Lightweight soundproof thermal insulation wall brick and preparation method thereof
A wall brick, lightweight technology, applied in the field of building filling materials, can solve the problems of high density and low strength of foam bricks, and achieve the effect of good corrosion resistance and fire resistance
- Summary
- Abstract
- Description
- Claims
- Application Information
AI Technical Summary
Problems solved by technology
Method used
Examples
Embodiment 1
[0015] Example 1, Preparation of raw materials, every 1 m 3 The raw materials required for wall bricks are as follows: silica sand 180Kg, cement 85Kg, lime 40Kg, phosphogypsum 20Kg, coal ash 30Kg, water 340Kg, aluminum powder 0.41Kg, mica powder 28.4Kg.
[0016] Preparation Process:
[0017] 1. Weigh the ingredients according to the proportion, grind all the materials except aluminum powder into powder, mix at a temperature of 38℃, add water and stir, add aluminum powder after complete mixing, and stir for 40 seconds;
[0018] 2. Heat to 58°C for foaming, the foaming time is 150 minutes;
[0019] 3. Divide into blocks;
[0020] 4. After dividing, enter the steam room for steaming, the steaming pressure is 1.2-1.4MPa, the steaming temperature is 200℃, and the steaming time is 8 hours.
Embodiment 2
[0021] Example 2: Preparation of raw materials, every 1 m 3 The raw materials required for wall bricks are as follows: silica sand 185Kg, cement 87Kg, lime 42Kg, phosphogypsum 24Kg, coal ash 31Kg, water 330Kg, aluminum powder 0.43Kg, mica powder 28.6Kg.
[0022] Preparation Process:
[0023] 1. Weigh the ingredients according to the proportion, grind all the materials except aluminum powder into powder, mix at a temperature of 38℃, add water and stir, add aluminum powder after complete mixing, and stir for 40 seconds;
[0024] 2. Heat to 59°C for foaming, the foaming time is 140 minutes;
[0025] 3. Divide into blocks;
[0026] 4. After dividing, enter the steam room for steaming, the steaming pressure is 1.2-1.4MPa, the steaming temperature is 210℃, and the steaming time is 8 hours.
Embodiment 3
[0027] Example 3: Preparation of raw materials, every 1 m 3 The raw materials required for wall bricks are as follows: silica sand 190Kg, cement 85Kg, lime 35Kg, phosphogypsum 17Kg, coal ash 30Kg, aluminum powder 0.5Kg, mica powder 30Kg, and water 360Kg. .
[0028] Preparation Process:
[0029] 1. Weigh the ingredients according to the ratio, grind all the materials except aluminum powder into powder, mix at 38℃, add water and stir, add aluminum powder after complete mixing, and stir for 45 seconds;
[0030] 2. Heat to 59°C for foaming, and the foaming time is 150 minutes;
[0031] 3. Divide into blocks;
[0032] 4. After dividing, enter the steam room for steaming, the steaming pressure is 1.2-1.4MPa, the steaming temperature is 220℃, and the steaming time is 8 hours.
PUM
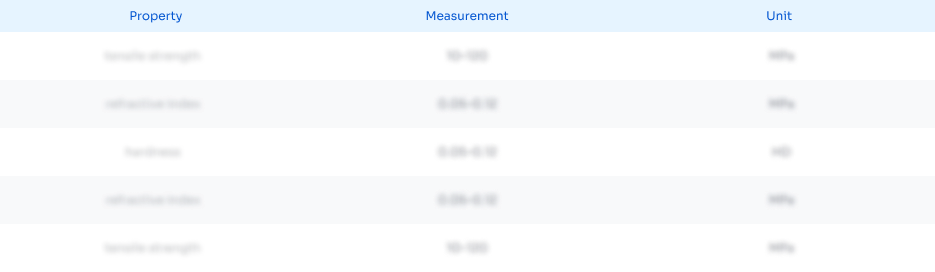
Abstract
Description
Claims
Application Information

- Generate Ideas
- Intellectual Property
- Life Sciences
- Materials
- Tech Scout
- Unparalleled Data Quality
- Higher Quality Content
- 60% Fewer Hallucinations
Browse by: Latest US Patents, China's latest patents, Technical Efficacy Thesaurus, Application Domain, Technology Topic, Popular Technical Reports.
© 2025 PatSnap. All rights reserved.Legal|Privacy policy|Modern Slavery Act Transparency Statement|Sitemap|About US| Contact US: help@patsnap.com