Machining method of target surface
A processing method and target material technology, which is applied in metal processing equipment, manufacturing tools, grinding machines, etc., can solve the problems of inability to process the ratio of length and thickness, partial viscosity of properties, etc., and achieve low requirements on the surface of the target material, thin stress layer, and requirements low effect
- Summary
- Abstract
- Description
- Claims
- Application Information
AI Technical Summary
Problems solved by technology
Method used
Examples
Embodiment 1
[0034] Two pieces of pure nickel target material blanks with a diameter of 400 mm and a thickness of 3.3 mm were processed by a common lathe, and then continued to use the common lathe for surface processing and the equipment of the present invention for surface processing respectively.
[0035] When using an ordinary lathe for processing, the ordinary lathe uses a diamond knife with a speed of 250r / min and a feed rate of 0.1mm. Turning is performed from the outer circle to the center.
[0036] After processing, the nickel target is removed from the jaws of the lathe. It was found that due to the processing stress, the core and the outer diameter of the target protruded and deformed.
[0037] Using the method of the present invention to grind and polish the nickel target blank comprises the following steps:
[0038] 1) The surface of the processed target blank is rough machined by a lathe, and the surface roughness Ra after rough machining is 1.7 μm.
[0039] 2) The use of ...
Embodiment 2
[0046] Two pure titanium target blanks with a length of 800 mm, a width of 100 mm, and a thickness of 8.4 mm rough-processed by a planer were respectively processed by a planer and the grinding and polishing equipment adopted in the present invention.
[0047] The pure titanium target blank processed by a planer has a roughness Ra of 5.5 μm.
[0048] A target with a large length-to-thickness ratio for surface processing using mechanical grinding and polishing equipment, including the following steps:
[0049] 1) The surface of the target material to be processed is rough machined by a planer, and the surface roughness Ra after rough machining is 5.5 μm.
[0050] 2) Use mechanical grinding and polishing equipment to adjust the opening width of the parallel rollers to 8mm;
[0051] 3) The parallel rollers of the mechanical grinding and polishing equipment are wrapped with water sandpaper abrasive belts, and the rotation of the rollers drives the abrasive belts and cloth to rota...
Embodiment 3
[0057] Two pure copper target blanks with a length of 100mm, a width of 100mm, and a thickness of 5.5mm. Use the planer and the grinding and polishing equipment adopted in the present invention to process respectively.
[0058] The pure copper target blank processed by a planer has a roughness Ra of 6.3 μm.
[0059] The target material for surface processing using mechanical grinding and polishing equipment includes the following steps:
[0060] 1) The surface roughness Ra of the copper target blank processed by the planer is 6.3 μm;
[0061] 2) Adjust the two parallel rollers of the mechanical grinding and polishing equipment, and the opening width is 5mm;
[0062] 3) The water sandpaper abrasive belt is wrapped on the parallel roller shaft, and the abrasive belt and cloth are driven to rotate through the rotation of the roller shaft, and the surface of the target is ground and polished. At the same time, deionized water is used for rinsing and lubrication. The rotational s...
PUM
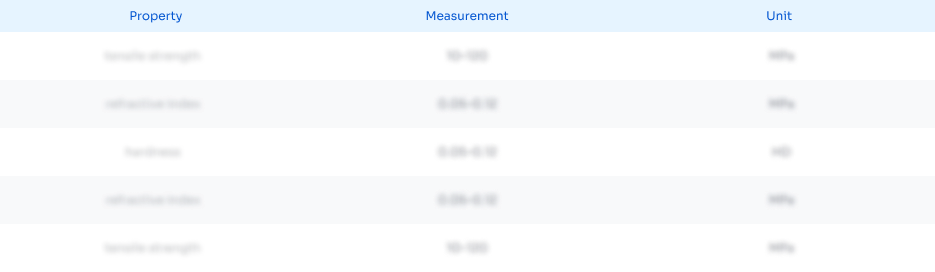
Abstract
Description
Claims
Application Information

- R&D
- Intellectual Property
- Life Sciences
- Materials
- Tech Scout
- Unparalleled Data Quality
- Higher Quality Content
- 60% Fewer Hallucinations
Browse by: Latest US Patents, China's latest patents, Technical Efficacy Thesaurus, Application Domain, Technology Topic, Popular Technical Reports.
© 2025 PatSnap. All rights reserved.Legal|Privacy policy|Modern Slavery Act Transparency Statement|Sitemap|About US| Contact US: help@patsnap.com