Metamorphic process of hypo eutectic casting aluminum-silicon alloy
A technology for casting aluminum-silicon alloys and aluminum-silicon master alloys, which is applied in the field of hypoeutectic casting aluminum-silicon alloy modification technology, and can solve problems such as single function, complicated processing technology, and easy volatility
- Summary
- Abstract
- Description
- Claims
- Application Information
AI Technical Summary
Problems solved by technology
Method used
Image
Examples
Embodiment 1
[0020] Embodiment 1: The method for modifying Zl114 alloy by rare earth Sc in this embodiment is realized through the following steps:
[0021] 1) Ingredients according to Z1114 alloy composition: Si: 6.5-7.5, Mg: 0.45-0.60, Ti: 0.10-0.20, Be: 0.04-0.07, Fe (sand casting): ≤0.2, Mn: ≤0.1, Al: balance , The sum of impurities: (sand casting) ≤ 0.75.
[0022] 2) After cleaning and drying the pure aluminum, aluminum-silicon master alloy, aluminum-manganese master alloy, aluminum-titanium master alloy prepared in step 1), put them into a graphite clay crucible resistance furnace with a power of 5KW, and heat and melt them completely.
[0023] 3) Press the pure Mg weighed in step 1) into the melt obtained in step 2) in a graphite bell jar with a preheating temperature of 300°C at 700°C, and let it stand for 5 minutes;
[0024] 4) Heat up the melt obtained in step 3) to 740°C, add the weighed AlSc 4 The amount of the intermediate alloy (Sc) accounts for 0.15wt% of the total amount ...
Embodiment 2
[0027] Embodiment 2: The method for modifying Zl107 alloy by rare earth Sc in this embodiment is realized through the following steps:
[0028] 1) According to the composition of Zl107 alloy: Si: 6.5~7.4, Cu: 3.5~4.5, Zn: 0.8~1.2, Mg: 0.1~0.2, Cd: 0.1~0.2, Fe≤0.12, Ti: 0.1~0.2, Al: margin.
[0029] 2) After cleaning and drying the pure aluminum, aluminum-silicon master alloy, aluminum-copper master alloy, aluminum-manganese master alloy, aluminum-titanium master alloy prepared in step 1), put them into a graphite clay crucible resistance furnace with a power of 5KW, and heat them completely melt.
[0030] 3) Press the pure Mg weighed in step 1 into the melt obtained in step 2) in a graphite bell jar with a preheating temperature of 300°C at 700°C, and let it stand for 3 minutes;
[0031] 4) Heat up the melt obtained in step 3) to 760°C, add the weighed AlSc4 master alloy (the amount of Sc added accounts for 0.18wt% of the total amount of the alloy), and after the melting is ...
Embodiment 3
[0034] Embodiment 3: The method for modifying Zl702 alloy by rare earth Sc in this embodiment is realized through the following steps:
[0035] 1) According to the composition of Zl702 alloy: Si: 6.0-7.0, Cu: 1.5, Mg: 0.35, Ti: 0.1-0.2, Mn: 0.1-0.2, Fe≤0.2, Al: balance.
[0036] 2) After cleaning and drying the pure aluminum, aluminum-silicon master alloy, aluminum-copper master alloy, aluminum-manganese master alloy, aluminum-titanium master alloy prepared in step 1), put them into a graphite clay crucible resistance furnace with a power of 5KW, and heat them completely melt.
[0037] 3) Press the pure Mg weighed in step 1) into the melt obtained in step 2) in a graphite bell jar with a preheating temperature of 300°C at 700°C, and let it stand for 3 minutes;
[0038] 4) Heat up the melt obtained in step 3) to 750°C, add the weighed AlSc4 master alloy (the amount of Sc added accounts for 0.2wt% of the total amount of the alloy), and after the melting is completed, use the ro...
PUM
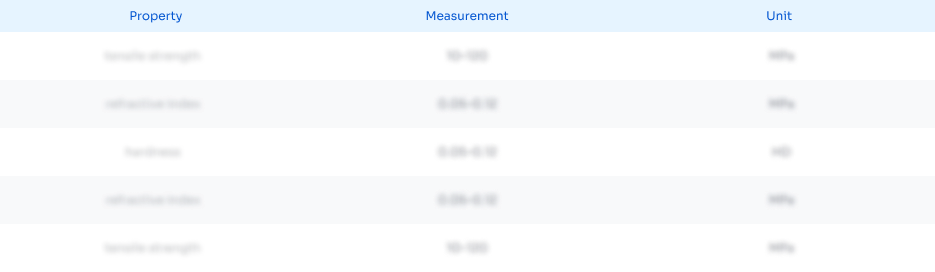
Abstract
Description
Claims
Application Information

- R&D Engineer
- R&D Manager
- IP Professional
- Industry Leading Data Capabilities
- Powerful AI technology
- Patent DNA Extraction
Browse by: Latest US Patents, China's latest patents, Technical Efficacy Thesaurus, Application Domain, Technology Topic, Popular Technical Reports.
© 2024 PatSnap. All rights reserved.Legal|Privacy policy|Modern Slavery Act Transparency Statement|Sitemap|About US| Contact US: help@patsnap.com