Method for preparing silicon carbide particle reinforced aluminum-based composites
A silicon carbide particle-reinforced aluminum-based technology, which is applied in the field of preparing silicon carbide particle-reinforced aluminum-based composite materials, can solve the problems of weakening the comprehensive performance of the composite material, making it difficult for the composite material to penetrate completely, and the density is difficult to achieve complete uniformity. Openness, low cost, no segregation effect
- Summary
- Abstract
- Description
- Claims
- Application Information
AI Technical Summary
Problems solved by technology
Method used
Examples
Embodiment 1
[0018] Example 1: Preparation of silicon carbide particle-reinforced aluminum-based composite material with SiC particle volume fraction of 50%
[0019] Use silicon carbide powder with a particle size of 70# and 180# respectively, and mix them at a volume ratio of 1:1. According to the volume of silicon carbide, according to the volume ratio of silicon carbide: binder: pore-forming agent 8:3:2, the added The binder is sodium stearate, the pore-forming agent is starch, put it into a mixer, and stir for 1.5 hours at a temperature of 80-100°C to obtain uniform silicon carbide mixed particles, put it into a mold of a press, and grind it at 50-100°C Under the pressure of 200MP, control and calculate the volume of the preform. After the free impregnation of the aluminum liquid, the volume fraction of the aluminum matrix is 50%. Press the preform of the desired shape and dry it in a drying room at 80-120°C. . Put the pressed silicon carbide particle preform in an atmospheric atmos...
Embodiment 2
[0020] Example 2: Preparation of silicon carbide particle-reinforced aluminum-based composite material with SiC particle volume fraction of 60%
[0021] Use silicon carbide powder with a particle size of 70# and 150# respectively, and mix them at a volume ratio of 1:2. According to the volume of silicon carbide, according to the volume ratio of silicon carbide: binder: pore-forming agent 7:2:3, add The binder is paraffin, and the pore-forming agent is stearic acid. Put it into a mixer and stir for 2.0 hours at a temperature of 80-100°C to obtain uniform silicon carbide mixed particles. Under the pressure of 200MP, control and calculate the volume of the preform. After free impregnation of the aluminum liquid, the volume fraction of the aluminum matrix is 40%. Press the preform of the required shape and dry it in a drying room at 80-120°C. . Put the pressed silicon carbide particle preform in an atmospheric atmosphere furnace, heat it up to 350°C with the furnace at a heatin...
Embodiment 3
[0022] Example 3: Preparation of silicon carbide particle-reinforced aluminum-based composite material with SiC particle volume fraction of 45%
[0023] Use silicon carbide powder with a particle size of 100# and 150# respectively, and mix them at a volume ratio of 2:1. According to the volume of silicon carbide, according to the volume ratio of silicon carbide: binder: pore-forming agent 9:4:2, the added The binder is silica sol, and the pore-forming agent is graphite. Put it into a mixer and stir for 1.2 hours at a temperature of 80-100°C to obtain uniform silicon carbide mixed particles. Under pressure, control and calculate the volume of the preform. After free impregnation with aluminum liquid, the volume fraction of the aluminum matrix is 55%. Press the preform of the required shape and dry it in a drying room at 80-120°C. Place the pressed silicon carbide particle preform in an atmospheric atmosphere furnace, heat it up to 400°C with the furnace at a heating rate of 3...
PUM
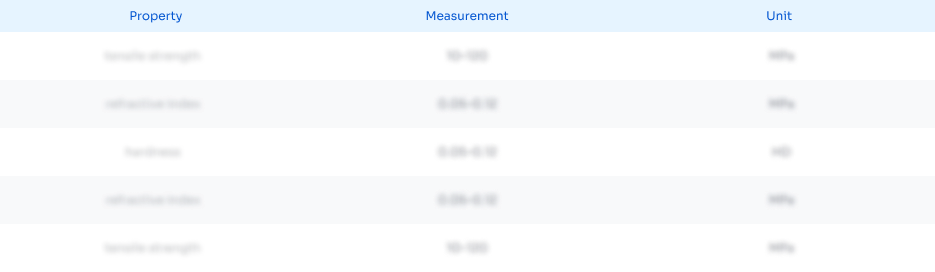
Abstract
Description
Claims
Application Information

- R&D
- Intellectual Property
- Life Sciences
- Materials
- Tech Scout
- Unparalleled Data Quality
- Higher Quality Content
- 60% Fewer Hallucinations
Browse by: Latest US Patents, China's latest patents, Technical Efficacy Thesaurus, Application Domain, Technology Topic, Popular Technical Reports.
© 2025 PatSnap. All rights reserved.Legal|Privacy policy|Modern Slavery Act Transparency Statement|Sitemap|About US| Contact US: help@patsnap.com