Ablation-resisting composite material resin composition and preparation method of ablation-resisting composite material
A technology of resin composition and composite materials, applied in the field of polymer composite materials preparation, can solve the problems of high brittleness and poor performance, and achieve the effects of high thermal stability, high mechanical properties and ablation resistance
- Summary
- Abstract
- Description
- Claims
- Application Information
AI Technical Summary
Problems solved by technology
Method used
Image
Examples
preparation example Construction
[0036] The preparation method of the above-mentioned composite material is as follows: 100 grams of weighed polyphenoxyphosphazene (PPP) and boron phenolic resin (BPR) are respectively dissolved in 1 liter of tetrahydrofuran, and after the dissolution is complete, they are mixed into a uniform solution, and then coated with On the carbon fiber plain weave cloth, after drying, put it into a vacuum oven for 12 hours at 50°C. Cut the fiber cloth into 10cm×10cm squares, stack them together and put them into the mold, heat them with a flat vulcanizer at 100°C for 1 hour to completely melt the boron phenolic resin, then raise the temperature to 120°C for pre-curing for 1 hour, and finally After raising the temperature to 180°C and a pressure of 5 MPa for 6 hours, take it out and cool it to room temperature.
[0037] The ablation-resistant composite material prepared in the embodiment of the present invention has high mechanical properties and ablation resistance, and can be used in ...
Embodiment 1
[0048] This embodiment provides an ablation-resistant composite material resin composition, which can be used to prepare ablation-resistant composite materials used in the fields of aerospace vehicles, missiles, rocket engines, etc., and the composition includes the raw materials in the following table;
[0049]
[0050] The method for preparing the composite material is: dissolve the weighed polyphenoxyphosphazene (PPP) (30g) and boron phenolic resin (BPR) (70g) in 1 liter of tetrahydrofuran respectively, and mix them into a uniform solution after dissolving completely , and then coated on carbon fiber plain cloth (3K plain cloth), after drying, put it in a vacuum oven at 50°C for 12 hours; cut the fiber cloth into squares of 10cm×10cm, stack them together and put them into the mold, and use Heat the plate vulcanizer at 100°C for 1 hour to completely melt the boron phenolic resin, then raise the temperature to 120°C for pre-curing for 1 hour, and finally raise the temperatu...
Embodiment 2
[0052] This embodiment provides an ablation-resistant composite material resin composition, which can be used to prepare ablation-resistant composite materials used in the fields of aerospace vehicles, missiles, rocket engines, etc., and the composition includes the raw materials in the following table;
[0053]
[0054] The method for preparing the composite material is: dissolve the weighed polyphenoxyphosphazene (PPP) (40g) and boron phenolic resin (BPR) (60g) in 1 liter of tetrahydrofuran respectively, and mix them into a uniform solution after the dissolution is complete , and then coated on carbon fiber plain cloth (3K plain cloth), after drying, put it in a vacuum oven at 50°C for 12 hours; cut the fiber cloth into squares of 10cm×10cm, stack them together and put them into the mold, and use Heat the plate vulcanizer at 100°C for 1 hour to completely melt the boron phenolic resin, then raise the temperature to 120°C for pre-curing for 1 hour, and finally raise the tem...
PUM
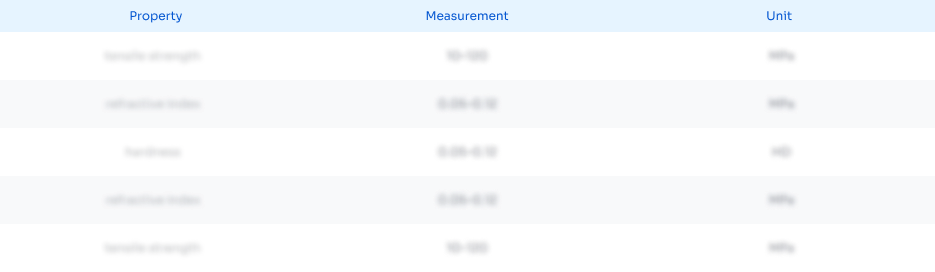
Abstract
Description
Claims
Application Information

- R&D Engineer
- R&D Manager
- IP Professional
- Industry Leading Data Capabilities
- Powerful AI technology
- Patent DNA Extraction
Browse by: Latest US Patents, China's latest patents, Technical Efficacy Thesaurus, Application Domain, Technology Topic, Popular Technical Reports.
© 2024 PatSnap. All rights reserved.Legal|Privacy policy|Modern Slavery Act Transparency Statement|Sitemap|About US| Contact US: help@patsnap.com