Dispersing method of halogen-free flame retardant polypropylene
A technology of flame-retardant polypropylene and polypropylene, which is applied in the field of flame-retardant PP materials, can solve problems such as easy delamination, poor compatibility of flame retardants, and affecting material performance, and achieve the effect of improving compatibility and stabilizing quality
- Summary
- Abstract
- Description
- Claims
- Application Information
AI Technical Summary
Problems solved by technology
Method used
Image
Examples
Embodiment 1
[0041] Premix 59 parts of PP, 35 parts of halogen-free flame retardant, 0.1 part of antioxidant 1010, 0.1 part of antioxidant 168, 5 parts of compatibilizer, and 1 part of ethylene bis fatty acid amide (EBS). Extrusion and granulation are carried out in a twin-screw extruder with an aspect ratio of 40. The processing temperatures are: 170°C, 180°C, 190°C, 190°C, 200°C, 200°C, 200°C, 190°C, 190°C, The head temperature is 190°C.
Embodiment 2
[0043] 57 parts of PP, 35 parts of halogen-free flame retardant, 0.1 part of antioxidant 1010, 0.1 part of antioxidant 168, 5 parts of compatibilizer, 1 part of ethylene bis fatty acid amide (EBS), 3 parts of BYK-9076 Mixing, the above mixture is extruded and granulated in a twin-screw extruder with an aspect ratio of 40. The processing temperatures are: 170°C, 180°C, 190°C, 190°C, 200°C, 200°C, 200°C, 190°C, 190°C, head temperature is 190°C.
Embodiment 3
[0045] 54 parts of PP, 35 parts of halogen-free flame retardant, 0.1 part of antioxidant 1010, 0.1 part of antioxidant 168, 5 parts of compatibilizer, 1 part of ethylene bis fatty acid amide (EBS), 3 parts of BYK-9076, 3 parts of powder BYK-4100 parts are pre-mixed, and the above mixture is extruded and granulated in a twin-screw extruder with an aspect ratio of 40. The processing temperatures are: 170°C, 180°C, 190°C, 190°C, 200°C °C, 200 °C, 200 °C, 190 °C, 190 °C, the head temperature is 190 °C.
[0046] Using the masterbatches obtained in Comparative Examples and Examples 1-3, a sheet of the halogen-free flame-retardant polypropylene composition was prepared, and then its properties were tested. The data are listed in Table 1.
[0047] Table 1
[0048]
[0049] As can be seen from the data listed in Table 1, the mechanical properties of the halogen-free flame-retardant polypropylene composition of the present invention added with a compatibilizer and a dispersant are s...
PUM
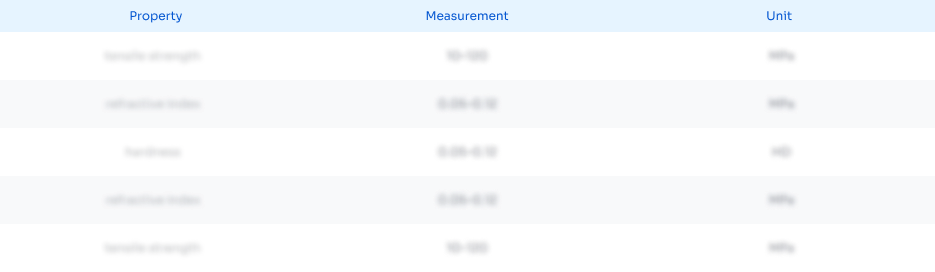
Abstract
Description
Claims
Application Information

- R&D
- Intellectual Property
- Life Sciences
- Materials
- Tech Scout
- Unparalleled Data Quality
- Higher Quality Content
- 60% Fewer Hallucinations
Browse by: Latest US Patents, China's latest patents, Technical Efficacy Thesaurus, Application Domain, Technology Topic, Popular Technical Reports.
© 2025 PatSnap. All rights reserved.Legal|Privacy policy|Modern Slavery Act Transparency Statement|Sitemap|About US| Contact US: help@patsnap.com