Aluminum brass alloy and preparation method thereof
An aluminum-brass and alloy technology, which is applied in the field of aluminum-brass alloy and its preparation, can solve the problems of leakage of pipes and can not meet the service life requirements of power station condensers, and achieves improved casting performance, improved service life, and refined structure. Effect
- Summary
- Abstract
- Description
- Claims
- Application Information
AI Technical Summary
Problems solved by technology
Method used
Examples
Embodiment 1
[0070] Put Cu with a mass percentage of 56% into a power frequency furnace for smelting (the balance of copper is brought in through the intermediate alloy), and after the copper starts to soften, a layer of charcoal is covered on the copper surface. The amount of charcoal is 8-10kg per ton of copper. The melting temperature is 1180-1200°C. Add 0.15% Ni by mass percentage to the molten copper liquid to dissolve metallic nickel into the copper liquid through alloying. The temperature of the copper liquid is adjusted to 1180-1200°C, and 23% by mass of Zn is added to the copper liquid to dissolve the metal zinc into the copper liquid through alloying. After the zinc is melted, adjust the temperature of the copper liquid to 1130-1160 ° C, add 20% Cu and 2.1% aluminum to the copper liquid at the same time, and use a large amount of hot melt metal copper cold material released when the aluminum is dissolved . Add Cu-Zr, Cu-Ti and Cu-B intermediate alloys to the copper liquid so t...
Embodiment 2
[0074] Put Cu with a mass percentage of 59% into a power frequency furnace for smelting (the balance of copper is brought in through the intermediate alloy), and after the copper starts to soften, a layer of charcoal is covered on the copper surface. The amount of charcoal is 8-10kg per ton of copper. The melting temperature is 1180-1200°C. 1.2% Ni by mass percentage is added to the molten copper liquid to dissolve metallic nickel into the copper liquid through alloying. The temperature of the copper liquid is adjusted to 1190-1210°C, and 20% by mass of Zn is added to the copper liquid to dissolve the metal zinc into the copper liquid through alloying. After the zinc is melted, adjust the temperature of the copper liquid to between 1130-1160 ° C, add 20% Cu and 2.8% aluminum by mass to the copper liquid at the same time, and use the large amount of hot-melted metal copper cold material released when the aluminum is dissolved . Add Cu-Zr, Cu-Ti and Cu-B intermediate alloys t...
Embodiment 3
[0078] Put Cu with a mass percentage of 56% into a power frequency furnace for smelting (the balance of copper is brought in through the intermediate alloy), and after the copper starts to soften, a layer of charcoal is covered on the copper surface. The amount of charcoal is 8-10kg per ton of copper. The melting temperature is 1180-1200°C. Add 0.10% Ni by mass percentage to the molten copper liquid, so that metallic nickel can be dissolved into the copper liquid through alloying. The temperature of the copper liquid is adjusted to 1180-1200°C, and 23% by mass of Zn is added to the copper liquid to dissolve the metal zinc into the copper liquid through alloying. After the zinc is melted, adjust the temperature of the copper liquid to 1130-1160 ° C, add 20% Cu and 2.1% aluminum to the copper liquid at the same time, and use a large amount of hot melt metal copper cold material released when the aluminum is dissolved . Add the Cu-Fe master alloy to the copper liquid to make t...
PUM
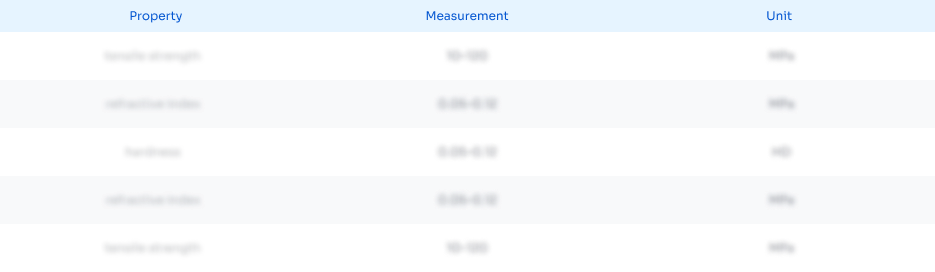
Abstract
Description
Claims
Application Information

- R&D
- Intellectual Property
- Life Sciences
- Materials
- Tech Scout
- Unparalleled Data Quality
- Higher Quality Content
- 60% Fewer Hallucinations
Browse by: Latest US Patents, China's latest patents, Technical Efficacy Thesaurus, Application Domain, Technology Topic, Popular Technical Reports.
© 2025 PatSnap. All rights reserved.Legal|Privacy policy|Modern Slavery Act Transparency Statement|Sitemap|About US| Contact US: help@patsnap.com