Toughened conducting material and preparation method for toughened conducting material
A conductive material and toughening technology, which is applied in the field of toughened conductive materials and their preparation, can solve the problems of reducing the amount of conductive filler, reducing the mechanical properties of materials, and reducing the toughness of materials, so as to improve the electrical conductivity, improve the dispersion effect, and enhance the mechanical properties. performance effect
- Summary
- Abstract
- Description
- Claims
- Application Information
AI Technical Summary
Problems solved by technology
Method used
Image
Examples
Embodiment 1
[0032] 51 parts of polypropylene (parts by weight, the same below), 10 parts of linear low-density polyethylene, 15 parts of ethylene octene copolymer, 5 parts of heavy calcium above 100 mesh, 3.5 parts of grafted maleic anhydride of polypropylene as compatibilizer, silane 0.2 parts of coupling agent, 15 parts of carbon fiber, 10100.3 parts of antioxidant.
[0033] Put polypropylene, linear low-density polyethylene, ethylene octene copolymer, calcium carbonate, polypropylene grafted maleic anhydride, silane coupling agent and antioxidant 1010 into a high-speed mixer according to the above ratio and mix for 5 minutes Take it out, extrude and granulate in the twin-screw extruder, add carbon fiber in the glass fiber feeding port of the twin-screw extruder according to the above ratio, set the temperature of the extruder at 175-215°C, and inject the obtained pellets into The splines were made in the injection molding machine, and the temperature of the injection molding machine wa...
Embodiment 2
[0035] 40 parts of polypropylene, 10 parts of linear low density polyethylene, 20 parts of ethylene octene copolymer, 10 parts of light calcium above 100 mesh, 3.5 parts of polypropylene grafted maleic anhydride, 0.2 parts of aluminate coupling agent Parts, 15 parts of carbon fiber, 1 part of multi-walled carbon nanotube, 10100.3 parts of antioxidant.
[0036] Polypropylene, linear low density polyethylene, ethylene octene copolymer, calcium carbonate, compatibilizer polypropylene grafted maleic anhydride, aluminate coupling agent, multi-walled carbon nanotubes and antioxidant 1010 in the above ratio Put it in a high-speed mixer and mix it for 5 minutes, take it out, extrude and granulate in a twin-screw extruder, add carbon fiber to the glass fiber feeding port of the twin-screw extruder according to the above ratio, and set the temperature of the extruder at 175- At 215°C, the obtained pellets were made into splines in an injection molding machine, and the temperature of the...
Embodiment 3
[0038] 50 parts of polypropylene, 5 parts of linear low density polyethylene, 20 parts of ethylene octene copolymer, 5 parts of light calcium above 100 mesh, 3.5 parts of polypropylene grafted maleic anhydride as compatibilizer, 0.3 parts of titanate coupling agent , 1 part of multi-walled carbon nanotubes, 15 parts of conductive carbon black, and 1680.2 parts of antioxidant.
[0039] Polypropylene, linear low density polyethylene, ethylene octene copolymer, calcium carbonate, compatibilizer polypropylene grafted with maleic anhydride, aluminate coupling agent, multi-walled carbon nanotubes, conductive carbon black and antioxidant 168 is put into the high-speed mixer according to the above ratio and mixed for 5 minutes, then taken out, extruded and granulated in the twin-screw extruder, and the temperature of the extruder is set at 175-215°C, and the obtained pellets are made in the injection molding machine The temperature of the injection molding machine is set at 190-220°C,...
PUM
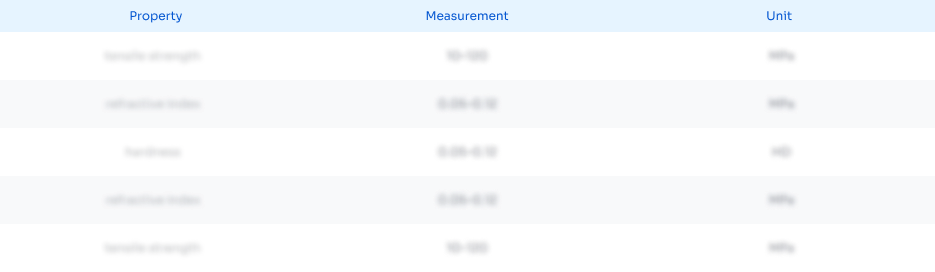
Abstract
Description
Claims
Application Information

- R&D Engineer
- R&D Manager
- IP Professional
- Industry Leading Data Capabilities
- Powerful AI technology
- Patent DNA Extraction
Browse by: Latest US Patents, China's latest patents, Technical Efficacy Thesaurus, Application Domain, Technology Topic, Popular Technical Reports.
© 2024 PatSnap. All rights reserved.Legal|Privacy policy|Modern Slavery Act Transparency Statement|Sitemap|About US| Contact US: help@patsnap.com