High-temperature fireproof kiln material and preparing method thereof
A high-temperature refractory and kiln furniture technology, applied in the field of refractory materials, can solve problems that affect the service life and quality of kiln furniture, large shrinkage of kiln furniture materials, poor thermal shock resistance, etc., and achieve strong thermal shock resistance and air holes Dense, easily controlled effects
- Summary
- Abstract
- Description
- Claims
- Application Information
AI Technical Summary
Problems solved by technology
Method used
Image
Examples
Embodiment 1
[0038] A high-temperature refractory kiln furniture material, which includes the following components in parts by weight:
[0039]
[0040] Wherein, the secondary calcined porcelain material is prepared by the following method:
[0041] (1) In parts by weight, 93 parts of aluminum oxide, 3 parts of calcium carbonate, 1.5 parts of kaolin, 1.6 parts of silicon micropowder and 0.8 part of chromium oxide are batched and ball milled, mixed and pulverized to 300-400 mesh;
[0042] (2) 13 parts of paraffin, 0.4 part of oleic acid are heated to melting;
[0043] (3) After removing water from the raw materials in step (1), add the melted paraffin wax and oleic acid in step (2), mix them evenly, and mold them by hot die casting at 0.5MP and 60-70°C.
[0044] (4) Discharging wax and firing to get the finished product.
[0045] The preparation method of the above-mentioned warm refractory kiln furniture material comprises the following steps:
[0046] 1. Measure raw materials accord...
Embodiment 2
[0059] A high-temperature refractory kiln furniture material, which includes the following components in parts by weight:
[0060]
[0061] Wherein, the secondary cooked porcelain material is prepared by the following method:
[0062](1) In parts by weight, 90 parts of aluminum oxide, 2 parts of calcium carbonate, 1 part of kaolin, 1.2 parts of silicon micropowder and 0.2 part of chromium oxide are batched and then ball milled, mixed and crushed to 300-400 meshes;
[0063] (2) heating 10 parts of paraffin and 0.2 part of oleic acid to melting;
[0064] (3) After removing water from the raw materials in step (1), add the melted paraffin wax and oleic acid in step (2), mix them evenly, and then use hot die casting to form at 0.5MP and 60-70°C.
[0065] (4) Discharging wax and firing to get the finished product.
[0066] The preparation method of the above-mentioned warm refractory kiln furniture material comprises the following steps:
[0067] 1. Measure raw materials acco...
Embodiment 3
[0080] A high-temperature refractory kiln furniture material, which includes the following components in parts by weight:
[0081]
[0082]
[0083] Wherein, the secondary calcined porcelain material is prepared by the following method:
[0084] (1) In parts by weight, 92 parts of aluminum oxide, 2 parts of calcium carbonate, 1 part of kaolin, 1.2 parts of silicon micropowder and 1.5 parts of chromium oxide are batched and ball milled, mixed and pulverized to 300-400 mesh;
[0085] (2) 12 parts of paraffin and 0.2 part of oleic acid are heated to melt;
[0086] (3) After removing water from the raw materials in step (1), add the melted paraffin wax and oleic acid in step (2), mix them evenly, and then use hot die casting to form at 0.5MP and 60-70°C.
[0087] (4) Discharging wax and firing to get the finished product.
[0088] The preparation method of the above-mentioned warm refractory kiln furniture material comprises the following steps:
[0089] 1. Measure raw ma...
PUM
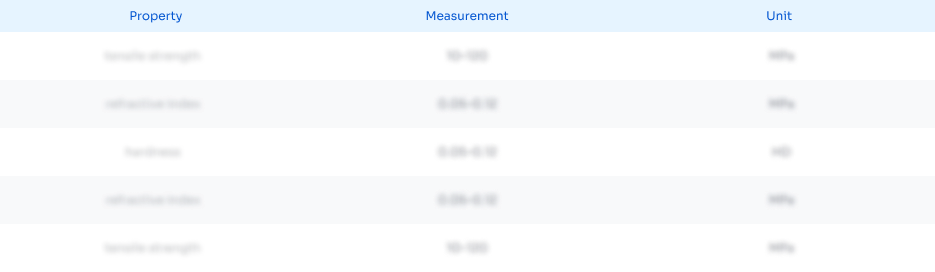
Abstract
Description
Claims
Application Information

- Generate Ideas
- Intellectual Property
- Life Sciences
- Materials
- Tech Scout
- Unparalleled Data Quality
- Higher Quality Content
- 60% Fewer Hallucinations
Browse by: Latest US Patents, China's latest patents, Technical Efficacy Thesaurus, Application Domain, Technology Topic, Popular Technical Reports.
© 2025 PatSnap. All rights reserved.Legal|Privacy policy|Modern Slavery Act Transparency Statement|Sitemap|About US| Contact US: help@patsnap.com