Production method of insulating brick containing plant straws
A technology for thermal insulation bricks and straws, which is applied in the field of thermal insulation bricks, can solve the problems of low fire resistance of auxiliary materials, unenvironmental binders, etc., and achieves good seismic effect, convenient and fast construction, and low density.
- Summary
- Abstract
- Description
- Claims
- Application Information
AI Technical Summary
Problems solved by technology
Method used
Image
Examples
Embodiment 1
[0020] The plant straw-containing thermal insulation brick composed of the raw materials in the following proportions by weight:
[0021] 70 parts of plant straw, 20 parts of magnesium hydroxide, 10 parts of isocyanate,
[0022] Preparation method: crush plant straw with a moisture content of 15% by weight into fibers with a length of 5 to 10 mm, dry until the moisture content is 8% by weight, weigh the plant straw according to the weight percentage, and press Add magnesium hydroxide and binder isocyanate to the parts by weight, stir and mix ingredients, and then pre-press, the pre-press pressure is 500 tons, and then mold compression molding, the molding pressure is 1.2 thousand tons, using high-frequency electromagnetic induction Method, heating to 110 ° C, hot pressing for 4 to 5 minutes to shape.
Embodiment 2
[0024] The plant straw-containing thermal insulation brick composed of the raw materials in the following proportions by weight:
[0025] 80 parts of plant straw, 15 parts of magnesium hydroxide, 5 parts of isocyanate,
[0026] Preparation method: adopt high-frequency electromagnetic induction method, heat to 110°C, hot press for 4-5 minutes to form, and the rest of the method and steps are the same as in Example 1.
[0027] The preparation method is the same as in Example 1.
[0028] Table: raw material component and performance index of embodiment
[0029]
PUM
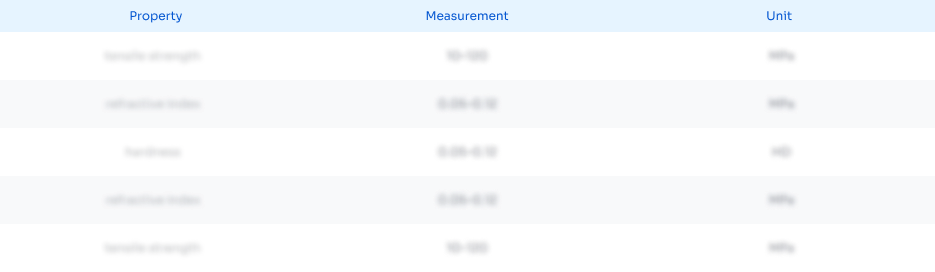
Abstract
Description
Claims
Application Information

- Generate Ideas
- Intellectual Property
- Life Sciences
- Materials
- Tech Scout
- Unparalleled Data Quality
- Higher Quality Content
- 60% Fewer Hallucinations
Browse by: Latest US Patents, China's latest patents, Technical Efficacy Thesaurus, Application Domain, Technology Topic, Popular Technical Reports.
© 2025 PatSnap. All rights reserved.Legal|Privacy policy|Modern Slavery Act Transparency Statement|Sitemap|About US| Contact US: help@patsnap.com