness, low installation difficulty
- Summary
- Abstract
- Description
- Claims
- Application Information
AI Technical Summary
Problems solved by technology
Method used
Image
Examples
Embodiment Construction
[0028] Such as figure 1As shown, an organic heat carrier waste heat furnace according to the present invention includes a waste heat furnace body 2 and a settling chamber 1. A flue gas inlet 12 is provided on one side wall of the settling chamber 1, and the other side wall of the settling chamber 1 is connected by 3 One side wall of the waste heat furnace body 2, the other side wall of the waste heat furnace body 2 is provided with a flue gas outlet 13, the settling chamber membrane wall tube screen 4 is set in the settling chamber 1, the top of the settling chamber membrane wall tube screen 4 is connected with the top of the settling chamber 1 Connection, there is a flue gas channel at the bottom of the membrane wall tube panel 4 in the settling chamber, a number of convection sections parallel to each other are arranged in the waste heat furnace body 2, and each adjacent convection section is separated by a smoke folding device, and each adjacent smoke folding section The de...
PUM
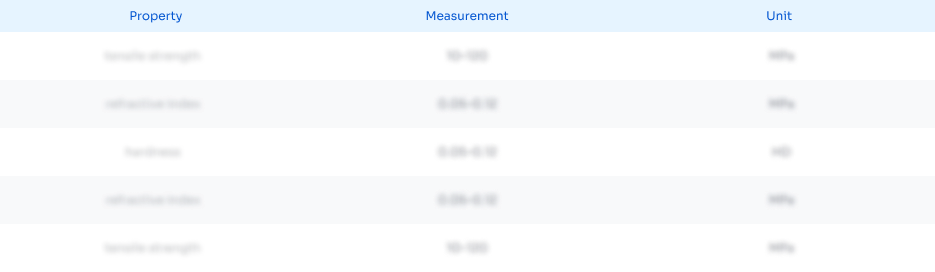
Abstract
Description
Claims
Application Information

- R&D
- Intellectual Property
- Life Sciences
- Materials
- Tech Scout
- Unparalleled Data Quality
- Higher Quality Content
- 60% Fewer Hallucinations
Browse by: Latest US Patents, China's latest patents, Technical Efficacy Thesaurus, Application Domain, Technology Topic, Popular Technical Reports.
© 2025 PatSnap. All rights reserved.Legal|Privacy policy|Modern Slavery Act Transparency Statement|Sitemap|About US| Contact US: help@patsnap.com