Artificial Fireproof polyvinyl chloride (PVC) leather for cushion furniture and preparation method thereof
A polyvinyl chloride and artificial leather technology, applied in textiles, papermaking, fiber processing and other directions, can solve the problems of reducing the comfort of upholstered furniture products, complex fire-resistant upholstered furniture processes, and no long-term fire resistance, saving raw materials, Excellent fire resistance and wide range of materials
- Summary
- Abstract
- Description
- Claims
- Application Information
AI Technical Summary
Problems solved by technology
Method used
Image
Examples
Embodiment 1
[0033] First, 100 parts of polyvinyl chloride resin powder, 1.6 parts of zinc stearate, 1.5 parts of calcium stearate, 30 parts of bis(2-ethyl)hexyl phthalate, 5 parts of epoxy soybean oil, trimethylbenzene phosphate 12 parts of ester TCP, 11 parts of antimony trioxide, 15 parts of calcium carbonate, 15 parts of ammonium polyphosphate, 8 parts of pentaerythritol, and 8 parts of melamine were put into a high-speed mixer and mixed evenly, and then put into an internal mixer for 3 minutes of mastication , then put 3.2 parts of azodicarbonamide, 1.5 parts of 4,4'-oxobisbenzenesulfonyl hydrazide, 1.5 parts of zinc oxide and 1.5 parts of borax into the internal mixer to continue mixing for 30 seconds, and then put it into a double The tab is mixed on the roller mill, and then the mixed tab material is transported to a calender at a temperature of 170°C through an extrusion feeder for calendering and compounded with a fireproof treated cloth base to form artificial leather.
[0034] ...
Embodiment 2
[0037] First, 100 parts of polyvinyl chloride resin powder, 1.5 parts of di-n-butyltin dilaurate, 0.5 parts of di-n-octyltin maleate, 35 parts of diisononyl phthalate, 20 parts of trioctyl phosphate, and 20 parts of kaolin, 18 parts of talcum powder, 15 parts of wollastonite, 20 parts of oligophosphate flame retardant, and 15 parts of perlite were mixed evenly in a high-speed mixer, and then put into an internal mixer for 3 minutes of mastication. 5 parts of diisopropyl nitrogen dicarboxylate, 1.7 parts of p-toluenesulfonyl hydrazide, 5 parts of calcium oxide, and 2.5 parts of salicylic acid were put into the internal mixer and continued to mix for 30 seconds, and then put into a double-roller plastic mixer with a constant temperature of 150°C for mixing. Pull the sheet, and then transport the mixed pull sheet material to a calender with a temperature of 175°C through an extrusion feeder for calendering and compound it with a fireproof treated cloth base to form artificial leat...
Embodiment 3
[0041] First, 100 parts of polyvinyl chloride resin powder, 2.5 parts of liquid barium-zinc composite stabilizer, 20 parts of trioctyl phosphate, 10 parts of epoxy soybean oil, 25 parts of zinc borate, 40 parts of silica lime, 10 parts of potassium hexametaphosphate, Put 10 parts of volcanic ash into a high-speed mixer and mix evenly, then put it into an internal mixer and masticate for 4 minutes, then add 4.5 parts of azodicarbonamide, 2.5 parts of disulfonyl hydrazide diphenyl sulfone, and 4 parts of potassium perchlorate. Put it into the internal mixer and continue mixing for 30 seconds, put it into a 145°C constant temperature double-roller plastic mixer to mix the tabs, and then transport the mixed tabs to a calender at a temperature of 175°C through an extrusion feeder for calendering and Fireproof treated cloth base composite artificial leather.
[0042] The cloth base of fireproofing treatment adopts cotton / polyester cloth base (polyester content less than 15%) on the ...
PUM
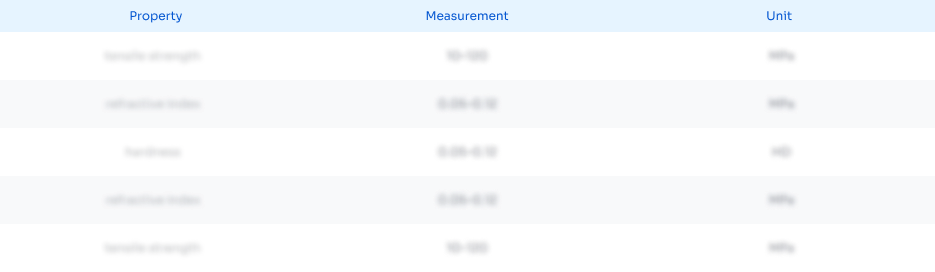
Abstract
Description
Claims
Application Information

- Generate Ideas
- Intellectual Property
- Life Sciences
- Materials
- Tech Scout
- Unparalleled Data Quality
- Higher Quality Content
- 60% Fewer Hallucinations
Browse by: Latest US Patents, China's latest patents, Technical Efficacy Thesaurus, Application Domain, Technology Topic, Popular Technical Reports.
© 2025 PatSnap. All rights reserved.Legal|Privacy policy|Modern Slavery Act Transparency Statement|Sitemap|About US| Contact US: help@patsnap.com