Preparation method of electric co-depositing zinc magnesium alloy plating layer in aqueous solution
An alloy coating and co-deposition technology, which is applied in the field of metal surface corrosion protection, can solve the problems of reduced coating smoothness, easy blackening of the coating, and high current density, so as to reduce the deposition rate of zinc, improve corrosion resistance, and increase current density. efficiency effect
- Summary
- Abstract
- Description
- Claims
- Application Information
AI Technical Summary
Problems solved by technology
Method used
Examples
Embodiment 1
[0024] The preparation steps of this embodiment are as follows:
[0025] a. Preparation of acidic plating solution: Weigh 100 g of zinc sulfate heptahydrate and 50 g of magnesium sulfate heptahydrate, dissolve them in distilled water, and prepare 1 L of plating solution.
[0026] b. Add 2.5g / L polyethylene glycol in the plating solution as a surfactant.
[0027] c. Add tartaric acid of 50g / L and sodium hypophosphite of 100g / L in the plating solution, then adjust the pH value of the plating solution to 1 with concentrated sulfuric acid. Place the plating solution in a water bath at 60°C. Magnetic stirring.
[0028] d. Deposit by direct current electroplating method; use cold-rolled low-carbon steel plate for automobiles as cathode electroplating material, use platinum electrode as anode, and feed 2A / cm 2 DC current; electroplating for 2 minutes; finally, an alloy coating of 0.878wt% magnesium was obtained through measurement and conversion.
Embodiment 2
[0030] The preparation steps of this embodiment are as follows:
[0031] a. Preparation of acidic plating solution: Weigh 150 g of zinc sulfate heptahydrate and 100 g of magnesium sulfate heptahydrate, dissolve them in distilled water, and prepare 1 L of plating solution.
[0032] b. Add 1g / L polyethylene glycol as a surfactant in the plating solution.
[0033] c. add the tartaric acid of 200g / L and the sodium hypophosphite of 500g / L again in the plating solution, then adjust the pH value of the plating solution to 1.5 with concentrated sulfuric acid. Place the plating solution in a water bath at 60°C. Magnetic stirring.
[0034] d. Deposit by DC electroplating method; use steel plate as cathodic electroplating material, use platinum electrode as anode, pass through 0.5A / cm 2 DC current; electroplating for 5 minutes; finally, an alloy coating of 1.024wt% magnesium was obtained through measurement and conversion.
Embodiment 3
[0036] The preparation steps of this embodiment are as follows:
[0037] a. Preparation of acidic plating solution: Weigh 350 g of zinc sulfate heptahydrate and 200 g of magnesium sulfate heptahydrate, dissolve them in distilled water, and prepare 1 L of plating solution.
[0038] b. Add 4g / L polyethylene glycol in the plating solution as a surfactant.
[0039] c. Add 120g / L of tartaric acid and 100g / L of sodium hypophosphite in the plating solution, then adjust the pH value of the plating solution to 2 with concentrated sulfuric acid. Place the plating solution in a water bath at 60°C. Magnetic stirring.
[0040] d. Deposit by direct current electroplating method; use cold-rolled low-carbon steel plate for automobiles as cathode electroplating material, use platinum electrode as anode, and feed 1A / cm 2 DC current; electroplating for 3.5min; and finally through measurement and conversion to obtain an alloy coating of 1.987wt% magnesium.
PUM
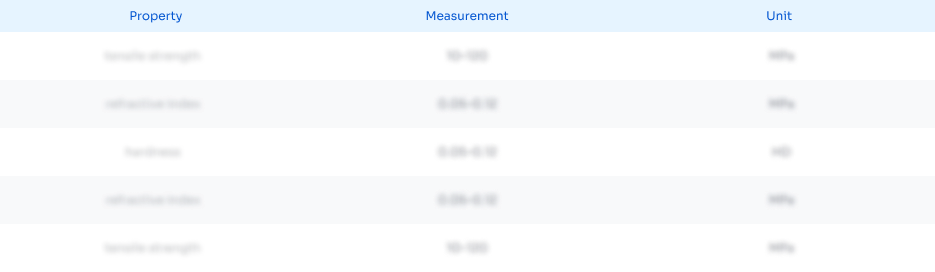
Abstract
Description
Claims
Application Information

- R&D
- Intellectual Property
- Life Sciences
- Materials
- Tech Scout
- Unparalleled Data Quality
- Higher Quality Content
- 60% Fewer Hallucinations
Browse by: Latest US Patents, China's latest patents, Technical Efficacy Thesaurus, Application Domain, Technology Topic, Popular Technical Reports.
© 2025 PatSnap. All rights reserved.Legal|Privacy policy|Modern Slavery Act Transparency Statement|Sitemap|About US| Contact US: help@patsnap.com