Production method for formable polyimide film
A technology of polyimide film and production method, which is applied in the production field of formable polyimide film, can solve the problems of unsatisfactory market development, poor formability, low mechanical strength, etc., and achieve excellent physical properties and self-lubrication Good performance and high mechanical strength
- Summary
- Abstract
- Description
- Claims
- Application Information
AI Technical Summary
Problems solved by technology
Method used
Image
Examples
Embodiment 1
[0017] The production method of a moldable polyimide film provided by this embodiment includes resin synthesis, defoaming, salivation film formation and winding and cutting, and the resin synthesis is 4,4'-dimethyl Press acetamide into the amine melting kettle, then meter the mixed 4,4'-diaminodiphenyl ether + p-phenylenediamine + 4,4'-diaminodiphenylmethane mixture into the amine melting kettle, and stir for 1 Hours, the mixture was completely dissolved in 4,4'-dimethylacetamide, and then the solution was hydraulically poured into the reactor, and the measured 4,4'-oxydiphthalic anhydride + 3,3' , 4,4'-biphenyltetracarboxylic dianhydride + pyromellitic dianhydride mixture is added to the reactor, reacted for 4 hours to form a sol-type polyamic acid resin, adjust the resin viscosity by adjusting the amount of residual anhydride; the test viscosity reaches About 30000cP to 100000cP is enough; the raw materials are composed of: 40 parts of 4,4'-oxydiphthalic anhydride, 20 parts ...
Embodiment 2
[0024] The production method of the formable polyimide film described in this example, the composition of its raw materials is: 30 parts of 4,4'-oxydiphthalic anhydride, 3,3',4,4'-biphenyl tetra Formic dianhydride 10, pyromellitic dianhydride 30; 4,4'-diaminodiphenyl ether 20, p-phenylenediamine 30, 4,4'-diaminodiphenylmethane 20 parts, the production method is the same as in Example 1 .
[0025] The moldable polyimide film obtained by the production method of the moldable polyimide film provided in this embodiment has a performance parameter of:
[0026] Performance parameter table
[0027]
[0028] Note: Tensile strength, elongation at break, and dielectric strength are the average values of multiple measurements.
Embodiment 3
[0030] The production method of the formable polyimide film described in this example, the composition of its raw materials is: 50 parts of 4,4'-oxydiphthalic anhydride, 3,3',4,4'-biphenyl tetra 30 parts of formic dianhydride, 50 parts of pyromellitic dianhydride; 40 parts of 4,4'-diaminodiphenyl ether, 50 parts of p-phenylenediamine, 40 parts of 4,4'-diaminodiphenylmethane. Production method is with embodiment 1.
[0031] The moldable polyimide film obtained by the production method of the moldable polyimide film provided in this embodiment has a performance parameter of:
[0032] Performance parameter table
[0033]
[0034]
[0035] Note: Tensile strength, elongation at break, and dielectric strength are the average values of multiple measurements.
PUM
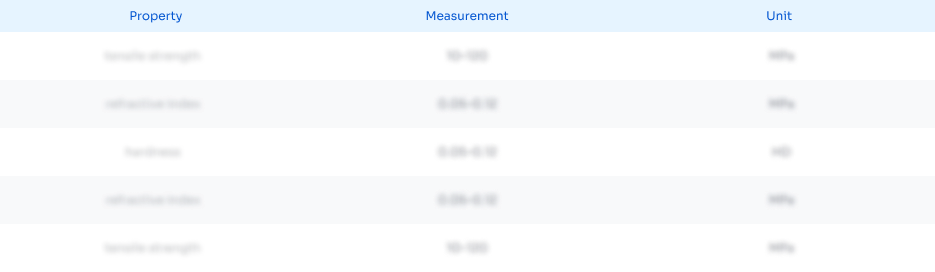
Abstract
Description
Claims
Application Information

- Generate Ideas
- Intellectual Property
- Life Sciences
- Materials
- Tech Scout
- Unparalleled Data Quality
- Higher Quality Content
- 60% Fewer Hallucinations
Browse by: Latest US Patents, China's latest patents, Technical Efficacy Thesaurus, Application Domain, Technology Topic, Popular Technical Reports.
© 2025 PatSnap. All rights reserved.Legal|Privacy policy|Modern Slavery Act Transparency Statement|Sitemap|About US| Contact US: help@patsnap.com