High-heat-input welding thick steel plate and manufacturing method thereof
A large heat input welding and manufacturing method technology, applied in the field of manufacturing steel plates for welding, can solve the problems of reducing the toughness of the welding heat-affected zone, reducing the Charpy impact energy of the welding heat-affected zone, etc.
- Summary
- Abstract
- Description
- Claims
- Application Information
AI Technical Summary
Problems solved by technology
Method used
Image
Examples
Embodiment Construction
[0057] The present invention will be further described below in conjunction with embodiment.
[0058] In this embodiment, during the secondary refining process of the molten steel, the alloy composition of the molten steel is adjusted. And deoxidize by adding alloys of corresponding elements in the order of Si, Mn, Al, Ti, Ca. While ensuring the composition of the alloy, adding Fe 2 o 3 The powder controls the oxygen position, and the NiMg alloy is added by wire feeding. The NiMg alloy in the NiMg alloy cored wire contains 5-50% Mg, the balance is Ni, and the grain size is 0.1-5mm.
[0059] Heat the slab to 1250°C, the rough rolling temperature is 1000-1150°C, and the cumulative reduction rate is 50%; the finish rolling temperature is 700-850°C, and the cumulative reduction rate is 67%; / s cooling rate water cooling to the final cooling temperature of 300 ~ 550 ℃.
[0060] The welding thermal simulation test was carried out using a Gleeble3800 thermal simulation testing m...
PUM
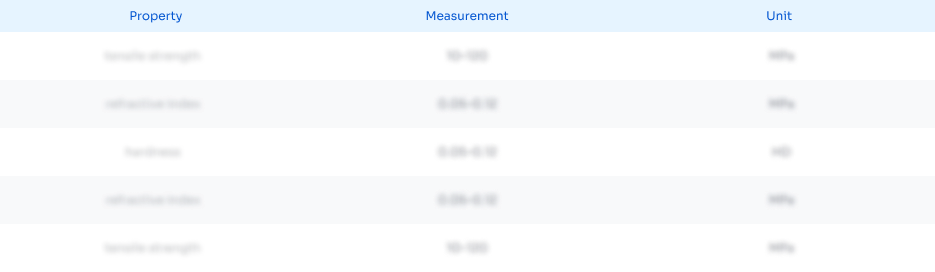
Abstract
Description
Claims
Application Information

- R&D Engineer
- R&D Manager
- IP Professional
- Industry Leading Data Capabilities
- Powerful AI technology
- Patent DNA Extraction
Browse by: Latest US Patents, China's latest patents, Technical Efficacy Thesaurus, Application Domain, Technology Topic, Popular Technical Reports.
© 2024 PatSnap. All rights reserved.Legal|Privacy policy|Modern Slavery Act Transparency Statement|Sitemap|About US| Contact US: help@patsnap.com