X-ray fluorescence spectroscopy analysis fusion sample preparation method of aluminum, manganese, calcium and iron alloy
A technology of fluorescence spectroscopy and fusion sample preparation, which is applied in the field of analysis and detection, can solve the problems of difficult, time-consuming, laborious and cumbersome fusion sample preparation methods, and achieve the effects of accurate and reliable analysis results, expanded application range, and simple operation
- Summary
- Abstract
- Description
- Claims
- Application Information
AI Technical Summary
Problems solved by technology
Method used
Image
Examples
Embodiment 1
[0019] Embodiment 1: This fusion sample preparation method is completed through the following steps:
[0020] 1. Weigh 7.0000g of lithium tetraborate in a platinum crucible, melt it at 1000°C, slowly rotate the crucible after taking it out, and hang a layer of protective wall with a certain height and uniformity in the platinum crucible;
[0021] 2. Weigh 0.2000g aluminum manganese calcium iron test sample, 0.5000g potassium iodide, 2.0000g lithium tetraborate and 1.5000g lithium nitrate, put them into a platinum crucible, and mix well;
[0022] 3. Uniformly cover 2.0000g of lithium tetraborate on the surface of the mixed sample mixture;
[0023] 4. Put the platinum crucible into the muffle furnace that has been heated to 800°C for pre-oxidation. During this process, the platinum crucible should be preheated at the furnace door for 1.5 minutes, and then slowly enter the furnace step by step for about 18 minutes. After the oxidation is complete The sample should be a flowable ...
Embodiment 2
[0026] Embodiment 2: This fusion sample preparation method is completed through the following steps:
[0027] 1. Weigh 5.0000g of lithium tetraborate in a platinum crucible, melt it at 1020°C, slowly rotate the crucible after taking it out, and hang a layer of protective wall with a certain height and uniformity in the platinum crucible;
[0028] 2. Weigh 0.5000g aluminum manganese calcium iron test sample, 0.5000g sodium iodide, 1.0000g mixed flux of 50wt% lithium tetraborate + 50wt% lithium metaborate and 2.5000g lithium carbonate, put them into a platinum crucible, and mix well;
[0029] 3. Put the platinum crucible into the muffle furnace for pre-oxidation by temperature programming. The process is 550°C for 3 minutes, 600°C for 3 minutes, 650°C for 3 minutes, 700°C for 3 minutes, 750°C for 5 minutes, and 800°C. After 5 minutes, the sample should be a flowable liquid after the oxidation is completed, and there are no black particles in the sample;
[0030] 4. Put the oxid...
Embodiment 3
[0032] Embodiment 3: This fusion sample preparation method is completed through the following steps:
[0033] 1. Weigh 8.0000g of lithium tetraborate in a platinum crucible, melt it at 1050°C, slowly rotate the crucible after taking it out, and hang a protective wall with a certain height and uniformity in the platinum crucible;
[0034] 2. Weigh 0.2500g aluminum manganese calcium iron test sample, 0.5000g potassium iodide, 2.5000g potassium nitrate and 3.0000g lithium metaborate, put them into a platinum crucible, and mix well;
[0035] 3. Put the platinum crucible into the muffle furnace that has been heated to 800°C for pre-oxidation. During this process, the platinum crucible should be preheated at the furnace door for 2.0 minutes, and then slowly enter the furnace step by step for about 20 minutes. After the oxidation is complete The sample should be a flowable liquid, and there are no black particles in the sample;
[0036] 4. Put the oxidized sample into the melting fu...
PUM
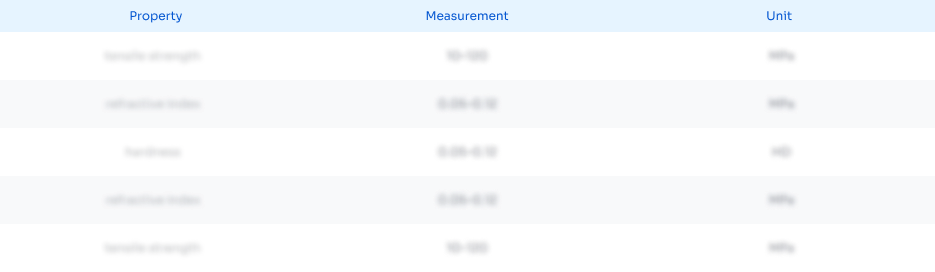
Abstract
Description
Claims
Application Information

- R&D
- Intellectual Property
- Life Sciences
- Materials
- Tech Scout
- Unparalleled Data Quality
- Higher Quality Content
- 60% Fewer Hallucinations
Browse by: Latest US Patents, China's latest patents, Technical Efficacy Thesaurus, Application Domain, Technology Topic, Popular Technical Reports.
© 2025 PatSnap. All rights reserved.Legal|Privacy policy|Modern Slavery Act Transparency Statement|Sitemap|About US| Contact US: help@patsnap.com