Energy-saving dry powder production method for building ceramics
A technology for dry milling and building ceramics, which is applied to clay products, other household appliances, household appliances, etc., can solve problems such as waste and large energy consumption, and achieve the effects of less pollution, saving heat energy, and reducing comprehensive energy consumption indicators.
- Summary
- Abstract
- Description
- Claims
- Application Information
AI Technical Summary
Problems solved by technology
Method used
Image
Examples
Embodiment 1
[0022] Each raw material and its weight percentage are as follows:
[0023] Black mud: 18%
[0024] Tang county soil: 5%
[0025] Cooked: 5%
[0026] Feldspar: 32%
[0027] Porcelain Stone: 35%
[0028] Talc 2%
[0029] High alumina sand: 3%
[0030] Among the above raw materials, the black mud is a soft material, and the others are hard materials.
[0031] Specific steps:
[0032] 1) According to the above ratio, put the black mud and water into the ball mill in a ratio of 6:4, then run the ball mill, grind it until the fineness reaches 325 mesh, and sieve the remaining 1% mud. Depending on the local water quality, an appropriate water reducer should be added during grinding to ensure that the mud has better fluidity.
[0033] 2) Grind the feldspar into 325 mesh with a vertical mill, sieve the remaining 3% fine powder, and put it into the silo for use.
[0034] 3) Grind the porcelain stone into 325 mesh with a vertical mill, sieve the remaining 3% fine powder, and pu...
Embodiment 2
[0045] Each raw material and its weight percentage are as follows:
[0046] Black Mud: 20%
[0047] Hebei soil: 4%
[0048] Tang County Soil: 3.5%
[0049] High alumina sand: 3%
[0050] Porcelain Stone 18.5%
[0051] Feldspar 32%
[0052] Pyrophyllite 8%
[0053] Manzu Stone 4%
[0054] Cooked 6%
[0055] Talc 1%
[0056] Among the above raw materials, the black mud is a soft material, and the others are hard materials.
[0057] Specific steps:
[0058] 1) According to the above ratio, put the black mud and water into the ball mill at a ratio of 5:3, then run the ball mill, grind it until the fineness reaches 370 mesh, and sieve the remaining 2% mud. Depending on the local water quality, an appropriate water reducer should be added during grinding to ensure that the mud has better fluidity.
[0059] 2) Grind the feldspar into 300 mesh with a vertical mill, sieve the remaining 4% fine powder, and put it into the silo for use.
[0060] 3) Grind the porcelain stone i...
Embodiment 3
[0073] Each raw material and its weight percentage are as follows:
[0074]
[0075] Clay is a soft material in the above-mentioned raw materials, and others are hard materials.
[0076] Specific steps:
[0077] 1) According to the above ratio, put clay and water into the ball mill at a ratio of 5:4, then run the ball mill, grind it until the fineness reaches 400 mesh, and sieve the remaining 3% mud. Depending on the local water quality, an appropriate water reducer should be added during grinding to ensure that the mud has better fluidity.
[0078] 2) Grind the diopside into 250 mesh with a vertical mill, sieve the remaining 8% fine powder, and put it into the silo for use.
[0079] 3) Grind the porcelain stone into 250 mesh with a vertical mill, sieve the remaining 8% fine powder, and put it into the silo for use.
[0080] 4) Grind the gravel into 250 mesh with a vertical mill, sieve the remaining 8% fine powder, and put it into the silo for use.
[0081] 5) Grind the...
PUM
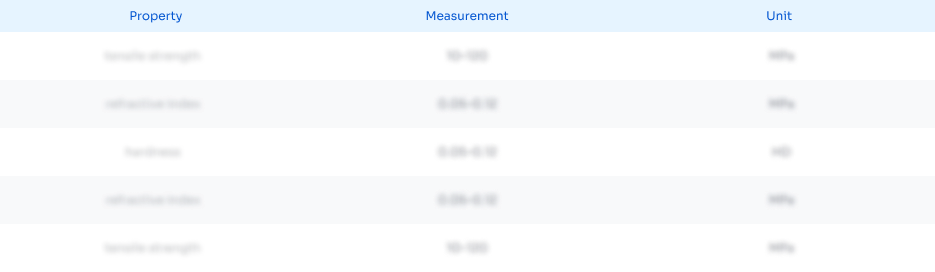
Abstract
Description
Claims
Application Information

- Generate Ideas
- Intellectual Property
- Life Sciences
- Materials
- Tech Scout
- Unparalleled Data Quality
- Higher Quality Content
- 60% Fewer Hallucinations
Browse by: Latest US Patents, China's latest patents, Technical Efficacy Thesaurus, Application Domain, Technology Topic, Popular Technical Reports.
© 2025 PatSnap. All rights reserved.Legal|Privacy policy|Modern Slavery Act Transparency Statement|Sitemap|About US| Contact US: help@patsnap.com