Method for preparing pollution-resistant low-pressure reverse osmosis membrane
A low-pressure reverse osmosis and pollution-resistant technology, applied in semi-permeable membrane separation, chemical instruments and methods, membrane technology, etc., can solve problems such as poor backwash resistance and poor stability, and achieve reduced organic adhesion, strong stability, The effect of improving hydrophilicity
- Summary
- Abstract
- Description
- Claims
- Application Information
AI Technical Summary
Problems solved by technology
Method used
Examples
Embodiment 1
[0022] In a reaction kettle equipped with 50 g / L of polyvinyl alcohol aqueous solution with a degree of hydrolysis (referring to the degree of hydrolysis of vinyl acetate in polyvinyl alcohol molecules) of 99%, add mass percentage (referring to N,N-dimethyl N -(2-methacryloyloxyethyl)N-(2-sulfoethyl)ammonium accounted for the mass percent of the total mass of polyvinyl alcohol aqueous solution) concentration of 20% N,N-dimethyl N-(2- Methacryloyloxyethyl) N-(2-sulfoethyl)ammonium, under nitrogen protection, add potassium persulfate-sodium bisulfite (potassium persulfate and sodium bisulfite quality) with a mass percentage concentration of 0.25% The ratio is 1.0:1.0), reacted at 55°C for 5 hours, the reaction product was precipitated and washed with acetone, dried at 60°C for 3 hours, and crushed to obtain polyvinyl alcohol grafted zwitterionic copolymer, which was set aside;
[0023] Immerse the polysulfone porous membrane in a m-phenylenediamine aqueous solution with a concen...
Embodiment 2
[0027] In a reaction kettle equipped with 50 g / L of polyvinyl alcohol aqueous solution with a degree of hydrolysis of 88%, add N,N-dimethyl N-(2-methacryloyloxyethyl) with a concentration of 35% by mass ) N-(2-sulfoethyl) ammonium, under the protection of nitrogen, add potassium persulfate-sodium bisulfite with a mass percentage concentration of 1% (the mass ratio of potassium persulfate to sodium bisulfite is 1.0:1.5), React at 55°C for 3 hours, the reaction product is precipitated and washed with acetone, dried at 80°C for 3 hours, and pulverized to obtain a polyvinyl alcohol grafted zwitterionic copolymer, which is set aside;
[0028] Immerse the polysulfone porous membrane in an aqueous m-phenylenediamine solution with a concentration of 5wt / v for 1 minute, take out and remove the excess solution on the surface; then immerse it in a solution with a concentration of 0.5wt / v trimesoyl chloride In n-hexane solution, react for 1 minute; then cure in an oven at 60°C for 20 minu...
Embodiment 3
[0032]In a reactor equipped with 50 g / L of polyvinyl alcohol aqueous solution with a degree of hydrolysis of 88%, add N,N-dimethyl N-(2-methacryloyloxyethyl) with a concentration of 30% by mass ) N-(2-sulfoethyl) ammonium, under the protection of nitrogen, add potassium persulfate-sodium bisulfite with a mass percentage concentration of 0.3% (the mass ratio of potassium persulfate to sodium bisulfite is 1.0:2.0), React at 55°C for 4 hours, the reaction product is precipitated and washed with acetone, dried at 60°C for 3 hours, and pulverized to obtain a polyvinyl alcohol grafted zwitterionic copolymer, which is set aside;
[0033] Immerse the polysulfone porous membrane in a m-phenylenediamine aqueous solution with a concentration of 2wt / v for 0.5 minutes, take out and remove the excess solution on the surface; In n-hexane solution, react for 1 minute; then cure in an oven at 50°C for 30 minutes; finally soak in deionized water to obtain a polyamide film for later use;
[003...
PUM
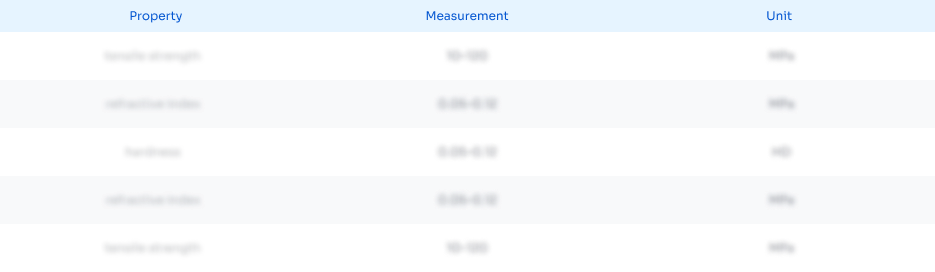
Abstract
Description
Claims
Application Information

- R&D
- Intellectual Property
- Life Sciences
- Materials
- Tech Scout
- Unparalleled Data Quality
- Higher Quality Content
- 60% Fewer Hallucinations
Browse by: Latest US Patents, China's latest patents, Technical Efficacy Thesaurus, Application Domain, Technology Topic, Popular Technical Reports.
© 2025 PatSnap. All rights reserved.Legal|Privacy policy|Modern Slavery Act Transparency Statement|Sitemap|About US| Contact US: help@patsnap.com