Preparation method of low-strength low-elongation terylene filament
A polyester filament and drawing technology, applied in the field of polyester filament, can solve the problems of unmodified light resistance, insufficient moisture absorption and air permeability of fabrics, insufficient heat resistance and thermal stability, etc. Reduced pilling, improved gloss retention, and strong cohesion
- Summary
- Abstract
- Description
- Claims
- Application Information
AI Technical Summary
Problems solved by technology
Method used
Examples
Embodiment 1
[0030] Prepare modified polyester, the modified polyester raw material:
[0031] Terephthalic acid;
[0032] Ethylene glycol, relative to terephthalic acid molar ratio 1.3:1;
[0033] Inorganic submicron particles, CaCO 3 or CaSO 4 , 0.5% relative to the mass of terephthalic acid;
[0034] Catalyst, antimony glycol or antimony trioxide, 0.03% relative to the mass of terephthalic acid;
[0035] Matting agent TiO 2 , 0.1% relative to the mass of terephthalic acid.
[0036] The invention discloses a method for preparing a modified polyester raw material of low-strength and low-elongation polyester filament, which is formed through esterification and polycondensation.
[0037] A preparation method of low-strength and low-stretch polyester filaments. The modified polyester is melt-spun and produced through the processes of drawing, cooling, and winding to obtain low-strength and low-stretch polyester filaments; the melt temperature is 270~ 285°C, 4000-6000m / min spinning spee...
Embodiment 2
[0039] Prepare modified polyester, the modified polyester raw material:
[0040] Terephthalic acid;
[0041] Ethylene glycol, relative to terephthalic acid molar ratio 1.4:1;
[0042] Inorganic submicron particles, CaCO 3 or CaSO 4 , 1.0% relative to the mass of terephthalic acid;
[0043] Catalyst, antimony glycol or antimony trioxide, 0.04% relative to the mass of terephthalic acid;
[0044] Matting agent TiO 2 , 0.2% relative to the mass of terephthalic acid.
[0045] The invention discloses a method for preparing a modified polyester raw material of low-strength and low-elongation polyester filament, which is formed through esterification and polycondensation.
[0046] A method for preparing low-strength and low-stretch polyester filaments. The modified polyester is melt-spun and produced through the processes of drawing, cooling and winding to obtain low-strength and low-stretch polyester filaments; the melt temperature is 275°C , under the spinning speed of 4500m / ...
Embodiment 3
[0048] Prepare modified polyester, the modified polyester raw material:
[0049] Terephthalic acid;
[0050] Ethylene glycol, relative to terephthalic acid molar ratio 1.5:1;
[0051] Inorganic submicron particles, CaCO 3 or CaSO 4 , 1.5% relative to the mass of terephthalic acid;
[0052] Catalyst, antimony glycol or antimony trioxide, 0.05% relative to the mass of terephthalic acid;
[0053] Matting agent TiO 2 , 0.3% relative to the mass of terephthalic acid.
[0054]The invention discloses a method for preparing a modified polyester raw material of low-strength and low-elongation polyester filament, which is formed through esterification and polycondensation.
[0055] A method for preparing low-strength and low-stretch polyester filaments. The modified polyester is melt-spun and produced through the processes of drawing, cooling and winding to obtain low-strength and low-stretch polyester filaments; the melt temperature is 285°C , under the spinning speed of 5000m / m...
PUM
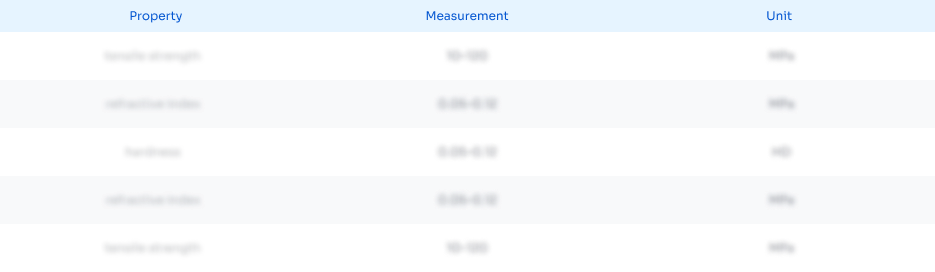
Abstract
Description
Claims
Application Information

- R&D Engineer
- R&D Manager
- IP Professional
- Industry Leading Data Capabilities
- Powerful AI technology
- Patent DNA Extraction
Browse by: Latest US Patents, China's latest patents, Technical Efficacy Thesaurus, Application Domain, Technology Topic, Popular Technical Reports.
© 2024 PatSnap. All rights reserved.Legal|Privacy policy|Modern Slavery Act Transparency Statement|Sitemap|About US| Contact US: help@patsnap.com