Vitrification agent, preparation method thereof and vitrification process
A vitrifying agent and process technology, which is applied in the direction of metal material coating process, etc., can solve the problems of poor adhesion, short salt spray resistance time, poor corrosion resistance, etc., to prolong the corrosion resistance time, excellent rust resistance, Avoid the effect of returning rust
- Summary
- Abstract
- Description
- Claims
- Application Information
AI Technical Summary
Problems solved by technology
Method used
Examples
Embodiment 1
[0031] The present embodiment discloses a ceramizer and its preparation method and ceramization process, which specifically include the following contents:
[0032] The ceramic agent comprises the following components in parts by weight: 5 parts of fluorozirconic acid, 15 parts of bisaminosilane, 6 parts of monoethanolamine borate, 1 part of sodium nitrite, 3 parts of pH adjuster, and 50 parts of water . The water is deionized water, and the pH adjusting agent is ammonia water.
[0033] The preparation method of the potting agent comprises the following steps:
[0034] Step 1: Weigh each component according to parts by weight;
[0035] Step 2: Add 70% water into the mixing tank, then add fluorozirconic acid, bisaminosilane, monoethanolamine borate, and sodium nitrite in sequence, stir evenly to obtain a pre-mixed solution, and the stirring time is 0.5h;
[0036] Step 3: Add the remaining 30% of water to the tank;
[0037] Step 4: detecting the pH value of the pre-preparati...
Embodiment 2
[0047] The present embodiment discloses a ceramizer and its preparation method and ceramization process, which specifically include the following contents:
[0048] The ceramic agent comprises the following components in parts by weight: 8 parts of fluorozirconic acid, 20 parts of bisaminosilane, 10 parts of monoethanolamine borate, 4 parts of sodium nitrite, 9 parts of pH adjuster, and 80 parts of water . The water is tap water, and the pH adjuster is sodium hydroxide.
[0049] The preparation method of the potting agent comprises the following steps:
[0050] Step 1: Weigh each component according to parts by weight;
[0051] Step 2: Add 70% water into the mixing tank, then add fluorozirconic acid, bisaminosilane, monoethanolamine borate, and sodium nitrite in sequence, and stir evenly to obtain a pre-mixed solution, and the stirring time is 1 h;
[0052] Step 3: Add the remaining 30% of water to the tank;
[0053] Step 4: Detecting the pH value of the pre-preparation so...
Embodiment 3
[0063] The present embodiment discloses a ceramizer and its preparation method and ceramization process, which specifically include the following contents:
[0064] The ceramic agent comprises the following components in parts by weight: 10 parts of fluorozirconic acid, 25 parts of bisaminosilane, 15 parts of monoethanolamine borate, 7 parts of sodium nitrite, 16 parts of pH adjuster, and 100 parts of water . The water is deionized water, and the pH adjusting agent is ammonia water.
[0065] The preparation method of the potting agent comprises the following steps:
[0066] Step 1: Weigh each component according to parts by weight;
[0067] Step 2: add 70% water into the mixing tank, then add fluorozirconic acid, bisaminosilane, monoethanolamine borate, and sodium nitrite in sequence, and stir evenly to obtain a pre-mixed solution, and the stirring time is 1.5h;
[0068] Step 3: Add the remaining 30% of water to the tank;
[0069] Step 4: Detecting the pH value of the pre-pr...
PUM
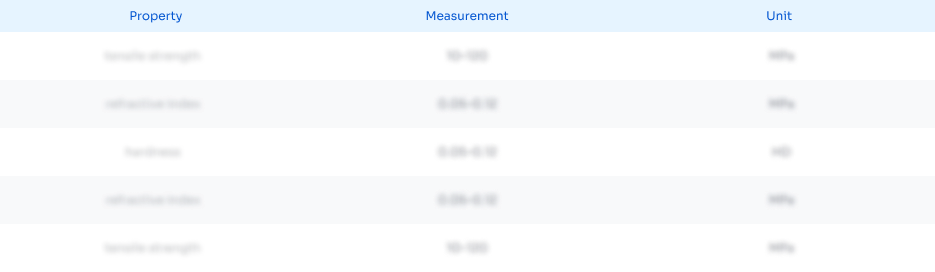
Abstract
Description
Claims
Application Information

- R&D Engineer
- R&D Manager
- IP Professional
- Industry Leading Data Capabilities
- Powerful AI technology
- Patent DNA Extraction
Browse by: Latest US Patents, China's latest patents, Technical Efficacy Thesaurus, Application Domain, Technology Topic, Popular Technical Reports.
© 2024 PatSnap. All rights reserved.Legal|Privacy policy|Modern Slavery Act Transparency Statement|Sitemap|About US| Contact US: help@patsnap.com