Industrial production method for synthesizing cemented carbide block material in situ
A cemented carbide block and in-situ synthesis technology, applied in the field of cemented carbide, can solve the problems of large energy consumption, long process, complex process, etc., and achieve strong controllability, short process, and reduction of waste gas and waste liquid The effect of emissions
- Summary
- Abstract
- Description
- Claims
- Application Information
AI Technical Summary
Problems solved by technology
Method used
Image
Examples
example 1
[0030] Example 1: The final product is WC-6wt.% Co (YG6) cemented carbide bulk material. According to the requirements of Co content in YG6 cemented carbide, according to the actual conditions of Co loss of 1.5% (m=1.5), total carbon content increased by 0.2% (p=0.2) and material loss coefficient of k=1.02 in hot pressing sintering, according to The mass ratio is 110.81:8.28:24.20 with WO 2.9 、Co 3 o 4 Ball milling and mixing with carbon black, and then according to the ratio of the mass of the sintered sample to the mass of the mixed powder is 1:1.29, the mixed oxide powder is weighed and filled into a mold, and sintered in a hot-press sintering furnace. The hot-pressing sintering process parameters are: pressure 10MPa, heating up to 375°C at a heating rate of 30°C / min, and holding for 1 hour; then raising the temperature to 1000°C, holding for 3 hours; ℃, and increase the pressure to 30MPa, keep the temperature and pressure for 60 minutes; finally keep the pressure and co...
example 2
[0031] Example 2: The final product is WC-10wt.% Co (YG10) cemented carbide bulk material. According to the requirements of Co content in YG10 cemented carbide, according to the actual conditions of Co loss in vacuum sintering of 0.3% (m=0.3), total carbon content increased by 0.15% (p=0.15) and material loss coefficient of k=1.00, according to the actual conditions The ratio of WO is 106.16:13.64:23.64 2.9 、Co 3 o 4 Carry out ball milling and mixing with carbon black, weigh the oxide mixed powder according to the ratio of sintered sample mass to mixed powder mass ratio of 1:1.22, fill it into a mold for cold pressing, and sinter the mold and powder together in vacuum Sintering in the furnace. The process parameters of vacuum sintering are as follows: heat up to 375°C and hold for 1 hour; then raise the temperature to 950°C at a rate of 8°C / min and hold for 2 hours; then raise the temperature to 1400°C and hold for 1.5 hours; finally cool down to room temperature with the f...
example 3
[0032] Example 3: The final product is WC-15wt.% Co (YG15) cemented carbide bulk material. According to the requirements of Co content in YG15 cemented carbide, according to the actual conditions of Co loss 2.5% (m=2.5) in low pressure sintering, total carbon content increased by 0.3% (p=0.3) and material loss coefficient k=1.05, according to the actual conditions The ratio of WO is 99.86:20.91:22.05 2.9 、Co 3 o 4 Ball milling and mixing with carbon black, according to the ratio of sintered sample mass to mixed powder mass ratio of 1:1.20, the oxide mixed powder is weighed and filled into a mold, and sintered in a low-pressure sintering furnace. The sintering process parameters are as follows: heat up to 400°C for 1 hour; then heat up to 980°C at a rate of 7°C / min and hold for 3 hours; Inject 5MPa argon gas, keep the temperature and pressure for 30 minutes; finally cool down to room temperature with the furnace. The XRD spectrum and microstructure of the YG15 cemented carb...
PUM
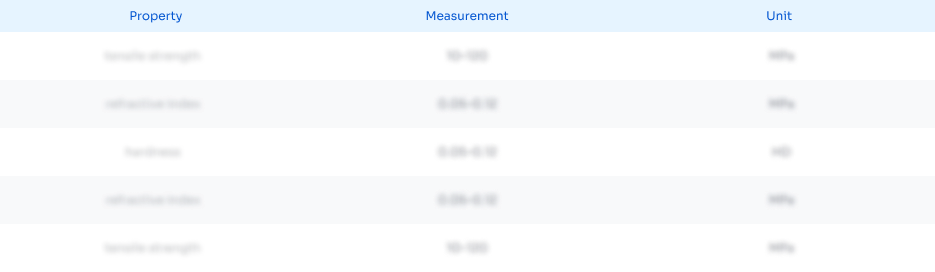
Abstract
Description
Claims
Application Information

- R&D Engineer
- R&D Manager
- IP Professional
- Industry Leading Data Capabilities
- Powerful AI technology
- Patent DNA Extraction
Browse by: Latest US Patents, China's latest patents, Technical Efficacy Thesaurus, Application Domain, Technology Topic, Popular Technical Reports.
© 2024 PatSnap. All rights reserved.Legal|Privacy policy|Modern Slavery Act Transparency Statement|Sitemap|About US| Contact US: help@patsnap.com